Fire School Part 1 Bow Drill Lessons
Description
http://www.thepathfinderstore.com
Dave Canterbury, David Canterbury, The Pathfinder School,Bush Craft ,Survival skills, Historical Lore, Primitive Skills, Archery, Hunting, Trapping, Fishing, Navigation, Knives, Axes, Fire, Water, Shelter, Search and Rescue
Tags: Bushcraft,Survival,David Canterbury,Dave Canterbury,Pathfinder,The Pathfinder School,Archery,Hunting,Fishing,Camping,Primitive Skills,Fire,Water,Shelter,Navigation,First Aid,Search and Rescue,Signaling,Prepper,Preparedness,Self Reliance,Survivability,The 10 C's,Knives,Axes,Saws,Bow Drill,Ferrocerium Rod,Ferro Rod,Tarp,Hammock,Canteen,Cooking,Longhunter,Trapping
Video Transcription
[Music]
[Music]
[Music]
what I thought we would do today is start a series called the fire school at the Pathfinder school fire is a primary teaching tool for every class from basic to advanced we generally start out with our basic classes in teaching ways to make fire with the items in your 10 piece kit generally speaking that is a lighter and magnifying glass in a large ferrocerium rod we teach people how to build a proper fire lei how to collect proper tinder and how to affect ignition using their ferrocerium rod using their cigarette lighter saving it even if it's been wet or cold and also how to use magnification to get solar embers and control those to blow a bird nest to flame but I thought what we do in this fire school series is start at the opposite end of the spectrum and start with primitive fire improving a fire is really the last resort in a survival scenario and the reason it is is because it's a complicated way to start fire it has lots and lots of input variables that affect the output and everything in survival just like in life is really a process the inputs always affect the output any variation within those inputs can also affect the output so what I thought we'd do is make a very in-depth detailed video today to start off this series on making a bow drill set and creating an ember from that bow drill set now that's not going to that's not talking about making a fire lay or making the bird nest or making the tinder bundle and all those things we'll go into those as we go I thought what we do today is we would talk about just creating the ember from a bow drill set making a bow drill set from scratch from what we find in the woods with a couple simple tools that we'd have in our backpack and then some of the variation that can be found within the bow drill set and some of the little simple tweaks that you can make to make your bow drill set work better for you and then also the correct inputs that will directly affect the output stay with me and we'll get started one of my favorite materials for bow drill fires in Eastern woodlands is the tulip poplar and tulip poplar tu Li p-pop
is really not a poplar at all it's actually a tulip treat and it's in the Magnolia family but it has very similar properties to all other poplars and poplar in general is a very good species to use for a bow-drill fire other species that are also in the poplar family that are good for bow drill fires are basswood Cottonwood regular everyday poplar Lombardy poplar and things like that
sawtooth Aspen those are all in the poplar family those will all work well tulip poplar is actually sometimes called yellow poplar but it is not truly a poplar although it has the same properties but it does have several things to its advantage in eastern Willows number one there's a lot of them number two they're very easy to identify number three because they drop their branches as they grow usually there's hanging dead to be available it's not always something you find on the ground you can find dead branches very similar to this one is hung up in the thicket here in front of me you can see how white that is from the bark rotting off of it or being torn off of it and that white color almost looks like deer antler is very indicative of a tulip poplar or yellow poplar when you're walking through the woods so it helps you to identify that type tree if you're looking around you see something it looks like deer antler color like that very bright very white looking it's generally going to be a tulip poplar you can then walk up and look at the tree itself look at the bark look at the consistency and that's what we're looking for is the properties of the tree it really doesn't matter what species it is necessarily to us what matters is doesn't have the correct properties and in our case what we want for a bow-drill fire is we really want the properties of this wood to be fairly soft we want something that we can push our fingernail into and it will leave an imprint that's a fairly good indication of how soft that wood is and that will be