Forged Scissors Part 1
Description
http://www.selfrelianceoutfitters.com
http://astore.amazon.com/davecante-20
The Pathfinder School,Bush Craft ,Survival skills, Historical Lore, Primitive Skills, Archery, Hunting, Trapping, Fishing, Navigation, Knives, Axes, Fire, Water, Shelter, Search and Rescue
Tags: Bushcraft,Survival,David Canterbury,Dave Canterbury,Pathfinder,The Pathfinder School,Archery,Hunting,Fishing,Camping,Primitive Skills,Fire,Water,Shelter,Navigation,First Aid,Search and Rescue,Signaling,Prepper,Preparedness,Self Reliance,Survivability,The 10 C's,Knives,Axes,Saws,Bow Drill,Ferrocerium Rod,Ferro Rod,Tarp,Hammock,Canteen,Cooking,Longhunter,Trapping
Video Transcription
morning folks I'm Dave Canterbury with self-reliance Outfitters in the Pathfinder school and what I thought I'd do today out here at the forge in the shop is I would try to recreate a pair of hand forged scissors and recreating items from the past and being able to become more self-reliant in the things that we create we can create I think is important but I like to recreate historical items as well and scissors are something that have been used since Egyptian times most of them were the spring style says there's like you see for shearing sheep and things like that's a day on smaller scale the scissors like these that are hand forged overseas or at least they're made overseas that are pivoting type says there's like this really didn't come into being until Egyptian times and they really didn't come into production or full replication or manufacturing until the 1760s in England and then later in the 1830s in Scandinavia but scissors that were like this style with the pivoting Center in them cross-cutting like this we're used even in the Viking era and there are examples of scissors like this that have been found in Viking burials so this type of scissor has been around for a long long time and today we're going to try to recreate that so I'm going to use two pieces of metal stock that are 1095 that are one inch wide and one foot long and I'm going to make each side individually and match them up and then I'm going to try to put them together and make a pair of scissors so stay with me and I'll walk you through the process okay so I've basically taken one side of these shears and matched it up and cut it out of a piece of 1095 and now I'm going to just kind of clean this up so it's the exact profile that I want and then I'm going to make the other side out of another piece of 1095 and then we'll start the assembly and forging process there's not a lot of forging involved in this other than heating things up to bend them and round them out and then of course the heat treating tempering and quenching and tempering of the blades themselves as you can see they're a single bevel edge and they weren't overly sharp surely like a knife blade but they had a fairly steep probably a 30 degree angle single bevel on them and we'll put that on there probably on the belt grinder itself on a two inch belt grinder but that could easily be put in there with an angle grinder as well if you're trying to do some simple tools and you can heat this stuff up if you had to with an ox oxy acetylene torch or something like that if you didn't have a forge so really the first thing I want to do is just clean up some of the jagged edges and I'm just gonna lay this thing right here on the belt to do that I'm just going to get that thing Trude up to the line so that when I trace this on to my second piece I'll have an exact match in the end so the only thing I'm going to do now is just lay this one on top of another piece exactly like it trace it on there with a marker and then I'm going to cut that piece out and if I turn it over it'll be the opposite way so it doesn't matter that I cut it the same because I can always flip it over and it'll be the opposite side okay so there's our second side layout we'll just go over on the bandsaw and chop that dude out and we'll come over here get it straightened up and form matching on this one and then we'll get to work and once we get that cut out if we take our scrap from both sides you've actually got two pretty decent knife blades