Comprehensive Bow Drill
Description
http://www.selfrelianceoutfitters.com
The Pathfinder School,Bush Craft ,Survival skills, Historical Lore, Primitive Skills, Archery, Hunting, Trapping, Fishing, Navigation, Knives, Axes, Fire, Water, Shelter, Search and Rescue
Tags: Bushcraft,Survival,David Canterbury,Dave Canterbury,Pathfinder,The Pathfinder School,Archery,Hunting,Fishing,Camping,Primitive Skills,Fire,Water,Shelter,Navigation,First Aid,Search and Rescue,Signaling,Prepper,Preparedness,Self Reliance,Survivability,The 10 C's,Knives,Axes,Saws,Bow Drill,Ferrocerium Rod,Ferro Rod,Tarp,Hammock,Canteen,Cooking,Longhunter,Trapping
Video Transcription
morning folks I'm Dave Canterbury with self-reliance outfitters in the pathfinder school obviously out here at the school property underneath the classroom overhang
what I thought I would do today is I've got a book that I'm in the middle of right now and middle of writing and the manuscript is due here in about 15 days but it's an illustrated book about bushcraft and it's gonna have lots and lots of illustrations within that book and one of the things that I wanted to strive for with this book was to have several illustrations created that really aren't out there the way I think they should be Illustrated there's lots and lots of bow-drill illustrations out there that are just one picture of the guy over the top of the set or maybe a picture of a few components but there's really nothing that shows how that set should actually look and with up-close pictures of things like the knotch the underside of the board the thickness of the board all those types of things come into play but again they're also material dependent and that's the hardest thing about teaching the bow drill to a mass audience like on the internet because there's so many different materials out there some of them work way better than others some of them you can almost get a coal out of by accident as long as they're dry Cedars are a good example of that cedar is a very very easy wood to get a bow drill number off of and then if you go out west of course where most people practice the hand drill it's because everything out there is so dry and it's easier to get an ember with a hand drill out there it can be done in Eastern woodlands but the fact that you have mechanical advantage with the bow drill and you can overcome some of the humidity factors and moisture factors in the Eastern woodlands makes the bow drill a better option I think for people to learn in Eastern woodlands however like I said there's not a whole lot of comprehensive photographs or images or illustrations out there of exactly how to do that so I thought what I do today is to make a long story short while I am setting this bow drill set up to take photographs I thought I would also try to shoot some short video to kind of show you up close what some of those components are supposed to look like and then we'll go and make an ember with this set stay with me okay so I just split a poplar log and you can see this pith line running through the middle and then you can see the heartwood separating from the SAP wood the more of this SAP wood I can get to using my bow drill set they're better off it's going to be as I get closer and closer to the pith or the dead wood the more dense the material is going to be other than the pith itself so this area of yellow and kind of a purplish heartwood here is going to be dense compared to this outer white wood so if I can find a piece of that white wood that's wide enough to get my bow drill into even if I'm just touching this green that's okay but I don't want to make it in this area I want it over here so I have to think about that when I'm making my board to begin with and I want that board to be about the thickness of my finger when it's finished okay this is the center of that log you have this on one side and this on the other side and this is the center so this is what I'm gonna use for my hearth board you can see I've got plenty of white wood there out of one of these to split again okay I've cleaned up the outer side again I want to stay in the white wood and I've picked a good wide spot of that white wood right here so this is gonna be my board and it's about thumb a little over finger thick and this length is good because it gives me a lot of options down the road as long as I can keep this thing dry okay now we have split one side of that log off and we're going to use one of these two to create our spindle okay so I decided the length that I wanted my spindle to be and generally you know something like that is about what I start with it's easier to remove the bulk of the waste material with an axe then go back in and refine it with your knife now as I begin to refine the shape of this spindle I want to keep it straight I don't want that thing to have a hook in or it's gonna wobble when I'm drilling with it so I got to keep it straight the next thing I want to think about is how big do I want this thing to end up and for me in the Eastern woodlands with the material that I generally use which is tulip poplar because I'm pretty shy on cedar out here for tulip poplar I like to have that spindle about the size of my thumb in diameter or just a little bit bigger and again you know about this big okay so here's what I tell my students when they're making a bow drill spindle for the first time I tell them to make that spin to look like the pencil you had when you were in about fourth grade and you've been chewing on the eraser all day long and you're about ready to take it to the pencil sharpener because it was getting dull so you've got a very dull point but a definite point on the top of that spindle that's going to rest in the bearing block and then you've got kind of a chamfered and bull-nosed front end on this thing that looks like it shoot on a racer okay the next thing we're going to work on is we're going to work on our handhold or our bearing block and believe it or not that's the place that causes the most problems in a bow drill set you don't want any friction in that bearing block because you want all the friction down below if you have friction at the top and you start to Waller out that bearing block and it starts to what's called solar out where it's rubbing on the sides of the hole that you've created for your bearing block or the divot it's going to become harder to be able to push that bow back and forth to rotate that spindle the easier that spindle moves the better you're going to be at making a bow drill ember now you can get commercial hand holes like this Pathfinder fire tool or you can make a handle I made this one out of antler this morning really quick and it's just a piece of antler tine it's comfortable in my hand to hold and I just drilled a small divot in it with a large drill bit then I put a drill the hole straight through it right here for a lanyard but that will work just fine as well and you could make this on the fly in the bush if you needed to by carving out out with your knife point nobody worked the same way and you can burn these antler tines off if you find a shed in the woods just by holding a hot coal up to them for a while and then snapping them off I've got video on that on my channel so this is something you can make in the bush this is something you would have to carry in with you for practicing the bow drill but again this is going to make it seem easy compared to what it really is sometimes because a wooden handhold is much more difficult and that's what we're gonna make it right now now I should mention in this video that you could also find a stone that already had an indentation in it or groove in it that you could use for handle I see lots of people doing that and that'll work as well and there's lots of fancy tricks that you can use you know shot glasses and skateboard wheels and bearings and all those kind of things but none of that is truly bushcraft to me if it's not made out of a piece of natural material like antler or wood it's really not truly bushcraft but then again you go all the way back to is your cordage natural material on your bow itself is that really bushcraft I think primitive fire is an important skill to understand not because it's going to save your life but because it teaches you a lot of mechanics and a lot of understanding variability within a process so what I've got here is a piece of hard wood and I'm going to it's pretty damp that's an advantage to me because I'm going to get less burning of that handle and what I'm going to do is this thing is about two and a half inches something like that in diameter I'm going to cut this off to about the width of my hand and then we're going to split it in half okay so I've taken a piece of that wood and cut it off and I've split it just on one side of the heartwood you can see this is the side I would choose I want that heartwood so it's really nice and hard that's a green piece of wood and it's damp so this thing is gonna be great for a handhold again back to that whole thing of you know what is bushcraft well to me anytime you have to craft something in the woods to make something work even if it's just part of the bow drill set maybe you bring in the handhold maybe you brought in cordage but you have to erect the rest of the set from natural material that is bushcrafting