the right wood or a good wood or a good candidate for Vogel now the other thing they like to look at with this wood to see if it's what I'm looking for or the right consistency is like you just go ahead and cut into with my knife if you've been using your knife for very long you understand what wood feels like when you cut into it and how hard it is if would cuts like butter and I'm just using a more a bush craft block here really good starting bushcraft style knife works really really well for this again you don't spend a lot of money on squidly just got to have the right stuff but you got a good skiing and naveen edge on here if you shave that stuff down and you can feel it's really really soft and it's cutting almost like butter when you cut into it that's a pretty good indicator that this is going to be good wood for bow drill set so here's several branches of tulip poplar we've picked up off the ground in the woods you can see the bark is off of this one completely and the bark on some of these is different colors than the other barks and the reason for that is differentiating ages of decay if you find these ones that are very blackish colors like this they've been dead the longest ones like this that are more light colored on the bark generally speaking have not been dead as long and may not be as dry as others ones like this that have been found on the ground with no bark on them have most likely been dead the longest but if they've been found directly on the ground they may contain moisture this is a good straight piece right here from about right here to here it's fairly straight that's why I picked this piece up I thought that would make a pretty decent spindle now remember that we need really three main components but we need four components for our bow drill set we need a hearth board we need a spindle we need a bearing block and we need a bow generally speaking we can make a spindle and the hearth board from the same wood very easily it would be better to have green wood for both the bow and for the bearing block the bearing block is what gives people the most trouble and they don't realize it we'll talk about that we get to that point so let's look the wood that we have and figure out what we're going to use for our spindle and what piece we're going to use for our hearth would our hearth board first now I'd like to use this piece from my heart board because it's bigger in diameter it's going to need to be wider than our spindle or just a little bit wider than our spindle we could use this as our spindle and cut it down a little bit more and easily be smaller than a diameter of this piece of wood we also want to check the wood to make sure it's not rotten and starting to get real pithy feeling or spongy feeling as long as it's not doing that it should be okay but the longer it's been dead the faster it's going to burn up the least amount of time or the lesser time it's been dead the more chances are it's going to hold moisture the closer to the ground it was the more choice chances are it's going to hold moisture all of these things are important variables that we have to control so as we're cutting into this wood we're going to be checking for all of those things all right let's first look at what we're going to try use for a spindle and besides my bushcraft black I have just a Leatherman super tool multi-tool that's going to give me a small saw a bahco laplander would do the same thing but if your carry option is three tools especially in the beginning or when you're just starting out I would suggest a Leatherman super tool 300 a bahco laplander folding saw and a Mora bushcraft black those tools will serve you very very well for a lot of things and they won't break the bank buying them either let's take this thing and cut it off we'll be able to tell a little bit about this wood just by cutting it off with our saw if it's real real easy to cut it may be pithy and we can look at the end of this push our fingernail into that as well and see how pithy feeling it is see if we think it's possibly too dead to use for this purpose so let's cut the other end and I like my spindles about the span of my fingertip