right there and we can use later on in 1095 so we'll set that scrap aside save that for carving knives or smaller puku style knives down the road here okay so once we get our two sides cut out what we're looking at is this we want those blades to overlap at the tip and don't worry about any of this down here because we're gonna shape that the way we want to hear it momentarily right now what we're looking at is an initial fit up where do we want to put our hole because we've got to drill this thing as well and we'll drill it before we grind the blades in or do anything else while the metal still annealed and soft we'll go ahead and drill our hole in here so we need to figure out where that's going to be and get that in the right spot so I'm gonna take a metal punch here to basically punch myself a spot on there where I'm gonna drill that okay so once we decide how we want this blade to lay against each other then we can kind of come in here figure out a good center point that punch this and we'll just come in here and mark the spot well drill one side then we'll match it up the other side and mark it and drill it on the drill press or with a regular hand drill either one will work okay so now we're gonna find our rivet stock and we can use just a regular nail for that if we want to or we can use a piece of steel round stock and I kind of go between the two I'd like to use nails for pens and knife scales but I think we're gonna want a little bit more beef to this rivet so I think I'm gonna go with a piece of round stock it's bigger diameter than nail so because I've got some scrap laying around here so now I just need to match that up to a drill bit this is 7/32 not quite there this must be a piece of quarter inch round stock I'd say it is so we'll go ahead and cut a quarter inch hole in here and drill it through and then we'll match it up and drill the other side okay so we've got one side drilled and now we're just going to lay it on top again and line things out the way we want to lay when the scissors are done make sure we got an even amount of space there and then we're just going to take a marking pen here double-check everything give ourselves a circle there where we won our hole come in and punch that with our punch again just Center punch it so that we can drill that hole okay once we've got that taken care of you can lay those over the top and just make sure it's exactly what we wanted to be now we need to decide where we're going to put our plunge line on the blades themselves so I'm gonna lay this sideways here for a minute and I'm gonna put one on top of the other as they would lay and by my plunge line I mean where am I gonna put my grind I think I'm gonna start about right here with my grind I'm gonna marked out on both sides just like that and then I'm just going to start my grind here and go down and here and go down by putting it on the same type of jigs that I used for the knives but I'll use the one that I use for the draw knives because it's got about a 30 degree angle on it all right this is the jig that we use for our draw knives and it puts about a thirty degree angle on there so I'm got the side that I've got the plunge line drawn on and I'm gonna move out a little bit away from that but I've got to keep it flat against the jig and I'm just going to use cheap clamp here but I've got to make sure that when I clamp that on there it's not going to move and my plunge line is going to be on the straight side here and I just want to make sure that I can line everything up and see what I'm doing if I need to I'll transfer that plunge line to the top of the knife just like this so I can look at it from above on the sanding belt okay and then we're just going to grind a single bevel grind on that side similar to the draw knives [Music]
[Music]
[Music]
[Music]
okay so there's one side done pretty much you've just got a single bleated or a single bevel grind knife there at about a 30-degree angle and I've ground that down pretty close I've got about half the thickness of a dime maybe left there [Music]