anything else beyond that is primitive wilderness living skills and right now we're talking about bushcraft okay so I've taken that piece and I've chamfered the edges so it's more comfortable in my hand and I've just dug out a little area in the center with my knife point just going in there and cutting the trimming the fibers just like this to cut that hole in there now you don't want to get that too deep because it's going to burn in and generally what I'll do is I'll take this and just kind of twist it in there a few times to kind of marry those up and I'll do the same thing on my fire board here in a little bit you'll see what I'm talking about all right just like that now we're ready to go okay so to the bow part of this so I like to find something that's got a fork in the top that is fairly long green it doesn't matter if it's got a bow in it if it's straight it's fine we're going to clean this up get all the branches and stuff off of it cut it to length and then we'll talk about some more okay
don't overcomplicate this part of the process clean the knots off of it make sure that they're level so you don't get any humps and bumps in there because your spindle will be on the outside of your string anyway so it's not going to rub up against this but you don't want anything rough on there either necessarily I like to have this thing about the length of my outstretched arm with my cupped hand in my armpit that gives me a good length the biggest mistakes I see with bows when it comes to students is too fat or too short you want this thing plenty long because the more stroke you can get out of this thing it's just like a saw the more stroke you get the more revolutions you get to that spindle with a single stroke that's important the other thing is you don't want this thing heavy because you may be going out this for a little while so if you're going at it and this thing is heavy it's gonna wear you out so you want this thing nice and light but nice and sturdy a good green heavy branch will work fine for this okay let's talk about setting up this bow for a minute now you can see I've got a fork on the front of this bow and I like that for reason show you that just a minute it doesn't matter if you're using like Hickory bass cordage like this or if you're using that utility cord you had in your pocket that I showed you yesterday on the we hung our pack a six-foot piece of paracord or plot a piece of bank line into the woods so just take that bank line put a stop knot in one end of it then come up here and put a bowline knot in that thing and it doesn't matter what your loop size is but you can keep the loop size fairly small on this bowline knot it doesn't have to be really big okay something like that will work just great now I'll just tie stop not in the other end of this thing what that allows is allows me to put that loop over the top and run it right back over the top just like this to hold my bowstring now all I need to do is cut a quick notch to tie this cord into and I'm ready to rock and roll it doesn't have to be fancy a saw kerf is enough look at how your string lays on the bow and how you want to be flip it over to both sides I see which side is better the sides got a little bit of a bow in it so what I'm probably going to do is I'm probably going to put my kerf right on the back side here about right here of that V mark that with my thumb put my kerf in there and then tie it off okay the next thing we want to do is we want to make sure that our spindle and our bow all ready to rock and roll so we've got our bow tied up here and now we want to put our spindle in now I'm left-handed but I always approach the string from the bottom with the working end or the end it's going to go in the board up and then turn it down so if I'm right-handed I'm going to come over here go behind the string turn it down and if your strings tight you may have to roll it a little bit to get it in there you kind of want that to be honest with you get a good bite on that thing I know that's gonna go in there so that's no big deal I know we're good to go now that's a good tight string and we're ready to rock and roll with that part so the next thing we need to do is prepare our board for the burning process now this is where a lot of people make a mistake it really matters a lot where you burn this hole and how this knot is both oriented and construct
this board what I tell my students is take the thickness of your spindle and half again and that's where you want to start your burning process if you're too close to the front of this board you're going to end up burning into your notch and you're going to lose a lot of friction against the board because you're going to have that knotch open area where you're not getting any friction of the spindle against material to create an ember so you want to take this thing and lay it on the board and go half way back one roll so about right there is where I want to create the spot that I'm gonna burn in so when you're cutting that initial divot in there get that thing on a flat surface choke up on your knife and just dig yourself a spot in there don't go too deep it's better if you are scraping across the top to create that divot and moving the workpiece as you go just like this and severing those fibers as you go around it doesn't have to be real deep trust me on that you're dealing with soft wood here now what you can do is you can come up here and you can take this and just kind of work it in just like I did with the handhold they kind of marry that up and see where you're at if you don't think you're deep enough at that point then you can go back and do it again okay and next thing we want to do is we want to before we cut any notches in this board we want to ensure that the sets going to work and that's called the burnin process what that does is that tells us exactly where the spindles gonna ride so that we can create our notch in relation to that and it also gives us an indication of whether this piece of wood is going to work well for us before we put any more work into it like creating a notch so just lay it on the ground and get your materials together we've got our spindle in our boat and we have our handled we'll go ahead and load our spindle I'm gonna load this thing on the left side because I'm used to it I've already showed you how to do from the right side you're better off if that thing is lower on the spindle when you load it up then higher and when you are rowing this thing or Boeing action is going on here you've got to keep this bow level if you turn it up it's going to ride up the spindle if you let it droop down it's going to write down the spindle so that part is very important the next thing that's important is okay here's a good point I want to talk to you about real quick I'm getting ready put my foot on this board