or my thumb tip to my pinky so I go up in here somewhere and cut that dude off and again I'm feeling see if how pithy that thing feels or how rotten it feels it's fairly straight it's not too bad it's got a little bit of a warp right here but we're going to shave this thing down anyway so we'll see what it looks like when we get a shave down a little further that will tell us more about the consistency or variables within the spindle now generally speaking I never use the knife on my multi-tool for cutting I saved that knife razor sharp that's part of my first-aid so I'm always going to use this more knife to cut with and carve with instead of using that as I'm cutting into this I'm trying to feel what the wood feels like is it carving off pretty smooth is it coming off chunky it's coming off chunky that could be a pretty good indicator that's too rotten if it's coming off fairly smooth that's okay but you can also feel dampness as you go this feels really really bone dry we've got a little bit of a knot right here we're definitely going to use this for the top end of our spindle and we'll talk about that in a little bit as well but I'd rather have the top of my spindle harder than the bottom if that's possible so that it doesn't shoulder out on my handhold
it does feel a little bit chunky to me coming off of there but that could just because really really dry it doesn't feel smooth smooth gently equates to Greenwood or moisture it doesn't feel smooth it feels a little bit shock you can hear that when you're cutting into this and all of those things are important to understand when you're doing this stuff you can look at your shavings on the ground and see what they look like after you've taken them off of your spindle do they look like chunks or do they look like curls they look like curls you're usually pretty safe if they look like chunks probably got some pretty rotten wood that you're working with or starting to rod now we need to get this hump out of here to kind of make this a little bit straighter get a little bit of a hump on this backside the straighter the spindle is the better it's going to spin if this thing is crooked it's going to wobble if it wobbles in the socket it's going to be releasing heat it's not going to run smooth and you're going to have friction in areas you don't want friction so you always want this thing to be smooth as you can get it and run as smooth as you can make it run and we'll look down this thing and see what we got not too bad off it's looking pretty good the other thing I want to look for as I'm going down through here is I don't want any cracks in the end of the spindle or checks if I have cracks and checks as soon as I heat this thing up it's going to open those cracks up and again I'm going to lose heat because heat rises so when this thing is down on the board the heats rising up from the friction and the downward pressure and heats rising up through the crack and it's not staying where I want it that's all important things that I have to think about now let's talk about the shape of this spindle for a minute we want this spindle what I tell my students is the diameter of your spindle should start out about the diameter of your thumb so this one can be shaved down a little bit further than this and the profile overall profile of the spindle imagine a number two pencil those big fatty pencils used to have when you were in grade school that you're about ready to take to the sharpener and you've already used the eraser aren't a few dozen times so you've got kind of a rounded over end and you've got a semi pointed end that you're getting ready taking put in the sharpener because it's getting dull this end is bulldozed over like the eraser so this thing needs to look like that number two Ticonderoga pencil you had in second grade when you're done right now I'm just going around I'm reducing the diameter to get it to the diameter I want and making sure I'm getting rid of those humps to make the exact size I want and keeping it as round as possible so that it will run smooth and won't wobble
okay now I can do a lot of this heavy heavy chunking stuff just off the cuff like this hold it in my hand when I want to start doing something a little bit fire with this thing I'm going to change my tactic a little bit and go to more of a knee levered hold where I can just kind of draw the piece toward me like this take off very controlled amounts of the material just like this steady rotating
this is a very controlled way to carve something it's also a very safe way to carve something I'm not changing anything here if I have to change any angle I just change the angle that I'm pulling the wood right there dry hump is app it's not too shabby as far as the diameter goes that's pretty good remember we had our knot right here so this is the area that I'm going to use for my point now when I make a point on this I generally like to think about this like I said as a number two pencil that's just about to the point of going to the sharper so I'm going to back off of this thing about an inch start to pull in here like I'm serving a tent stake and just keep rotating it around you can see what I'm getting here preparation with fire is 90% of the success failure of a fire so the more time you take to make this right to begin with the better your