all right so we're measuring our tails here to make sure that they're exactly the same length for both sides we've got rounded out now and now we're going to start to put the curvature in our handles understanding the blades will lay like this and a curve the handle toward
the blade edge [Music]
[Music]
[Music]
[Music]
[Music]
About the Author
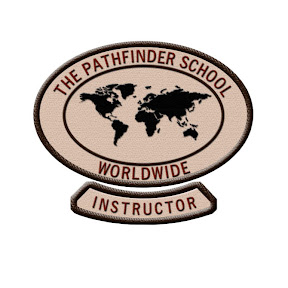
wildernessoutfitters
From the lore of bushcraft to all things related to self-sustainability, the Pathfinder vision is to pass on the knowledge of outdoor self-reliance. Providing basic to advanced self-reliance training and survival gear, our goal is to offer both practical knowledge and survival gear that will stand the test of time. From emergency preparedness to sustainability, the Pathfinder way is to share and educate.
Here you can explore the world of survival knives, survival kits and simple tips on outdoor self-reliance. We are always learning and enjoy passing on the knowledge we acquire.
There is no substitute for having a plan in the event of the unexpected.
More articles from this author
- Black Drawing Salve
- Pace Counting and Dead Reckoning
- Bullet Proof Bushcraft on a Budget Long Guns
- The Witchery of Archery Part 3 Arrows and Arrow Flight
- Sling Bow Final Modification How To
- Journal of the Yurt 29 Q&A
- African Bird Trap
- Journal of the Yurt 37 Stock and Trade
- A Common Man Sustainability Cross Bow
- Modular Packing Discussion
- Rendering Birch Oil, As taught at the PF Pioneer Class by Joe Kellam
- Modern Trapping Series Part 41 Raccoon caught in a False Drain Set.wmv
- Shooting the Recurve Bow (Beginners) with Iris Canterbury.wmv
- Journal of the Yurt 2
- Journal of the Yurt 7
- NINJA SHELTER
- Spring pole Bowdrill Ember
- Cooking Tips and Quick Treats (Garlic Rice and Smoked Sausage)
- 5 Navigation Techniques Every Woodsman Should Know
- Building a Discount Bushcraft Kit Part 5 (Wool Blankets)
- Journal of the Yurt 38 A day in the Life
- Trail Tarp Set up Options Part 1
- Cast Iron Cooking Part 2 Pork Mash Cassarole
- Creating a Fire with Aspen Punk wood and the Sun
- Modern Trapping Series Part 44 Skinning a Mink
- Shoes a Simple Improvised Pattern
- Pathfinder Advanced Class Florida Everglades
- Blacksmithing Part 14 Making Nails
- Bow Saws, a Common Man Bush Tool
- Bow Fishing Equipment Explained
- Kid Testing of the Lightning Strike Fire System
- The Osage Bow Part 6 (Draw Wt and Shooting)
- Modern Camp Set up
- Utilizing Resources Tallow Making Lye Soap
- Apache Foot Trap
- H&R 12 GA Buttstock Mods
- The Quickie Poachers Camp.wmv
- Blacksmithing Part 7 Making Cooking Irons
- Tablet Weaving
- 21st Century Longhunter Processing Tinder Fungus for Use
- Neolithic and Ancient Roman Fire Methods
- Eastern Woodland Trees and their Uses 1
- Using a Compass to take a Visual Bearing
- Journal of the Yurt 24
- Journal of the Yurt 36 12GA R&D
- Kit Mentality the Basics
- Blacksmithing Part 11 Forging a Knife Step 1.wmv
- Beginners Knife Safety Part 1
- Commercial: Dave Canterbury "Makes fire with his beard"
- Modern Trapping Series Part 23 Skinning the Catch
- Starting your net
- Wood Craft on a Budget Part 6 Cookware 2
- Jam Knots 3 that do it all
- Slingshot Forging
- Pathfinder Product Review 11 Flint Knapping Tools
- On the Waters Edge Part 4 Sling Spear
- Pathfinder Product Review #3 The Emergency Shelter Kit
- Pathfinder Product Review #5 The Nessmuk Hand Axe
- Throwing a Knife
- Packable Draw Knife and a Simple Vise for the Woodland Projects
- Bushcraft Kit Shot Show Intro
- Shooting Vanes from a Traditional Bow
- Journal of the Yurt 1
- Testing a Common Man's Survival Bow.wmv
- Diary of the Tipi 4 Primitive Archery Repair Kit.wmv
- ROKON Series Intro
- Cornish Hen Cassarole in an Aluminum Dutch Oven
- Super Shelter Modified for the Eastern Woodlands Part 1
- Improvised Zip Lock Compass.wmv
- 21st Century Longhunter The Versatile #110 Conibear
- Journal of the Yurt 31 Folders and MT's
- Condor Greenland Axe Pathfinder Product Review #12
- Packing for a Trip the 3 C's Concept
- How to get your pattern for a wool blanket shirt
- Brain Tanning Hair On Part 1
- SlingBow DVD
- Fleshing hides: The easy way
- Butcher Knives a Frontier Standard.wmv
- Reviewing a Survival Shotgun Set up.wmv
- Long Guns, Canoe Guns&Testing the Wax Slug 12 GA Load