my foots probably got mud moisture and everything else on it I could do myself a favor and put another piece of wood on there and that would be a smart thing to do if I were planning on using this kit very long now I'm going to come in here and hold everything together and I'm gonna lock the crook of my wrist into my shin and I'm going to move my back leg out of the way and now what I want to do is I just want to slowly I don't want to get in a hurry here I want to put downward pressure on it get the center of my body the center of gravity of my body over the top of the spindle so that I don't have to use my arm to put pressure on the spindle I'm really using my leg by leaning forward my legs pushing in on that spindle pushing down and then I just want to gently marry the set and this is my chance really to kind of see what's going on to make sure that I'm creating what I need to create for material make sure it's burning in good make sure my colors right make sure my handhold is good once I get that thing black I can stop and now I'm going to inspect the pieces and parts of my set the first thing I want to look at is am i shouldering out here and I can feel a little bit of resistance here long enough to know that so that tells me this is already shouldering out in here this needs to have a little bit steeper point on it the problem with that is the steeper this point is the easier it is to crush it away so I probably would opt to open this up instead okay the next thing we want to look at is our knotch and this is really really important what we want to do first of all is we want the into that notch to basically just touch or apex right there and we want to go out from that like this okay now a couple things depending on the material that you're using this notch may need to be bigger or smaller if you're using a fibrous material like tulip poplar it may need to be a little bit wider to allow more oxygen into the material if you're using something that's very dry and very fine dust then you can't get away with the thinner notch all right so what we're gonna first do is we're gonna cut this notch basically just like this with a saw into our board and remove it and we could use our knife for that or our saw either one I find a saw is pretty clean and quick and dirty okay I'm going to show you a little tip or trick real fast here while I'm cutting this notch you can see that I've cut the notch with a saw I've kind of left the line there for you to see but what I did was I back cut it on the other side so in other words I made my straight cut and then I taught it a saw a little bit and cut back into it a little further on the back side so the notch is actually a little deeper on the back side than it is on the front side now you can't pop that notch out of there with your saw or you can pop it out of there with your knife either way just pop it straight out now you can kind of see how that notch is a little deeper on the back and it is the front and now you just want to kind of clean that out make sure you got a good clean surface there and I like to cut just a little bit of a recess right there where it marries up to my burn in just to give that coal a good place to spill into and you can see what I've done is I've restricted yet I've opened up the notch by doing that back cut and you can see that right here how there's a little bit of a taper in that notch I hope you can see on the camera next thing I'm going to do is I'm going to come to the bottom of the board and I'm gonna cut a little bit of a chamfer right in the base of that notch and what that's gonna allow is it's going to allow when that board is on the ground flat it's going to allow a little bit of oxygen flow underneath that notch to the material and I find that when you're talking about materials like tulip poplar that extra aeration underneath there makes a big difference because you're talking about a thick fiber material so the construction of this knotch depending on the material using can be very very critical okay the next critical step is the creation of our bird nest and it needs to be made up of coarse medium and fine material what we've got here is a combination of poplar bark and Aspen bark okay and we're going to take this bark and we're just going to begin to shred it and process it down and I'm just going to take the whole bundle and start to spread it out I've got some key pieces like this one that have really fine fibers in them I'm going to set those aside because this right here is going to be my course and medium material looks like there might be a little bit of grapevine bark in there that's not gonna hurt anything with this operation here the bird nest portion of this it's really key that you process this stuff up as good as you can that's another big mistake I see with people they work really hard to get that Ember and then they can't do anything with it because their material is just trash and you want to kind of fold that into a bird nest okay you're trying to make a bird nest out of this thing if that thing don't look like something a bird lay an egg in it ain't good enough collect all them fine material kind of save that to the side for a minute get that thing turned in turned over rolled up so you got a good deep nest there and it's nice and thick I think should be the size of a softball okay now we're gonna take some of this material here and get as much bark off of as we can and get it processed down these fine fibers I want some of these I also want some of the finest stuff that I can on the ground here in this nest so I'm gonna put that stuff in there that really fine stuff and I'm gonna set some of this aside for later because this is really really highly combustible stuff here and then I'm gonna come in here and get the finest stuff that was on the ground and sprinkle that in the center of that nest just like that okay we're going to set that aside that's how you construct a proper bird nest okay this is where the rubber meets the road now we're going to take something and this is just a sliver of our original material and we're gonna put it underneath our board for what we call a welcome mat a place for that coal to collect and form what I want to tell you before I start doing this is that the mistake I see a lot of people make is they go too fast too fast you don't need to go a hundred miles an hour to get this to happen what you need to do is remove material from this board in the spindle to accumulate in the knotch because that is your fuel for your fire you'll then add heat to ignite that material without the material in the knotch the speed creating heat makes no difference whatsoever
you've got to create friction first and heat second okay I went ahead and move this inside underneath this overhang a little further because of the wind outside I wanted you to be able to see this without the wind blowing everything around at the same time when you're doing it so again you know we've got a welcome mat underneath it so we've put a piece of bark underneath here and that's our welcome mat that's just a place to catch our ember so that it does not sit on the ground and absorb moisture it also gives us a way to transfer the Ember once it's coagulated into a bird's nest now we're going to use exactly the same form that we use the last time around and we're going to start off slow because really all we want to do is build up material in this not through friction it doesn't matter how much speed we have to create heat until we have filled that knot with dust because that's the material for our fire protect it from the wind a little bit but you want the wind to get to that Ember
at this point you got plenty of time let's move this up still see our end we're here now we really just want to let that thing matter of fact I'm gonna get this camera down here I really just want to let that thing build up until we see it turn red on the top so we got plenty of time to catch our breath and all that stuff while that's happening once we see that things start to glow then we can think about transferring that thing into our bird nest the key is get your bird nest as close to the embers you can get it now you can see it's starting to glow right there all right so now I'm gonna move this back up here and we're going to gently pick this welcome out up and gently tap that ember into our bird nest and then let that thing build up a little better again I'm reposition okay we want to fold our nest just a little bit and gently gently blow remember that heat rises so blowing from underneath up is always going to be better if you've got a big ember you don't have to be in a hurry there you go
About the Author
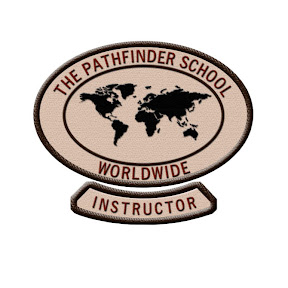
wildernessoutfitters
From the lore of bushcraft to all things related to self-sustainability, the Pathfinder vision is to pass on the knowledge of outdoor self-reliance. Providing basic to advanced self-reliance training and survival gear, our goal is to offer both practical knowledge and survival gear that will stand the test of time. From emergency preparedness to sustainability, the Pathfinder way is to share and educate.