chances are of getting a coal the first time around and that's really important because it takes a lot less energy to sit here and carve this set then it takes to work that bow drill and if you don't get your coal the first time you start to run that bow drill every time you do it consecutively after that you're going to have less and less energy to accomplish the task you may have marginal chords that you're using or cords you had to fashion off the landscape and you may only get one shot so you really need to take your time at this to get this part right so you have the best chance of success the very first time don't rush this now I'm looking at this thing to see how much pith there isn't a center because that will crush in the handhold so I'm just going to kind of bulldoze this over a little bit right where that pith is and I'm going to be a little bit more dull again that's just getting used to understanding the material I think there's a pretty good amount of pith right in the middle of that thing so to circumvent that a little bit I'm going to make that thing a little bit bigger around then I may generally make it because I know that's going to crush as that crushes I'm going to start to shoulder out inside my socket for my handhold which is going to cause friction in the top instead of the friction being
the bottom now the bottom of this needs to look like an eraser basically so I'm going to start taking chunks just off to the side just like this I'm just kind of going in an angle at it all the way around and if I have facets on there because of that that's okay with me it was fast it's not going to hurt anything they're actually going to add friction once they go all the way around I move up a little bit about half way and they just keep knocking that off and moving up and knocking it off and moving it up and knocking it off until I get a nice rounded shape on there again very similar to a used eraser as even as I can get it that looks pretty good again I'm seeing pith right there and that concerns me a little bit but not a ton it just means that the spindle is going to wear down pretty fast but I'm only planning on having to use it the one time that's part of the progression of fire I don't want to keep making bow drill sets or keep making bow drill fires I want to make one and then never have to make another one my progression of fire will allow me not to have to do this twice
About the Author
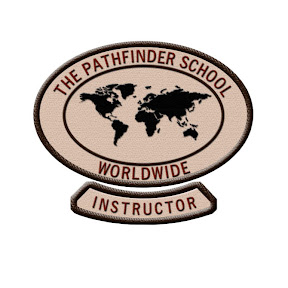
wildernessoutfitters
From the lore of bushcraft to all things related to self-sustainability, the Pathfinder vision is to pass on the knowledge of outdoor self-reliance. Providing basic to advanced self-reliance training and survival gear, our goal is to offer both practical knowledge and survival gear that will stand the test of time. From emergency preparedness to sustainability, the Pathfinder way is to share and educate.
Here you can explore the world of survival knives, survival kits and simple tips on outdoor self-reliance. We are always learning and enjoy passing on the knowledge we acquire.
There is no substitute for having a plan in the event of the unexpected.
More articles from this author
- Black Drawing Salve
- Pace Counting and Dead Reckoning
- Bullet Proof Bushcraft on a Budget Long Guns
- The Witchery of Archery Part 3 Arrows and Arrow Flight
- Sling Bow Final Modification How To
- Journal of the Yurt 29 Q&A
- African Bird Trap
- Journal of the Yurt 37 Stock and Trade
- A Common Man Sustainability Cross Bow
- Modular Packing Discussion
- Rendering Birch Oil, As taught at the PF Pioneer Class by Joe Kellam
- Modern Trapping Series Part 41 Raccoon caught in a False Drain Set.wmv
- Shooting the Recurve Bow (Beginners) with Iris Canterbury.wmv
- Journal of the Yurt 2
- Journal of the Yurt 7
- NINJA SHELTER
- Spring pole Bowdrill Ember
- Cooking Tips and Quick Treats (Garlic Rice and Smoked Sausage)
- 5 Navigation Techniques Every Woodsman Should Know
- Building a Discount Bushcraft Kit Part 5 (Wool Blankets)
- Journal of the Yurt 38 A day in the Life
- Trail Tarp Set up Options Part 1
- Cast Iron Cooking Part 2 Pork Mash Cassarole
- Creating a Fire with Aspen Punk wood and the Sun
- Modern Trapping Series Part 44 Skinning a Mink
- Shoes a Simple Improvised Pattern
- Pathfinder Advanced Class Florida Everglades
- Blacksmithing Part 14 Making Nails
- Bow Saws, a Common Man Bush Tool
- Bow Fishing Equipment Explained
- Kid Testing of the Lightning Strike Fire System
- The Osage Bow Part 6 (Draw Wt and Shooting)
- Modern Camp Set up
- Utilizing Resources Tallow Making Lye Soap
- Apache Foot Trap
- H&R 12 GA Buttstock Mods
- The Quickie Poachers Camp.wmv
- Blacksmithing Part 7 Making Cooking Irons
- Tablet Weaving