- Stronghold Haywire Klamper Projects
- Asian Monitor Trap
- NO FAK First Aid Kit
- Journal of the Yurt 6
- Walnut Blueing an H&R 12GA
- Modern Trapping Part 4 Foot Hold Traps
- Mora Camping Axe "Dont save it for the wimpy wood!"
- Quick Run Down of the Final 5 C's of the 10 PC Kit
- 1751 Belt Ax Kit Project Part 2
- Fire Tube
- Journal of the Yurt 28 Spices
- Journal of the Yurt 26 My Shooting Bag
- Utilizing Resources, Glass Arrow Heads
- Iris Intro1.wmv
- PF Cook System for 2017
- Primal Gear Unlimited Compact Folding Survival Bow
- Corn Meal Mush
- Journal of the Yurt 9
- Emergency Fire-Foul Weather
- Boot Care and Boot discussion
- Pathfinder Pocket Hunting System Promo
- Auger Adapter DIY
- Making a Scrap Yard Folding Knife Part 1
- Bug Dope
- Tools and Honing Discussion
- Pine Sap Accelerant
- Journal of the Yurt 5
- On The Waters Edge Part 8 Fileting a Fish
- American Mod to the Asian Bird Trap Snare
- Modern Trapping Series Part 26 Prepping the hide for Tanning
- Modifying Brass Shotgun Shells to accept the 209 Primer.wmv
- Survival Bows (Shaping and Floor Tillering the Stave)
- Woodcrafters Bench Part 4 Spoon Mule Attachment
- Pathfinder School Self Reliance Projects Update 2
- Char Cloth and Ignition Sources
- Wool Blankets Winter Camping Part 2
- Making Woodland Furniture The Dove Tail Joint Lash
- Fire School Part 9 Bowdrill Ember from Horsehoof Fungus
- American Yurt at the Pathfinder School Intro
- Journal of the Yurt 3 Making Hard Tack
- Cast Iron Cooking Part 1 Spicey Rice Dish
- Pathfinder Nessmuk Trail Tarp by Duluth Pack Co
- Take Down Bucksaw Project Wood Craft on a Budget Part 19
- 5 Min Shelter Option Double Wedge
- Swing Arm Cook System from Natural Materials
- Stump Anvil Improvements The Clave
- Throwing the Tomahawk
- Making Corn Flour Cereal.wmv
- Diary of the Tipi 8 Making Gourd Containers Part 1
- Starting Fire with Steel Wool and Ferro Rod
- NEW Gen 2 Small Bushpot
- Exploring the Whelen Lean Part 2
- Converting Your Percussion Cap to 209 SG Primer Ignition (Mag Spark)
- Over Night Scout
- Pathfinder Cribs The Pathfinder Yurt
- Survivability vs Sustainability.wmv
- Self Feeding Fire Part 1 Basic Bushcraft
- Simple Machines 3 Rope Spinner
- Bullet Proof Bushcraft on a Budget Cover
- Wood Craft on a Budget Part 10 Refurbishing Old Tools1
- Survival Basic Series DVD Part 5
- Pathfinder Product Review #14 New Mora Knives
- Addressing Snake Bites
- Top 5 Medicinal and Useful Plants of the Eastern Woodlands Part 1.wmv
- Poplar Dough Bowl Part 1
- Simple Camping Plow Points Part 1
- Clothing for the Cold
- Frontier Fire Methods 2.wmv
- Fishing Kit-Improvments Testing
- Modern Trapping Part 5 Intro to Snares and Snaring
- Equipment List Discussion for Pathfinder Basics
- Processing Small Game Pheasant
- Evolution of Survival
- Black Smithing Part 1 Making a quick Fire Striker from a File
- Modern Trapping Series Part 33 Using PVC in Sets
- Journal of the Yurt 8
- Journal of the Yurt 4
- Introducing the Pathfinder Scout Hawk
- Mini Inferno NEW PRODUCT
- The Common Man's Last Shot- Pocket Pistol
- Scout about and Bacon out
- Simple Bucket Pack Modification
- Navigation by Terrain Feature Association Part 1
- A Quick Bait holder for Catfishing
- Building Traps without Tools
- Journal of the Yurt 27 Securing More Meat
- The Witchery of Archery Remake Part 1 The Two Tracks Long Walker
- Pocket Hunter A Comprehensive Look at Design and Use
- Practicing Fire Methods 1
- Cabin Fever Part 20 Preserving Game meat in Winter
- Cast iron Cooking Part 3 Deep Fried Bass Filets
- Journal of the Yurt 50 Forging a Cookset.wmv
- Journal of the Yurt 23
- Tarp Setups and Research for System Development
- 5x5 Bushfit Kit
- A Review of 3 Pocket Tools
- Bushcraft Tools Fire Piston Test
- Sunfish Lunch'en
- Knapping a Quick Stone Point from a Flake.wmv
- PVC Bait stick Trap
- Bullet Proof Bushcraft on a Budget Containers
- Cooking Squirrel and Rice
- The Spider Shelter Part 3 Finishing up and heating it up!
- Fire School Part 14 Rub Cloth
- Journal of the Yurt 20
- Journal of the Yurt 18
- Journal of the Yurt 41 Pack Goat
- Materia Medica Yarrow 3
- Building a Discount Bushcraft Kit Part 4 (Take Down BuckSaw for Ten Dollars)