Here you can explore the world of survival knives, survival kits and simple tips on outdoor self-reliance. We are always learning and enjoy passing on the knowledge we acquire.
There is no substitute for having a plan in the event of the unexpected.
More articles from this author
- Black Drawing Salve
- Pace Counting and Dead Reckoning
- Bullet Proof Bushcraft on a Budget Long Guns
- The Witchery of Archery Part 3 Arrows and Arrow Flight
- Sling Bow Final Modification How To
- Journal of the Yurt 29 Q&A
- African Bird Trap
- Journal of the Yurt 37 Stock and Trade
- A Common Man Sustainability Cross Bow
- Modular Packing Discussion
- Rendering Birch Oil, As taught at the PF Pioneer Class by Joe Kellam
- Modern Trapping Series Part 41 Raccoon caught in a False Drain Set.wmv
- Shooting the Recurve Bow (Beginners) with Iris Canterbury.wmv
- Journal of the Yurt 2
- Journal of the Yurt 7
- NINJA SHELTER
- Spring pole Bowdrill Ember
- Cooking Tips and Quick Treats (Garlic Rice and Smoked Sausage)
- 5 Navigation Techniques Every Woodsman Should Know
- Building a Discount Bushcraft Kit Part 5 (Wool Blankets)
- Journal of the Yurt 38 A day in the Life
- Trail Tarp Set up Options Part 1
- Cast Iron Cooking Part 2 Pork Mash Cassarole
- Creating a Fire with Aspen Punk wood and the Sun
- Modern Trapping Series Part 44 Skinning a Mink
- Shoes a Simple Improvised Pattern
- Pathfinder Advanced Class Florida Everglades
- Blacksmithing Part 14 Making Nails
- Bow Saws, a Common Man Bush Tool
- Bow Fishing Equipment Explained
- Kid Testing of the Lightning Strike Fire System
- The Osage Bow Part 6 (Draw Wt and Shooting)
- Modern Camp Set up
- Utilizing Resources Tallow Making Lye Soap
- Apache Foot Trap
- H&R 12 GA Buttstock Mods
- The Quickie Poachers Camp.wmv
- Blacksmithing Part 7 Making Cooking Irons
- Tablet Weaving
- 21st Century Longhunter Processing Tinder Fungus for Use
- Neolithic and Ancient Roman Fire Methods
- Eastern Woodland Trees and their Uses 1
- Using a Compass to take a Visual Bearing
- Journal of the Yurt 24
- Journal of the Yurt 36 12GA R&D
- Kit Mentality the Basics
- Blacksmithing Part 11 Forging a Knife Step 1.wmv
- Beginners Knife Safety Part 1
- Commercial: Dave Canterbury "Makes fire with his beard"
- Modern Trapping Series Part 23 Skinning the Catch
- Starting your net
- Wood Craft on a Budget Part 6 Cookware 2
- Jam Knots 3 that do it all
- Slingshot Forging
- Pathfinder Product Review 11 Flint Knapping Tools
- On the Waters Edge Part 4 Sling Spear
- Pathfinder Product Review #3 The Emergency Shelter Kit
- Pathfinder Product Review #5 The Nessmuk Hand Axe
- Throwing a Knife
- Packable Draw Knife and a Simple Vise for the Woodland Projects
- Bushcraft Kit Shot Show Intro
- Shooting Vanes from a Traditional Bow
- Journal of the Yurt 1
- Testing a Common Man's Survival Bow.wmv
- Diary of the Tipi 4 Primitive Archery Repair Kit.wmv
- ROKON Series Intro
- Cornish Hen Cassarole in an Aluminum Dutch Oven
- Super Shelter Modified for the Eastern Woodlands Part 1
- Improvised Zip Lock Compass.wmv
- 21st Century Longhunter The Versatile #110 Conibear
- Journal of the Yurt 31 Folders and MT's
- Condor Greenland Axe Pathfinder Product Review #12
- Packing for a Trip the 3 C's Concept
- How to get your pattern for a wool blanket shirt
- Brain Tanning Hair On Part 1
- SlingBow DVD
- Fleshing hides: The easy way
- Butcher Knives a Frontier Standard.wmv
- Reviewing a Survival Shotgun Set up.wmv
- Long Guns, Canoe Guns&Testing the Wax Slug 12 GA Load
- Stronghold Haywire Klamper Projects
- Asian Monitor Trap
- NO FAK First Aid Kit
- Journal of the Yurt 6
- Walnut Blueing an H&R 12GA
- Modern Trapping Part 4 Foot Hold Traps
- Mora Camping Axe "Dont save it for the wimpy wood!"