- 21st Century Longhunter Processing Tinder Fungus for Use
- Neolithic and Ancient Roman Fire Methods
- Eastern Woodland Trees and their Uses 1
- Using a Compass to take a Visual Bearing
- Journal of the Yurt 24
- Journal of the Yurt 36 12GA R&D
- Kit Mentality the Basics
- Blacksmithing Part 11 Forging a Knife Step 1.wmv
- Beginners Knife Safety Part 1
- Commercial: Dave Canterbury "Makes fire with his beard"
- Modern Trapping Series Part 23 Skinning the Catch
- Starting your net
- Wood Craft on a Budget Part 6 Cookware 2
- Jam Knots 3 that do it all
- Slingshot Forging
- Pathfinder Product Review 11 Flint Knapping Tools
- On the Waters Edge Part 4 Sling Spear
- Pathfinder Product Review #3 The Emergency Shelter Kit
- Pathfinder Product Review #5 The Nessmuk Hand Axe
- Throwing a Knife
- Packable Draw Knife and a Simple Vise for the Woodland Projects
- Bushcraft Kit Shot Show Intro
- Shooting Vanes from a Traditional Bow
- Journal of the Yurt 1
- Testing a Common Man's Survival Bow.wmv
- Diary of the Tipi 4 Primitive Archery Repair Kit.wmv
- ROKON Series Intro
- Cornish Hen Cassarole in an Aluminum Dutch Oven
- Super Shelter Modified for the Eastern Woodlands Part 1
- Improvised Zip Lock Compass.wmv
- 21st Century Longhunter The Versatile #110 Conibear
- Journal of the Yurt 31 Folders and MT's
- Condor Greenland Axe Pathfinder Product Review #12
- Packing for a Trip the 3 C's Concept
- How to get your pattern for a wool blanket shirt
- Brain Tanning Hair On Part 1
- SlingBow DVD
- Fleshing hides: The easy way
- Butcher Knives a Frontier Standard.wmv
- Reviewing a Survival Shotgun Set up.wmv
- Long Guns, Canoe Guns&Testing the Wax Slug 12 GA Load
- Stronghold Haywire Klamper Projects
- Asian Monitor Trap
- NO FAK First Aid Kit
- Journal of the Yurt 6
- Walnut Blueing an H&R 12GA
- Modern Trapping Part 4 Foot Hold Traps
- Mora Camping Axe "Dont save it for the wimpy wood!"
- Quick Run Down of the Final 5 C's of the 10 PC Kit
- 1751 Belt Ax Kit Project Part 2
- Fire Tube
- Journal of the Yurt 28 Spices
- Journal of the Yurt 26 My Shooting Bag
- Utilizing Resources, Glass Arrow Heads
- Iris Intro1.wmv
- PF Cook System for 2017
- Primal Gear Unlimited Compact Folding Survival Bow
- Corn Meal Mush
- Journal of the Yurt 9
- Emergency Fire-Foul Weather
- Boot Care and Boot discussion
- Pathfinder Pocket Hunting System Promo
- Auger Adapter DIY
- Making a Scrap Yard Folding Knife Part 1
- Bug Dope
- Tools and Honing Discussion
- Pine Sap Accelerant
- Journal of the Yurt 5
- On The Waters Edge Part 8 Fileting a Fish
- American Mod to the Asian Bird Trap Snare
- Modern Trapping Series Part 26 Prepping the hide for Tanning
- Modifying Brass Shotgun Shells to accept the 209 Primer.wmv
- Survival Bows (Shaping and Floor Tillering the Stave)
- Woodcrafters Bench Part 4 Spoon Mule Attachment
- Pathfinder School Self Reliance Projects Update 2
- Char Cloth and Ignition Sources
- Wool Blankets Winter Camping Part 2
- Making Woodland Furniture The Dove Tail Joint Lash
- Fire School Part 9 Bowdrill Ember from Horsehoof Fungus
- American Yurt at the Pathfinder School Intro
- Journal of the Yurt 3 Making Hard Tack
- Cast Iron Cooking Part 1 Spicey Rice Dish
- Pathfinder Nessmuk Trail Tarp by Duluth Pack Co
- Take Down Bucksaw Project Wood Craft on a Budget Part 19
- 5 Min Shelter Option Double Wedge
- Swing Arm Cook System from Natural Materials
- Stump Anvil Improvements The Clave
- Throwing the Tomahawk
- Making Corn Flour Cereal.wmv
- Diary of the Tipi 8 Making Gourd Containers Part 1
- Starting Fire with Steel Wool and Ferro Rod
- NEW Gen 2 Small Bushpot
- Exploring the Whelen Lean Part 2
- Converting Your Percussion Cap to 209 SG Primer Ignition (Mag Spark)
- Over Night Scout
- Pathfinder Cribs The Pathfinder Yurt
- Survivability vs Sustainability.wmv
- Self Feeding Fire Part 1 Basic Bushcraft
- Simple Machines 3 Rope Spinner
- Bullet Proof Bushcraft on a Budget Cover
- Wood Craft on a Budget Part 10 Refurbishing Old Tools1
- Survival Basic Series DVD Part 5
- Pathfinder Product Review #14 New Mora Knives
- Addressing Snake Bites
- Top 5 Medicinal and Useful Plants of the Eastern Woodlands Part 1.wmv
- Poplar Dough Bowl Part 1
- Simple Camping Plow Points Part 1
- Clothing for the Cold
- Frontier Fire Methods 2.wmv
- Fishing Kit-Improvments Testing
- Modern Trapping Part 5 Intro to Snares and Snaring
- Equipment List Discussion for Pathfinder Basics
- Processing Small Game Pheasant
- Evolution of Survival
- Black Smithing Part 1 Making a quick Fire Striker from a File
- Modern Trapping Series Part 33 Using PVC in Sets
- Journal of the Yurt 8
- Journal of the Yurt 4
- Introducing the Pathfinder Scout Hawk
- Mini Inferno NEW PRODUCT
- The Common Man's Last Shot- Pocket Pistol
- Scout about and Bacon out
- Simple Bucket Pack Modification