- 5 Tools and Functions to manipulate Wood
- Brain Tanning Hair On Part 3
- Grand Opening Invite
- Common Man Self Reliance Bow #2
- Cabin Fever Part 29 ATV Scouting and my Kit 1
- 21st Century Longhunter Mentality and the 5C's
- NEW Council Tool Woodcraft Pack Axe
- 2 Dollar Knife and Sheath Project Part 1
- Reproducing an Antique Draw Shave Part 1
- Basic Multi Use Knots
- New Sling Bow
- Quick Fishing Kit from Common Materials
- Asian Trail Spring Trap
- Natural Cordage Part 2 The Process of Reverse Wrap 2 Ply Cordage
- Ignition Sources, My Belt Kit
- Bushcraft Kitchen Part 1
- Dressing for Cold Weather.wmv
- 5 Minutes to Better Bushcraft Building a Friction Fire Ember
- Torture Test of a Savotta Pack
- Wisdom of the Wall Tent Part 4 Junk on the Bunk
- Full Circle
- Carving a Noggen
- Canvas Ship Hammocks and Weaving a Clew
- Traditional Japanese Water Stone Sharpening
- 5 Minutes to Better Bushcraft Dakota Fire Hole
- Blacksmithing Part 39 Making a Portable Pit Forge
- Dream Hammock System
- Starting Fire with a Compass K&R Alpine
- 5 Wooden Tools
- New Jon Pack Woodsman’s Bed Sleeve
- 5 Minutes to Better Bushcraft proofing and Reproofing
- Mushroom and Plant walk in Sweden
- Mora Adventure 2018 Short clip
- 5 Min Fire and Shelter Conversion.wmv
- Trap Comparison and Thought Process, Modern Trapping Series Part 43
- Simple Fencing
- Rendering and using Raccoon Fat
- Viking research
- Hickory Resources
- Bushpot Chicken and Dumplings
- Woodcrafters Bench Part 2
- 21st Century Longhunter The Oil Cloth Watch Coat
- Game Hooks
- Bill Hawk
- Pathfinder Product Review The JW Trekker
- Basic Camp Overnighter Part 3
- Next Fire Mentality
- 50 Dollar Tool Kit for Green Woodworking
- Pathfinder Product Review #6 The Duluth Pack PF Haversack.wmv
- Steam Bending Wood
- Water Filter Comparison
- Sling Bow (Bow Fishing Mod How To)
- Survival Bow Making(Making a Bow String)
- Making the Packable Draw Knife
- Making A Common Man's Broadhead
- Building a Discount Bushcraft Kit Part 7 (The Blanket Pack)
- Exploring the Whelen Lean
- Blacksmithing on a Budget
- Building a Discount Bushcraft Kit Part 6 (Cheap Small Game Snares)
- Materia Medica INFUSIONS The Woodsman's Expectorant 22
- Fire School Part 8 No Container Char
- Norlund Axes
- Using Flex Seal on a Canvas Pack
- Pathfinder Product review #4 The Pathfinder Trade Knife.wmv
- Knives and Processing Wood
- Axes and Hatchets Wood Craft on a budget Part 15
- Opinel Safety Mod and Penny Knives
- The M44 Mosin Nagant, A Common Man Rifle
- Simple Box Traps Live Rabbit Box
- Grass Thatching
- Frontier Fire Seminar from the Camping and Woodcraft Class
- Rocky Woodland Forge's Woodcraft Tool Kit
- Stack Pack by Short Lane Arms
- Restoring A Scrap Yard Wood Stove
- Diary of the Tipi 10 I love Fire! my EDC.wmv
- PFODJ Ep4 18th Century Woodsman Hunters Camp
- Camp Cookery Baked Rabbit
- Survival Pro Tips 1 Making Fire with an Empty Bic
- Simple Box Traps Mink Box
- Fire School Part 2 Bow Drill Lessons
- Meat Processing Tools
- Fire School Part 7 Strikers, Scapers, and Smooth Strokers
- Tools and Wood Processing
- Medicinal Trees of the Eastern Woodlands 1.wmv
- Hush Puppies on the trail
- Blacksmithing Part 17 Scrap Yard Pick'en
- Hammock Chat
- Knife Making , Material Reduction Knife Start to Finish Part 1
- Belt Pouch EDC
- Useful and Medicinal Trees of the Eastern Woodlands 3
- Using the H&R 12GA for a Muzzeloader
- Ultimate Survival Bows
- Journal of the Yurt 11 Hygiene
- Journal of the Yurt 10 Visit with Jeremy Janey PF School Intructor
- On the Waters Edge 13 Day 2 Mohawk Canoe
- Hygiene from Fire
- Wisdom from the Wall Tent Part 1
- Making a Common Man Limb Quiver for Hunting
- Coyote Consuming the Harvest
- Knife Care in the Field
- Hobo Stew and Corn Bread
- Bushpot Jambalaya and Hushpuppies
- Useful and Medicinal Trees of the Eastern Woodlands 4
- Basic Camp Overnighter Part 1
- Axe Care Made Simple
- Bulletproof Bushcraft on a Budget Part 1
- Snares The Ugly Truth Modern Trapping Part 57
- Kit mentality Useage vs Investment
- Blacksmithing Part 36 The Wind Tunnel Forge
- New Primitive Technologies Discussion
- Blacksmithing Part 13 Forging a Knife Step 3 Heat Treat and Testing