- Quick Run Down of the Final 5 C's of the 10 PC Kit
- 1751 Belt Ax Kit Project Part 2
- Fire Tube
- Journal of the Yurt 28 Spices
- Journal of the Yurt 26 My Shooting Bag
- Utilizing Resources, Glass Arrow Heads
- Iris Intro1.wmv
- PF Cook System for 2017
- Primal Gear Unlimited Compact Folding Survival Bow
- Corn Meal Mush
- Journal of the Yurt 9
- Emergency Fire-Foul Weather
- Boot Care and Boot discussion
- Pathfinder Pocket Hunting System Promo
- Auger Adapter DIY
- Making a Scrap Yard Folding Knife Part 1
- Bug Dope
- Tools and Honing Discussion
- Pine Sap Accelerant
- Journal of the Yurt 5
- On The Waters Edge Part 8 Fileting a Fish
- American Mod to the Asian Bird Trap Snare
- Modern Trapping Series Part 26 Prepping the hide for Tanning
- Modifying Brass Shotgun Shells to accept the 209 Primer.wmv
- Survival Bows (Shaping and Floor Tillering the Stave)
- Woodcrafters Bench Part 4 Spoon Mule Attachment
- Pathfinder School Self Reliance Projects Update 2
- Char Cloth and Ignition Sources
- Wool Blankets Winter Camping Part 2
- Making Woodland Furniture The Dove Tail Joint Lash
- Fire School Part 9 Bowdrill Ember from Horsehoof Fungus
- American Yurt at the Pathfinder School Intro
- Journal of the Yurt 3 Making Hard Tack
- Cast Iron Cooking Part 1 Spicey Rice Dish
- Pathfinder Nessmuk Trail Tarp by Duluth Pack Co
- Take Down Bucksaw Project Wood Craft on a Budget Part 19
- 5 Min Shelter Option Double Wedge
- Swing Arm Cook System from Natural Materials
- Stump Anvil Improvements The Clave
- Throwing the Tomahawk
- Making Corn Flour Cereal.wmv
- Diary of the Tipi 8 Making Gourd Containers Part 1
- Starting Fire with Steel Wool and Ferro Rod
- NEW Gen 2 Small Bushpot
- Exploring the Whelen Lean Part 2
- Converting Your Percussion Cap to 209 SG Primer Ignition (Mag Spark)
- Over Night Scout
- Pathfinder Cribs The Pathfinder Yurt
- Survivability vs Sustainability.wmv
- Self Feeding Fire Part 1 Basic Bushcraft
- Simple Machines 3 Rope Spinner
- Bullet Proof Bushcraft on a Budget Cover
- Wood Craft on a Budget Part 10 Refurbishing Old Tools1
- Survival Basic Series DVD Part 5
- Pathfinder Product Review #14 New Mora Knives
- Addressing Snake Bites
- Top 5 Medicinal and Useful Plants of the Eastern Woodlands Part 1.wmv
- Poplar Dough Bowl Part 1
- Simple Camping Plow Points Part 1
- Clothing for the Cold
- Frontier Fire Methods 2.wmv
- Fishing Kit-Improvments Testing
- Modern Trapping Part 5 Intro to Snares and Snaring
- Equipment List Discussion for Pathfinder Basics
- Processing Small Game Pheasant
- Evolution of Survival
- Black Smithing Part 1 Making a quick Fire Striker from a File
- Modern Trapping Series Part 33 Using PVC in Sets
- Journal of the Yurt 8
- Journal of the Yurt 4
- Introducing the Pathfinder Scout Hawk
- Mini Inferno NEW PRODUCT
- The Common Man's Last Shot- Pocket Pistol
- Scout about and Bacon out
- Simple Bucket Pack Modification
- Navigation by Terrain Feature Association Part 1
- A Quick Bait holder for Catfishing
- Building Traps without Tools
- Journal of the Yurt 27 Securing More Meat
- The Witchery of Archery Remake Part 1 The Two Tracks Long Walker
- Pocket Hunter A Comprehensive Look at Design and Use
- Practicing Fire Methods 1
- Cabin Fever Part 20 Preserving Game meat in Winter
- Cast iron Cooking Part 3 Deep Fried Bass Filets
- Journal of the Yurt 50 Forging a Cookset.wmv
- Journal of the Yurt 23
- Tarp Setups and Research for System Development
- 5x5 Bushfit Kit
- A Review of 3 Pocket Tools
- Bushcraft Tools Fire Piston Test
- Sunfish Lunch'en
- Knapping a Quick Stone Point from a Flake.wmv
- PVC Bait stick Trap
- Bullet Proof Bushcraft on a Budget Containers
- Cooking Squirrel and Rice
- The Spider Shelter Part 3 Finishing up and heating it up!
- Fire School Part 14 Rub Cloth
- Journal of the Yurt 20
- Journal of the Yurt 18
- Journal of the Yurt 41 Pack Goat
- Materia Medica Yarrow 3
- Building a Discount Bushcraft Kit Part 4 (Take Down BuckSaw for Ten Dollars)
- 5 Tools and Functions to manipulate Wood
- Brain Tanning Hair On Part 3
- Grand Opening Invite
- Common Man Self Reliance Bow #2
- Cabin Fever Part 29 ATV Scouting and my Kit 1
- 21st Century Longhunter Mentality and the 5C's
- NEW Council Tool Woodcraft Pack Axe
- 2 Dollar Knife and Sheath Project Part 1
- Reproducing an Antique Draw Shave Part 1
- Basic Multi Use Knots
- New Sling Bow
- Quick Fishing Kit from Common Materials
- Asian Trail Spring Trap
- Natural Cordage Part 2 The Process of Reverse Wrap 2 Ply Cordage
- Ignition Sources, My Belt Kit
- Bushcraft Kitchen Part 1
- Dressing for Cold Weather.wmv
- 5 Minutes to Better Bushcraft Building a Friction Fire Ember
- Torture Test of a Savotta Pack
- Wisdom of the Wall Tent Part 4 Junk on the Bunk
- Full Circle
- Carving a Noggen
- Canvas Ship Hammocks and Weaving a Clew
- Traditional Japanese Water Stone Sharpening
- 5 Minutes to Better Bushcraft Dakota Fire Hole
- Blacksmithing Part 39 Making a Portable Pit Forge
- Dream Hammock System
- Starting Fire with a Compass K&R Alpine
- 5 Wooden Tools
- New Jon Pack Woodsman’s Bed Sleeve
- 5 Minutes to Better Bushcraft proofing and Reproofing
- Mushroom and Plant walk in Sweden
- Mora Adventure 2018 Short clip