- Navigation by Terrain Feature Association Part 1
- A Quick Bait holder for Catfishing
- Building Traps without Tools
- Journal of the Yurt 27 Securing More Meat
- The Witchery of Archery Remake Part 1 The Two Tracks Long Walker
- Pocket Hunter A Comprehensive Look at Design and Use
- Practicing Fire Methods 1
- Cabin Fever Part 20 Preserving Game meat in Winter
- Cast iron Cooking Part 3 Deep Fried Bass Filets
- Journal of the Yurt 50 Forging a Cookset.wmv
- Journal of the Yurt 23
- Tarp Setups and Research for System Development
- 5x5 Bushfit Kit
- A Review of 3 Pocket Tools
- Bushcraft Tools Fire Piston Test
- Sunfish Lunch'en
- Knapping a Quick Stone Point from a Flake.wmv
- PVC Bait stick Trap
- Bullet Proof Bushcraft on a Budget Containers
- Cooking Squirrel and Rice
- The Spider Shelter Part 3 Finishing up and heating it up!
- Fire School Part 14 Rub Cloth
- Journal of the Yurt 20
- Journal of the Yurt 18
- Journal of the Yurt 41 Pack Goat
- Materia Medica Yarrow 3
- Building a Discount Bushcraft Kit Part 4 (Take Down BuckSaw for Ten Dollars)
- 5 Tools and Functions to manipulate Wood
- Brain Tanning Hair On Part 3
- Grand Opening Invite
- Common Man Self Reliance Bow #2
- Cabin Fever Part 29 ATV Scouting and my Kit 1
- 21st Century Longhunter Mentality and the 5C's
- NEW Council Tool Woodcraft Pack Axe
- 2 Dollar Knife and Sheath Project Part 1
- Reproducing an Antique Draw Shave Part 1
- Basic Multi Use Knots
- New Sling Bow
- Quick Fishing Kit from Common Materials
- Asian Trail Spring Trap
- Natural Cordage Part 2 The Process of Reverse Wrap 2 Ply Cordage
- Ignition Sources, My Belt Kit
- Bushcraft Kitchen Part 1
- Dressing for Cold Weather.wmv
- 5 Minutes to Better Bushcraft Building a Friction Fire Ember
- Torture Test of a Savotta Pack
- Wisdom of the Wall Tent Part 4 Junk on the Bunk
- Full Circle
- Carving a Noggen
- Canvas Ship Hammocks and Weaving a Clew
- Traditional Japanese Water Stone Sharpening
- 5 Minutes to Better Bushcraft Dakota Fire Hole
- Blacksmithing Part 39 Making a Portable Pit Forge
- Dream Hammock System
- Starting Fire with a Compass K&R Alpine
- 5 Wooden Tools
- New Jon Pack Woodsman’s Bed Sleeve
- 5 Minutes to Better Bushcraft proofing and Reproofing
- Mushroom and Plant walk in Sweden
- Mora Adventure 2018 Short clip
- 5 Min Fire and Shelter Conversion.wmv
- Trap Comparison and Thought Process, Modern Trapping Series Part 43
- Simple Fencing
- Rendering and using Raccoon Fat
- Viking research
- Hickory Resources
- Bushpot Chicken and Dumplings
- Woodcrafters Bench Part 2
- 21st Century Longhunter The Oil Cloth Watch Coat
- Game Hooks
- Bill Hawk
- Pathfinder Product Review The JW Trekker
- Basic Camp Overnighter Part 3
- Next Fire Mentality
- 50 Dollar Tool Kit for Green Woodworking
- Pathfinder Product Review #6 The Duluth Pack PF Haversack.wmv
- Steam Bending Wood
- Water Filter Comparison
- Sling Bow (Bow Fishing Mod How To)
- Survival Bow Making(Making a Bow String)
- Making the Packable Draw Knife
- Making A Common Man's Broadhead
- Building a Discount Bushcraft Kit Part 7 (The Blanket Pack)
- Exploring the Whelen Lean
- Blacksmithing on a Budget
- Building a Discount Bushcraft Kit Part 6 (Cheap Small Game Snares)
- Materia Medica INFUSIONS The Woodsman's Expectorant 22
- Fire School Part 8 No Container Char
- Norlund Axes
- Using Flex Seal on a Canvas Pack
- Pathfinder Product review #4 The Pathfinder Trade Knife.wmv
- Knives and Processing Wood
- Axes and Hatchets Wood Craft on a budget Part 15
- Opinel Safety Mod and Penny Knives
- The M44 Mosin Nagant, A Common Man Rifle
- Simple Box Traps Live Rabbit Box
- Grass Thatching
- Frontier Fire Seminar from the Camping and Woodcraft Class
- Rocky Woodland Forge's Woodcraft Tool Kit
- Stack Pack by Short Lane Arms
- Restoring A Scrap Yard Wood Stove
- Diary of the Tipi 10 I love Fire! my EDC.wmv
- PFODJ Ep4 18th Century Woodsman Hunters Camp
- Camp Cookery Baked Rabbit
- Survival Pro Tips 1 Making Fire with an Empty Bic
- Simple Box Traps Mink Box
- Fire School Part 2 Bow Drill Lessons
- Meat Processing Tools
- Fire School Part 7 Strikers, Scapers, and Smooth Strokers
- Tools and Wood Processing
- Medicinal Trees of the Eastern Woodlands 1.wmv
- Hush Puppies on the trail
- Blacksmithing Part 17 Scrap Yard Pick'en
- Hammock Chat
- Knife Making , Material Reduction Knife Start to Finish Part 1
- Belt Pouch EDC
- Useful and Medicinal Trees of the Eastern Woodlands 3
- Using the H&R 12GA for a Muzzeloader
- Ultimate Survival Bows
- Journal of the Yurt 11 Hygiene
- Journal of the Yurt 10 Visit with Jeremy Janey PF School Intructor
- On the Waters Edge 13 Day 2 Mohawk Canoe
- Hygiene from Fire
- Wisdom from the Wall Tent Part 1
- Making a Common Man Limb Quiver for Hunting
- Coyote Consuming the Harvest