- Fire Lay The Proper Construction and Ignition after a Night of Rain
- Fire Arms Combination for Long Term Sustainability
- Modern Trapping Part 29 Foothold Pocket Set
- Basic Knife Handling and Bush Craft Notches Part 1
- Blacksmithing Part 18 Making a Brake Drum Forge
- Bucking with a HB Cruiser Ax Wood Craft on a Budget Part 16
- Journal of the Yurt 12
- Reloading 12GA with (Pyrodex) Black Powder in the Field
- Skinning a Raccoon with Rope,Modern Trapping Part 32
- The Witchery of Archery Part 2 The Basics
- Honeysuckle resources and a quick update
- Survival Bows (Collecting the Stave, Improvised Draw Knife)
- Skinning a squirrel for a usable hide
- Blacksmithing Part 12 Forging a Knife Step 2 Material Reduction
- Evolution of the 10 C's Part 1
- Shelter Basic Tarp Setups 1
- Fire The Basic Class Presentation
- Mora Garberg Full Tang Discussion and Review
- NEW 2 1 Ltr Bushpot and 64 Oz Bottle
- Shelter Basic Tarp Setups and an E Fire 2
- Mora Dangler made simple
- Simple Machine Woodland Hoist
- Coyote It's whats for Lunch
- Shelter Basic Tarp Setups 3
- A Woodsmans Apothocary
- Wooden Pulleys and Lifting
- Deer Heart and Pepper Gravy Camp Cooking
- Simple Woodcraft Aids
- Overnight Pack Out
- Fire School Part 1 Bow Drill Lessons
- Collapsible Cast Iron Skillet DIY
- Quick Upload Extracting Pine Tar from Fat Wood
- Blacksmithing Part 15 Making tools for Spoons and Ladles
- Forging and making a Primitive Adze
- Trapping Season Prep and Primer Discussion
- Top 10 Non Firearm Meat Gathering Tools
- Haversack Kit
- Pathfinder Advanced Class 1_7_2010 MA, USA.wmv
- Squirrel Hunt with a Flintlock
- Best Medium Game Snare Modified figure 4 Trigger
- Council Tool Hudson Bay Camp Axe
- Gig Discussion and Hunt with Weapon Vision Spear Cam
- 2 Dollar Knife and Sheath Project Part 2
- Go Ruck Rucker Review and Kit layout
- Bushcraft Breakfast Bannock
- On the Waters Edge Part 1 Compact Fishing Rods and Systems
- Toggle Trigger Fishing Variation
- Swiss Army Knife easy Ember , Fire Tips and Tricks
- Roycroft Pack Frame Part 3 Using Shelter Components
- Blacksmithing Part 4 Rounding and Drawing steel to make a Trap Stake
- Fire School Part 13 Ferro Rod Tips
- Tension Bending Pack Boards
- 12GA Shell Bag Contents and Discussion
- Bushpot Convection Oven
- Stretcher Bed Setup
- Pathfinder Folding Skillet
- Making Sweet Corn Bread Drop Biscuits
- Diary of the Tipi 2 Making Hide Glue.wmv
- Otzi s Knife Sheath
- Pathfinder Basic Survival Class Video Diary
- A Common Man's Grease Lamp
- Canterbury Camp Kitchen
- Rokon Winter Packout
- Blacksmith a Squirrel Cooker explained Part 47
- Leather Knife Scales
- M6 Scout Update Review
- The Osage Bow Part 1
- Basic Carving Kit
- Snow Shoes JMHO
- Simplicity
- Final Product Modified Kephart Bedroll by Duluth Pack
- Swedish Lap Vise
- Forging a Custom Carving Axe with Liam Hoffman Part 1
- Toggles The Woodsmans Friend
- Tarp Setups the Foresters Tent and the 4 W's
- Making a Blade Bowl Adze
- The osage Bow Part 4
- Taking a Bearing from your Map made easy
- Journal of the Yurt 43 Stock and Trade Part 2
- Survival JMHO
- Simple Camping Improved Pot Crane System
- Batoning Wood with your Knife
- Improving the Wax Slug Load for 12 GA and Black Powder Equivelant
- Modern Trapping Part 7 Bedding Foot Hold Traps
- Wisdom of the Wall Tent Part 3 Camp Tool Box
- Useful and Medicinal Trees of the Eastern Woodlands 5
- Pine Crate Tool Chest
- Pathfinder School Basic Class Equipment List Rundown
- Diary of the Tipi 11 Care for a Smoothbore Flintlock.wmv
- Baking with a Plank and a Bushpot
- Wood Craft on a Budget Part 3 Sheath Knives Continued
- Building a Discount Bushcraft Kit Part 3 (Food)
- Triple Barrel Shotgun PF Edition Intro
- Maul a good Learning Project
- Meat Preservation Concerns and Setting Snares
- PFODJ Ep 11 Wet Weather Fire Segment
- The Small Common Man Trapping Kit
- Useful and Medicinal Trees of the Eastern Woodlands 2
- Simple Camping Connection Knots 3
- Pathfinder Outdoor Journal Ep1 FULL HD Episode
- Quick Review of the ILBE USMC Assault Pack and Sealine Insert Bag
- Simple Blade Grinding Jig
- Diary of the Tipi 12 Working with Natural Dyes Part 1.wmv
- PF SS Kettle