- 5 Min Fire and Shelter Conversion.wmv
- Trap Comparison and Thought Process, Modern Trapping Series Part 43
- Simple Fencing
- Rendering and using Raccoon Fat
- Viking research
- Hickory Resources
- Bushpot Chicken and Dumplings
- Woodcrafters Bench Part 2
- 21st Century Longhunter The Oil Cloth Watch Coat
- Game Hooks
- Bill Hawk
- Pathfinder Product Review The JW Trekker
- Basic Camp Overnighter Part 3
- Next Fire Mentality
- 50 Dollar Tool Kit for Green Woodworking
- Pathfinder Product Review #6 The Duluth Pack PF Haversack.wmv
- Steam Bending Wood
- Water Filter Comparison
- Sling Bow (Bow Fishing Mod How To)
- Survival Bow Making(Making a Bow String)
- Making the Packable Draw Knife
- Making A Common Man's Broadhead
- Building a Discount Bushcraft Kit Part 7 (The Blanket Pack)
- Exploring the Whelen Lean
- Blacksmithing on a Budget
- Building a Discount Bushcraft Kit Part 6 (Cheap Small Game Snares)
- Materia Medica INFUSIONS The Woodsman's Expectorant 22
- Fire School Part 8 No Container Char
- Norlund Axes
- Using Flex Seal on a Canvas Pack
- Pathfinder Product review #4 The Pathfinder Trade Knife.wmv
- Knives and Processing Wood
- Axes and Hatchets Wood Craft on a budget Part 15
- Opinel Safety Mod and Penny Knives
- The M44 Mosin Nagant, A Common Man Rifle
- Simple Box Traps Live Rabbit Box
- Grass Thatching
- Frontier Fire Seminar from the Camping and Woodcraft Class
- Rocky Woodland Forge's Woodcraft Tool Kit
- Stack Pack by Short Lane Arms
- Restoring A Scrap Yard Wood Stove
- Diary of the Tipi 10 I love Fire! my EDC.wmv
- PFODJ Ep4 18th Century Woodsman Hunters Camp
- Camp Cookery Baked Rabbit
- Survival Pro Tips 1 Making Fire with an Empty Bic
- Simple Box Traps Mink Box
- Fire School Part 2 Bow Drill Lessons
- Meat Processing Tools
- Fire School Part 7 Strikers, Scapers, and Smooth Strokers
- Tools and Wood Processing
- Medicinal Trees of the Eastern Woodlands 1.wmv
- Hush Puppies on the trail
- Blacksmithing Part 17 Scrap Yard Pick'en
- Hammock Chat
- Knife Making , Material Reduction Knife Start to Finish Part 1
- Belt Pouch EDC
- Useful and Medicinal Trees of the Eastern Woodlands 3
- Using the H&R 12GA for a Muzzeloader
- Ultimate Survival Bows
- Journal of the Yurt 11 Hygiene
- Journal of the Yurt 10 Visit with Jeremy Janey PF School Intructor
- On the Waters Edge 13 Day 2 Mohawk Canoe
- Hygiene from Fire
- Wisdom from the Wall Tent Part 1
- Making a Common Man Limb Quiver for Hunting
- Coyote Consuming the Harvest
- Knife Care in the Field
- Hobo Stew and Corn Bread
- Bushpot Jambalaya and Hushpuppies
- Useful and Medicinal Trees of the Eastern Woodlands 4
- Basic Camp Overnighter Part 1
- Axe Care Made Simple
- Bulletproof Bushcraft on a Budget Part 1
- Snares The Ugly Truth Modern Trapping Part 57
- Kit mentality Useage vs Investment
- Blacksmithing Part 36 The Wind Tunnel Forge
- New Primitive Technologies Discussion
- Blacksmithing Part 13 Forging a Knife Step 3 Heat Treat and Testing
- Fire Lay The Proper Construction and Ignition after a Night of Rain
- Fire Arms Combination for Long Term Sustainability
- Modern Trapping Part 29 Foothold Pocket Set
- Basic Knife Handling and Bush Craft Notches Part 1
- Blacksmithing Part 18 Making a Brake Drum Forge
- Bucking with a HB Cruiser Ax Wood Craft on a Budget Part 16
- Journal of the Yurt 12
- Reloading 12GA with (Pyrodex) Black Powder in the Field
- Skinning a Raccoon with Rope,Modern Trapping Part 32
- The Witchery of Archery Part 2 The Basics
- Honeysuckle resources and a quick update
- Survival Bows (Collecting the Stave, Improvised Draw Knife)
- Skinning a squirrel for a usable hide
- Blacksmithing Part 12 Forging a Knife Step 2 Material Reduction
- Evolution of the 10 C's Part 1
- Shelter Basic Tarp Setups 1
- Fire The Basic Class Presentation
- Mora Garberg Full Tang Discussion and Review
- NEW 2 1 Ltr Bushpot and 64 Oz Bottle
- Shelter Basic Tarp Setups and an E Fire 2
- Mora Dangler made simple
- Simple Machine Woodland Hoist
- Coyote It's whats for Lunch
- Shelter Basic Tarp Setups 3
- A Woodsmans Apothocary
- Wooden Pulleys and Lifting
- Deer Heart and Pepper Gravy Camp Cooking
- Simple Woodcraft Aids
- Overnight Pack Out
- Fire School Part 1 Bow Drill Lessons
- Collapsible Cast Iron Skillet DIY
- Quick Upload Extracting Pine Tar from Fat Wood
- Blacksmithing Part 15 Making tools for Spoons and Ladles
- Forging and making a Primitive Adze
- Trapping Season Prep and Primer Discussion
- Top 10 Non Firearm Meat Gathering Tools
- Haversack Kit
- Pathfinder Advanced Class 1_7_2010 MA, USA.wmv
- Squirrel Hunt with a Flintlock
- Best Medium Game Snare Modified figure 4 Trigger
- Council Tool Hudson Bay Camp Axe
- Gig Discussion and Hunt with Weapon Vision Spear Cam
- 2 Dollar Knife and Sheath Project Part 2
- Go Ruck Rucker Review and Kit layout
- Bushcraft Breakfast Bannock
- On the Waters Edge Part 1 Compact Fishing Rods and Systems
- Toggle Trigger Fishing Variation
- Swiss Army Knife easy Ember , Fire Tips and Tricks
- Roycroft Pack Frame Part 3 Using Shelter Components
- Blacksmithing Part 4 Rounding and Drawing steel to make a Trap Stake
- Fire School Part 13 Ferro Rod Tips
- Tension Bending Pack Boards