- Knife Care in the Field
- Hobo Stew and Corn Bread
- Bushpot Jambalaya and Hushpuppies
- Useful and Medicinal Trees of the Eastern Woodlands 4
- Basic Camp Overnighter Part 1
- Axe Care Made Simple
- Bulletproof Bushcraft on a Budget Part 1
- Snares The Ugly Truth Modern Trapping Part 57
- Kit mentality Useage vs Investment
- Blacksmithing Part 36 The Wind Tunnel Forge
- New Primitive Technologies Discussion
- Blacksmithing Part 13 Forging a Knife Step 3 Heat Treat and Testing
- Fire Lay The Proper Construction and Ignition after a Night of Rain
- Fire Arms Combination for Long Term Sustainability
- Modern Trapping Part 29 Foothold Pocket Set
- Basic Knife Handling and Bush Craft Notches Part 1
- Blacksmithing Part 18 Making a Brake Drum Forge
- Bucking with a HB Cruiser Ax Wood Craft on a Budget Part 16
- Journal of the Yurt 12
- Reloading 12GA with (Pyrodex) Black Powder in the Field
- Skinning a Raccoon with Rope,Modern Trapping Part 32
- The Witchery of Archery Part 2 The Basics
- Honeysuckle resources and a quick update
- Survival Bows (Collecting the Stave, Improvised Draw Knife)
- Skinning a squirrel for a usable hide
- Blacksmithing Part 12 Forging a Knife Step 2 Material Reduction
- Evolution of the 10 C's Part 1
- Shelter Basic Tarp Setups 1
- Fire The Basic Class Presentation
- Mora Garberg Full Tang Discussion and Review
- NEW 2 1 Ltr Bushpot and 64 Oz Bottle
- Shelter Basic Tarp Setups and an E Fire 2
- Mora Dangler made simple
- Simple Machine Woodland Hoist
- Coyote It's whats for Lunch
- Shelter Basic Tarp Setups 3
- A Woodsmans Apothocary
- Wooden Pulleys and Lifting
- Deer Heart and Pepper Gravy Camp Cooking
- Simple Woodcraft Aids
- Overnight Pack Out
- Collapsible Cast Iron Skillet DIY
- Quick Upload Extracting Pine Tar from Fat Wood
- Blacksmithing Part 15 Making tools for Spoons and Ladles
- Forging and making a Primitive Adze
- Trapping Season Prep and Primer Discussion
- Top 10 Non Firearm Meat Gathering Tools
- Haversack Kit
- Pathfinder Advanced Class 1_7_2010 MA, USA.wmv
- Squirrel Hunt with a Flintlock
- Best Medium Game Snare Modified figure 4 Trigger
- Council Tool Hudson Bay Camp Axe
- Gig Discussion and Hunt with Weapon Vision Spear Cam
- 2 Dollar Knife and Sheath Project Part 2
- Go Ruck Rucker Review and Kit layout
- Bushcraft Breakfast Bannock
- On the Waters Edge Part 1 Compact Fishing Rods and Systems
- Toggle Trigger Fishing Variation
- Swiss Army Knife easy Ember , Fire Tips and Tricks
- Roycroft Pack Frame Part 3 Using Shelter Components
- Blacksmithing Part 4 Rounding and Drawing steel to make a Trap Stake
- Fire School Part 13 Ferro Rod Tips
- Tension Bending Pack Boards
- 12GA Shell Bag Contents and Discussion
- Bushpot Convection Oven
- Stretcher Bed Setup
- Pathfinder Folding Skillet
- Making Sweet Corn Bread Drop Biscuits
- Diary of the Tipi 2 Making Hide Glue.wmv
- Otzi s Knife Sheath
- Pathfinder Basic Survival Class Video Diary
- A Common Man's Grease Lamp
- Canterbury Camp Kitchen
- Rokon Winter Packout
- Blacksmith a Squirrel Cooker explained Part 47
- Leather Knife Scales
- M6 Scout Update Review
- The Osage Bow Part 1
- Basic Carving Kit
- Snow Shoes JMHO
- Simplicity
- Final Product Modified Kephart Bedroll by Duluth Pack
- Swedish Lap Vise
- Forging a Custom Carving Axe with Liam Hoffman Part 1
- Toggles The Woodsmans Friend
- Tarp Setups the Foresters Tent and the 4 W's
- Making a Blade Bowl Adze
- The osage Bow Part 4
- Taking a Bearing from your Map made easy
- Journal of the Yurt 43 Stock and Trade Part 2
- Survival JMHO
- Simple Camping Improved Pot Crane System
- Batoning Wood with your Knife
- Improving the Wax Slug Load for 12 GA and Black Powder Equivelant
- Modern Trapping Part 7 Bedding Foot Hold Traps
- Wisdom of the Wall Tent Part 3 Camp Tool Box
- Useful and Medicinal Trees of the Eastern Woodlands 5
- Pine Crate Tool Chest
- Pathfinder School Basic Class Equipment List Rundown
- Diary of the Tipi 11 Care for a Smoothbore Flintlock.wmv
- Baking with a Plank and a Bushpot
- Wood Craft on a Budget Part 3 Sheath Knives Continued
- Building a Discount Bushcraft Kit Part 3 (Food)
- Triple Barrel Shotgun PF Edition Intro
- Maul a good Learning Project
- Meat Preservation Concerns and Setting Snares
- PFODJ Ep 11 Wet Weather Fire Segment
- The Small Common Man Trapping Kit
- Useful and Medicinal Trees of the Eastern Woodlands 2
- Simple Camping Connection Knots 3
- Pathfinder Outdoor Journal Ep1 FULL HD Episode
- Quick Review of the ILBE USMC Assault Pack and Sealine Insert Bag
- Simple Blade Grinding Jig
- Diary of the Tipi 12 Working with Natural Dyes Part 1.wmv
- PF SS Kettle
- Jeff White Bush Knife and a Wet wood Fire
- My Back Yard
- Knives JMHO
- Iris Intro Video Part 2.wmv
- Thanks for Play'en, Bobcat in an MB 450 Released