- Jeff White Bush Knife and a Wet wood Fire
- My Back Yard
- Knives JMHO
- Iris Intro Video Part 2.wmv
- Thanks for Play'en, Bobcat in an MB 450 Released
- Kit Mentality Updates
- Bullet Proof Bushcraft on a Budget PVC Pack Frame
- The Osage Bow Part 5
- The Mocotaugan
- Pathfinder Knife Shop Introduction
- Deadliest Small Game Primitive Trap
- Saami Repair Kit
- Building a Discount Bushcraft Kit
- Stone and Bone (Utilizing Resources) Part 1
- No Map No Problem Part 2
- Arrow Making for the Common Man
- The Wish Bone Trigger Snare New
- Making a quick Spring Lathe
- Using the Slingshot to Hunt Bigger Game
- Bark Basket Part 1
- Scout Camp Common Man Black Powder Setup
- Collecting Back Sinew and Some Meat from a Roadkilled Deer
- Dakota Fire Hole Proper Construction and Use
- Artifact Quality Leather Work
- Bucket Making White Coopering
- PFODJ Ep 5 Axe Tomahawk Segment
- Reverse Figure 4 Dead fall Trigger
- Fire and Bushpots
- Shooting Shot from a 50 Cal BP Rifle
- Tarp Setups Modifed Plow Point
- 50 Cal Blue Ridge Mountain Flint Lock
- Remington Shotgun Model 1889 Double Barrel
- Shrink Pot 1
- Reflector Oven Bread
- Preping the Sling Bow for a Big Game Hunt
- Modern Trapping Coon in Beaver set
- Brimstone Matches and Next Fire Mentality
- No Map No Problem Part 3 Height and Distance
- Saw Maintenance 2 Wood Craft on a Budget Part 14
- SS Canteen Available NOW!~
- Identifiying Flint Chert and other Sparking Rocks
- Trap Sets The Step Down Set Modern Trapping Series Part 48
- Axe Selection and Use
- The Osage Bow Part 2
- Tomahawk from a Rasp Blacksmithing Part 46
- Making Pemmican
- Moonshine Why Carry
- Trailblazer Deliverables Basic Compass Use
- Making the Flemish Bow String in the Bush Part 2
- Simple Camping Hammock use with Wool Blankets
- Forging a Hook Knife
- Finishing a New Old Stock Mora 311
- Survival Basic Series DVD Part 1
- Sharpening an Axe with a Hardware Store Grind
- Putting a Handle on a Mora Blade Blank
- Simple Machine DIY Spring Hammer
- Forging a Tomahawk from a Rasp
- Feathersticks or Shavings
- 21st Century Longhunter Series Combustion
- Fire School Part 15 Pump Drill Fire,Learning the process
- Seneca Pack Frame
- Ever thought about this? Fire Tricks
- Sustainability Long Term,Modern Trapping Series Part 42
- Blacksmithing Part 2 The Folding Small Game Gambrel
- Double Bit Axes Wood Craft on a Budget Part 17
- Sleeping Gear JMHO
- Knapping Arrowheads From Glass Part 1
- Mora Bushcraft Pathfinder
- Making a Cook Tripod with a Chain
- One Match Fire for BSA Bushcraft
- Rope Bed Construction
- The Spider Shelter Part 4, Simple Improvments
- Quick and Easy Tensioner Knot for your Tarp Lines.wmv
- 10 Simple Knife Projects Part 1
- Lighting a Candle with Flint and Steel
- Winter Pack Out
- Utilizing Resources (Making Venison Jerky) Part 2
- Natural Cordage Part 1 Harvesting and Processing Materials
- Asian Bird Trap Laos
- Vines and Withies
- Woodman's Pal
- Five Tool Rule
- Prefered Clothing and Layering for the Woods
- Simple Shadow Navigation Part 1
- Brain Tanning Hair On Part 2
- R&D of the Kephart Bedroll by Dave Canterbury and Duluth Pack
- Light Weight Scouting Pack Set up
- Trapline Diary Part 1 Coon Cuffs
- Survival Basic Series DVD Part 2
- Pathfinder Basics Estimating Distance and Pace Count Lecture
- Super Shelter Modified for the Eastern Woodlands Part 2
- FULL TANG MORA Bushcraft Knife
- Beginners Knife Safety Part 2
- Survival Bows (The Tillering Process)
- Blacksmithing Part 6 Common Man Tools and lighting the Forge
- Building a Discount Bushcraft Kit Part 2
- Sloyd Project 1 Fid
- On the Waters Edge, Trekken and Fishen
- Traditional Cold weather Hammocking
- Knife Making, Material Reduction Knife Start to Finish Part 3
- Trapline Journal Coyote in MB450
- Winterizing the Hammock for the Common Man
- Samick Sage Recurve 8pt Buck Kill
- Large Bushpot Intro
- Bucksaw Modifications
- Fatwood Collecting Processing Igniting
- Aussie Wool Blanket
- Assembling a Custom Classic in the Mora Factory
- Traditional Camp Pack weight
- PFODJ Ep 2
- Hook Knife Part 1
- Making a Bushcraft Knife Part 4
- 1908 A&F Cook Grate
- Nordic Pocket Saw
- Making a Bushcraft Knife Part 1