- 12GA Shell Bag Contents and Discussion
- Bushpot Convection Oven
- Stretcher Bed Setup
- Pathfinder Folding Skillet
- Making Sweet Corn Bread Drop Biscuits
- Diary of the Tipi 2 Making Hide Glue.wmv
- Otzi s Knife Sheath
- Pathfinder Basic Survival Class Video Diary
- A Common Man's Grease Lamp
- Canterbury Camp Kitchen
- Rokon Winter Packout
- Blacksmith a Squirrel Cooker explained Part 47
- Leather Knife Scales
- M6 Scout Update Review
- The Osage Bow Part 1
- Basic Carving Kit
- Snow Shoes JMHO
- Simplicity
- Final Product Modified Kephart Bedroll by Duluth Pack
- Swedish Lap Vise
- Forging a Custom Carving Axe with Liam Hoffman Part 1
- Toggles The Woodsmans Friend
- Tarp Setups the Foresters Tent and the 4 W's
- Making a Blade Bowl Adze
- The osage Bow Part 4
- Taking a Bearing from your Map made easy
- Journal of the Yurt 43 Stock and Trade Part 2
- Survival JMHO
- Simple Camping Improved Pot Crane System
- Batoning Wood with your Knife
- Improving the Wax Slug Load for 12 GA and Black Powder Equivelant
- Modern Trapping Part 7 Bedding Foot Hold Traps
- Wisdom of the Wall Tent Part 3 Camp Tool Box
- Useful and Medicinal Trees of the Eastern Woodlands 5
- Pine Crate Tool Chest
- Pathfinder School Basic Class Equipment List Rundown
- Diary of the Tipi 11 Care for a Smoothbore Flintlock.wmv
- Baking with a Plank and a Bushpot
- Wood Craft on a Budget Part 3 Sheath Knives Continued
- Building a Discount Bushcraft Kit Part 3 (Food)
- Triple Barrel Shotgun PF Edition Intro
- Maul a good Learning Project
- Meat Preservation Concerns and Setting Snares
- PFODJ Ep 11 Wet Weather Fire Segment
- The Small Common Man Trapping Kit
- Useful and Medicinal Trees of the Eastern Woodlands 2
- Simple Camping Connection Knots 3
- Pathfinder Outdoor Journal Ep1 FULL HD Episode
- Quick Review of the ILBE USMC Assault Pack and Sealine Insert Bag
- Simple Blade Grinding Jig
- Diary of the Tipi 12 Working with Natural Dyes Part 1.wmv
- PF SS Kettle
- Jeff White Bush Knife and a Wet wood Fire
- My Back Yard
- Knives JMHO
- Iris Intro Video Part 2.wmv
- Thanks for Play'en, Bobcat in an MB 450 Released
- Kit Mentality Updates
- Bullet Proof Bushcraft on a Budget PVC Pack Frame
- The Osage Bow Part 5
- The Mocotaugan
- Pathfinder Knife Shop Introduction
- Deadliest Small Game Primitive Trap
- Saami Repair Kit
- Building a Discount Bushcraft Kit
- Stone and Bone (Utilizing Resources) Part 1
- No Map No Problem Part 2
- Arrow Making for the Common Man
- The Wish Bone Trigger Snare New
- Making a quick Spring Lathe
- Using the Slingshot to Hunt Bigger Game
- Bark Basket Part 1
- Scout Camp Common Man Black Powder Setup
- Collecting Back Sinew and Some Meat from a Roadkilled Deer
- Dakota Fire Hole Proper Construction and Use
- Artifact Quality Leather Work
- Bucket Making White Coopering
- PFODJ Ep 5 Axe Tomahawk Segment
- Reverse Figure 4 Dead fall Trigger
- Fire and Bushpots
- Shooting Shot from a 50 Cal BP Rifle
- Tarp Setups Modifed Plow Point
- 50 Cal Blue Ridge Mountain Flint Lock
- Remington Shotgun Model 1889 Double Barrel
- Shrink Pot 1
- Reflector Oven Bread
- Preping the Sling Bow for a Big Game Hunt
- Modern Trapping Coon in Beaver set
- Brimstone Matches and Next Fire Mentality
- No Map No Problem Part 3 Height and Distance
- Saw Maintenance 2 Wood Craft on a Budget Part 14
- SS Canteen Available NOW!~
- Identifiying Flint Chert and other Sparking Rocks
- Trap Sets The Step Down Set Modern Trapping Series Part 48
- Axe Selection and Use
- The Osage Bow Part 2
- Tomahawk from a Rasp Blacksmithing Part 46
- Making Pemmican
- Moonshine Why Carry
- Trailblazer Deliverables Basic Compass Use
- Making the Flemish Bow String in the Bush Part 2
- Simple Camping Hammock use with Wool Blankets
- Forging a Hook Knife
- Finishing a New Old Stock Mora 311
- Survival Basic Series DVD Part 1
- Sharpening an Axe with a Hardware Store Grind
- Putting a Handle on a Mora Blade Blank
- Simple Machine DIY Spring Hammer
- Forging a Tomahawk from a Rasp
- Feathersticks or Shavings
- 21st Century Longhunter Series Combustion
- Fire School Part 15 Pump Drill Fire,Learning the process
- Seneca Pack Frame
- Ever thought about this? Fire Tricks
- Sustainability Long Term,Modern Trapping Series Part 42
- Blacksmithing Part 2 The Folding Small Game Gambrel
- Double Bit Axes Wood Craft on a Budget Part 17
- Sleeping Gear JMHO
- Knapping Arrowheads From Glass Part 1
- Mora Bushcraft Pathfinder
- Making a Cook Tripod with a Chain
- One Match Fire for BSA Bushcraft
- Rope Bed Construction
- The Spider Shelter Part 4, Simple Improvments
- Quick and Easy Tensioner Knot for your Tarp Lines.wmv
- 10 Simple Knife Projects Part 1
- Lighting a Candle with Flint and Steel
- Winter Pack Out
- Utilizing Resources (Making Venison Jerky) Part 2
- Natural Cordage Part 1 Harvesting and Processing Materials
- Asian Bird Trap Laos
- Vines and Withies
- Woodman's Pal
- Five Tool Rule
- Prefered Clothing and Layering for the Woods
- Simple Shadow Navigation Part 1
- Brain Tanning Hair On Part 2
- R&D of the Kephart Bedroll by Dave Canterbury and Duluth Pack
- Light Weight Scouting Pack Set up
- Trapline Diary Part 1 Coon Cuffs
- Survival Basic Series DVD Part 2
- Pathfinder Basics Estimating Distance and Pace Count Lecture
- Super Shelter Modified for the Eastern Woodlands Part 2
- FULL TANG MORA Bushcraft Knife
- Beginners Knife Safety Part 2
- Survival Bows (The Tillering Process)
- Blacksmithing Part 6 Common Man Tools and lighting the Forge
- Building a Discount Bushcraft Kit Part 2
- Sloyd Project 1 Fid
- On the Waters Edge, Trekken and Fishen
- Traditional Cold weather Hammocking
- Knife Making, Material Reduction Knife Start to Finish Part 3
- Trapline Journal Coyote in MB450
- Winterizing the Hammock for the Common Man
- Samick Sage Recurve 8pt Buck Kill
- Large Bushpot Intro
- Bucksaw Modifications
- Fatwood Collecting Processing Igniting
- Aussie Wool Blanket
- Assembling a Custom Classic in the Mora Factory
- Traditional Camp Pack weight
- PFODJ Ep 2
- Hook Knife Part 1
- Making a Bushcraft Knife Part 4
- 1908 A&F Cook Grate
- Nordic Pocket Saw
- Making a Bushcraft Knife Part 1
- PFODJ Ep 5 Moved from the Pay Channel
- PFODJ Progression of Meat Source Gathering
- Experiments in Viking Navigation Viking Sun Stone
- Turkey Tail Materia Medica
- Hook Knife Part 2
- Making a Bushcraft Knife Part 3
- Making a Bushcraft Knife Part 2
- Double on Coons
- The Woodsmans Pantry Plus and the Woodland Chef Cook Kit
- Cooking Bannock in the Bush Pot with a Pack Grill Rack
- Fence Line Snares for Coyote
- Forged Scissors Part 2
- Forged Scissors Part 1
- Pathfinder Scout Hammock
- Trappers Cabin Season 2 Part 5 Raccoon Meatloaf
- Trappers Cabin Season 2 Part 2 Firearms
- Trappers Cabin Season 2 Part 7 Fleshing Hides
- WInter Clothing Discussion
- Trappers Cabin Season 2 Part 4 Tail Stripping
- Hammock Chair Hunting Seat
- Trappers Cabin Season 2 Part 1
- Trappers Cabin Season 2 Part 6 Single Shot Maintenance
- Trappers Cabin Season 2 Part 8 Pocket Sets
- Making a Holiday Wreath
- Trappers Cabin Season 2 Part 9 Making Kvass
- Trappers Cabin Season 2 Part 3 Trash Panda
- 110 For Mink
- Trappers Cabin Season 2 Part 13 Wood Stoves
- Morakniv Carbon Steel Garberg
- Trappers Cabin Season 2 Part 14 Releasing a Domestic Animal
- Z Drag with wooden Pulleys
- Trappers Cabin Season 2 Part 12 Log Crossing Set
- Trappers Cabin Season 2 Part 11 Chasing Mink
- Exotac Products and Titan Lighter tips
- Trappers Cabin Season 2 Part 10 Mapping the Creek Bed
- Trappers Cabin Season 2 Part 15
- Trappers Cabin Season 2 Part 16 Last day for a few
- Trappers Cabin Season 2 Part 18 Buck Mink
- Trappers Cabin Season 2 Part 17 Hidden Woodsman Pack
- Bushcrafting a Tarp Clip
- DD Tents
- Neck Knife to Carry or Not to Carry
- Blanket Pin Tripod
- Hibiscus Cordage
- The Versatile Marline Spike Hitch
- Hammock Chair Terrapin Outfitters
- Sticky Rice
- Udemy Intro Video
- Conserving the Bic in an emergency
- LL Bean Continental Ruck Sack
- Navigation The X Box Exercise
- Cave Man Conibear Updated
- Limb line Hook Set Device from natural materials
- Solar Embers without Char or Fungus
- Packing up the raised Bed Camp
- Raised Bed Emergency Shelter
- Basket Trap for Crayfish
- Making a Sun Compass
- Ottomani Sun Compass
- Dutchwaregear Chameleon Hammock and Xeon Tarp
- Tulip Poplar Knife Sheath
- Shadow Board Direction Finding
- Dirty by design
- Orienting a Map without a Compass
- Mushroom Foraging Part 2
- 5 Minutes to Better Bushcraft Pot Crane
- Paracord Hammock
- 5 Minutes to Better Bushcraft Quickly Deployable Ridgeline
- 5 Minutes to Better Bushcraft Hanging Camp Gear
- Tighten a Shear Lash Easily
- 5 Minutes to Better Bushcraft Tripod
- 5 Minutes to Better Bushcraft 90 Degree Spine
- Mushroom Foraging
- Broiling Fish with Grill Racks and the SRO Monthly Special
- Exerpt on Basket Weaving at the Bushcraft 101 Class
- 5 Minutes to Better Bushcraft Double Prusik Tensioning System
- Week Long Training Loadout
- Lunch and the Base Camp Cookset
- 5 Minutes to Better Bushcraft 5 Navigational Aids
- 5 Minutes to Better Bushcraft The Angular Advantage
- Last Shadow First Shadow Method
- 5 Minutes to Better Bushcraft Improved Fire Starting
- 5 Minutes to Better Bushcraft Pot Hanger
- Tulip Poplar The Best Eastern Woodland Bushcraft Resource
- 5 Minutes to Better Bushcraft Bark Candle Lantern
- Woodsman's Gear of the 20th Century Part 6
- 5 Minutes to Better Bushcraft The JB Figure 4 Variant
- Mushroom Foraging Part 3
- Woodsman's Gear of the 20th Century Part 3
- 5 Minutes to better Bushcraft other uses for Puffball Mushroom
- Woodsman's Gear of the 20th Century Part 7
- Woodsman's Gear of the 20th Century Part 5
- Fried Puff Ball Mushrooms
- Woodsman's Gear of the 20th Century Part 4
- Using a Strop to Clean, Sharpen, and Hone your Blades
- Woodsman's Gear of the 20th Century Part 1
- Best Survival Deadfall Trigger PDF4
- Woodsman's Gear of the 20th Century Part 2
- Woodsman's Gear of the 20th Century Part 9
- Woodsman's Gear of the 20th Century Part 8
- Woodsmans Gear of the 20th Century Part 10
- Woodsmans Gear of the 20th Century Part 11
- Blood Trailing a Deer
- M6 Takedown Rifle Comparison to the Springfield Scout
- Safe Release of Non Target Species
- French Press Testing and Protyping
- Simple Camp and a Test of the Wildward Lavu
- Pocket Stove Comparison