- PFODJ Ep 5 Moved from the Pay Channel
- PFODJ Progression of Meat Source Gathering
- Experiments in Viking Navigation Viking Sun Stone
- Turkey Tail Materia Medica
- Hook Knife Part 2
- Making a Bushcraft Knife Part 3
- Making a Bushcraft Knife Part 2
- Double on Coons
- The Woodsmans Pantry Plus and the Woodland Chef Cook Kit
- Cooking Bannock in the Bush Pot with a Pack Grill Rack
- Fence Line Snares for Coyote
- Forged Scissors Part 2
- Pathfinder Scout Hammock
- Trappers Cabin Season 2 Part 5 Raccoon Meatloaf
- Trappers Cabin Season 2 Part 2 Firearms
- Trappers Cabin Season 2 Part 7 Fleshing Hides
- WInter Clothing Discussion
- Trappers Cabin Season 2 Part 4 Tail Stripping
- Hammock Chair Hunting Seat
- Trappers Cabin Season 2 Part 1
- Trappers Cabin Season 2 Part 6 Single Shot Maintenance
- Trappers Cabin Season 2 Part 8 Pocket Sets
- Making a Holiday Wreath
- Trappers Cabin Season 2 Part 9 Making Kvass
- Trappers Cabin Season 2 Part 3 Trash Panda
- 110 For Mink
- Trappers Cabin Season 2 Part 13 Wood Stoves
- Morakniv Carbon Steel Garberg
- Trappers Cabin Season 2 Part 14 Releasing a Domestic Animal
- Z Drag with wooden Pulleys
- Trappers Cabin Season 2 Part 12 Log Crossing Set
- Trappers Cabin Season 2 Part 11 Chasing Mink
- Exotac Products and Titan Lighter tips
- Trappers Cabin Season 2 Part 10 Mapping the Creek Bed
- Trappers Cabin Season 2 Part 15
- Trappers Cabin Season 2 Part 16 Last day for a few
- Trappers Cabin Season 2 Part 18 Buck Mink
- Trappers Cabin Season 2 Part 17 Hidden Woodsman Pack
- Bushcrafting a Tarp Clip
- DD Tents
- Neck Knife to Carry or Not to Carry
- Blanket Pin Tripod
- Comprehensive Bow Drill
- Hibiscus Cordage
- The Versatile Marline Spike Hitch
- Hammock Chair Terrapin Outfitters
- Sticky Rice
- Udemy Intro Video
- Conserving the Bic in an emergency
- LL Bean Continental Ruck Sack
- Navigation The X Box Exercise
- Cave Man Conibear Updated
- Limb line Hook Set Device from natural materials
- Solar Embers without Char or Fungus
- Packing up the raised Bed Camp
- Raised Bed Emergency Shelter
- Basket Trap for Crayfish
- Making a Sun Compass
- Ottomani Sun Compass
- Dutchwaregear Chameleon Hammock and Xeon Tarp
- Tulip Poplar Knife Sheath
- Shadow Board Direction Finding
- Dirty by design
- Orienting a Map without a Compass
- Mushroom Foraging Part 2
- 5 Minutes to Better Bushcraft Pot Crane
- Paracord Hammock
- 5 Minutes to Better Bushcraft Quickly Deployable Ridgeline
- 5 Minutes to Better Bushcraft Hanging Camp Gear
- Tighten a Shear Lash Easily
- 5 Minutes to Better Bushcraft Tripod
- 5 Minutes to Better Bushcraft 90 Degree Spine
- Mushroom Foraging
- Broiling Fish with Grill Racks and the SRO Monthly Special
- Exerpt on Basket Weaving at the Bushcraft 101 Class
- 5 Minutes to Better Bushcraft Double Prusik Tensioning System
- Week Long Training Loadout
- Lunch and the Base Camp Cookset
- 5 Minutes to Better Bushcraft 5 Navigational Aids
- 5 Minutes to Better Bushcraft The Angular Advantage
- Last Shadow First Shadow Method
- 5 Minutes to Better Bushcraft Improved Fire Starting
- 5 Minutes to Better Bushcraft Pot Hanger
- Tulip Poplar The Best Eastern Woodland Bushcraft Resource
- 5 Minutes to Better Bushcraft Bark Candle Lantern
- Woodsman's Gear of the 20th Century Part 6
- 5 Minutes to Better Bushcraft The JB Figure 4 Variant
- Mushroom Foraging Part 3
- Woodsman's Gear of the 20th Century Part 3
- 5 Minutes to better Bushcraft other uses for Puffball Mushroom
- Woodsman's Gear of the 20th Century Part 7
- Woodsman's Gear of the 20th Century Part 5
- Fried Puff Ball Mushrooms
- Woodsman's Gear of the 20th Century Part 4
- Using a Strop to Clean, Sharpen, and Hone your Blades
- Woodsman's Gear of the 20th Century Part 1
- Best Survival Deadfall Trigger PDF4
- Woodsman's Gear of the 20th Century Part 2
- Woodsman's Gear of the 20th Century Part 9
- Woodsman's Gear of the 20th Century Part 8
- Woodsmans Gear of the 20th Century Part 10
- Woodsmans Gear of the 20th Century Part 11
- Blood Trailing a Deer
- M6 Takedown Rifle Comparison to the Springfield Scout
- Safe Release of Non Target Species
- French Press Testing and Protyping
- Simple Camp and a Test of the Wildward Lavu
- Pocket Stove Comparison