- Kit Mentality Updates
- Bullet Proof Bushcraft on a Budget PVC Pack Frame
- The Osage Bow Part 5
- The Mocotaugan
- Pathfinder Knife Shop Introduction
- Deadliest Small Game Primitive Trap
- Saami Repair Kit
- Building a Discount Bushcraft Kit
- Stone and Bone (Utilizing Resources) Part 1
- No Map No Problem Part 2
- Arrow Making for the Common Man
- The Wish Bone Trigger Snare New
- Making a quick Spring Lathe
- Using the Slingshot to Hunt Bigger Game
- Bark Basket Part 1
- Scout Camp Common Man Black Powder Setup
- Collecting Back Sinew and Some Meat from a Roadkilled Deer
- Dakota Fire Hole Proper Construction and Use
- Artifact Quality Leather Work
- Bucket Making White Coopering
- PFODJ Ep 5 Axe Tomahawk Segment
- Reverse Figure 4 Dead fall Trigger
- Fire and Bushpots
- Shooting Shot from a 50 Cal BP Rifle
- Tarp Setups Modifed Plow Point
- 50 Cal Blue Ridge Mountain Flint Lock
- Remington Shotgun Model 1889 Double Barrel
- Shrink Pot 1
- Reflector Oven Bread
- Preping the Sling Bow for a Big Game Hunt
- Modern Trapping Coon in Beaver set
- Brimstone Matches and Next Fire Mentality
- No Map No Problem Part 3 Height and Distance
- Saw Maintenance 2 Wood Craft on a Budget Part 14
- SS Canteen Available NOW!~
- Identifiying Flint Chert and other Sparking Rocks
- Trap Sets The Step Down Set Modern Trapping Series Part 48
- Axe Selection and Use
- The Osage Bow Part 2
- Tomahawk from a Rasp Blacksmithing Part 46
- Making Pemmican
- Moonshine Why Carry
- Trailblazer Deliverables Basic Compass Use
- Making the Flemish Bow String in the Bush Part 2
- Simple Camping Hammock use with Wool Blankets
- Forging a Hook Knife
- Finishing a New Old Stock Mora 311
- Survival Basic Series DVD Part 1
- Sharpening an Axe with a Hardware Store Grind
- Putting a Handle on a Mora Blade Blank
- Simple Machine DIY Spring Hammer
- Forging a Tomahawk from a Rasp
- Feathersticks or Shavings
- 21st Century Longhunter Series Combustion
- Fire School Part 15 Pump Drill Fire,Learning the process
- Seneca Pack Frame
- Ever thought about this? Fire Tricks
- Sustainability Long Term,Modern Trapping Series Part 42
- Blacksmithing Part 2 The Folding Small Game Gambrel
- Double Bit Axes Wood Craft on a Budget Part 17
- Sleeping Gear JMHO
- Knapping Arrowheads From Glass Part 1
- Mora Bushcraft Pathfinder
- Making a Cook Tripod with a Chain
- One Match Fire for BSA Bushcraft
- Rope Bed Construction
- The Spider Shelter Part 4, Simple Improvments
- Quick and Easy Tensioner Knot for your Tarp Lines.wmv
- 10 Simple Knife Projects Part 1
- Lighting a Candle with Flint and Steel
- Winter Pack Out
- Utilizing Resources (Making Venison Jerky) Part 2
- Natural Cordage Part 1 Harvesting and Processing Materials
- Asian Bird Trap Laos
- Vines and Withies
- Woodman's Pal
- Five Tool Rule
- Prefered Clothing and Layering for the Woods
- Simple Shadow Navigation Part 1
- Brain Tanning Hair On Part 2
- R&D of the Kephart Bedroll by Dave Canterbury and Duluth Pack
- Light Weight Scouting Pack Set up
- Trapline Diary Part 1 Coon Cuffs
- Survival Basic Series DVD Part 2
- Pathfinder Basics Estimating Distance and Pace Count Lecture
- Super Shelter Modified for the Eastern Woodlands Part 2
- FULL TANG MORA Bushcraft Knife
- Beginners Knife Safety Part 2
- Survival Bows (The Tillering Process)
- Blacksmithing Part 6 Common Man Tools and lighting the Forge
- Building a Discount Bushcraft Kit Part 2
- Sloyd Project 1 Fid
- On the Waters Edge, Trekken and Fishen
- Traditional Cold weather Hammocking
- Knife Making, Material Reduction Knife Start to Finish Part 3
- Trapline Journal Coyote in MB450
- Winterizing the Hammock for the Common Man
- Samick Sage Recurve 8pt Buck Kill
- Large Bushpot Intro
- Bucksaw Modifications
- Fatwood Collecting Processing Igniting
- Aussie Wool Blanket
- Assembling a Custom Classic in the Mora Factory
- Traditional Camp Pack weight
- PFODJ Ep 2
- Hook Knife Part 1
- Making a Bushcraft Knife Part 4
- 1908 A&F Cook Grate
- Nordic Pocket Saw
- Making a Bushcraft Knife Part 1
- PFODJ Ep 5 Moved from the Pay Channel
- PFODJ Progression of Meat Source Gathering
- Experiments in Viking Navigation Viking Sun Stone
- Turkey Tail Materia Medica
- Hook Knife Part 2
- Making a Bushcraft Knife Part 3
- Making a Bushcraft Knife Part 2
- Double on Coons
- The Woodsmans Pantry Plus and the Woodland Chef Cook Kit
- Cooking Bannock in the Bush Pot with a Pack Grill Rack
- Fence Line Snares for Coyote
- Forged Scissors Part 2
- Forged Scissors Part 1
- Pathfinder Scout Hammock
- Trappers Cabin Season 2 Part 5 Raccoon Meatloaf
- Trappers Cabin Season 2 Part 2 Firearms
- Trappers Cabin Season 2 Part 7 Fleshing Hides
- WInter Clothing Discussion
- Trappers Cabin Season 2 Part 4 Tail Stripping
- Hammock Chair Hunting Seat
- Trappers Cabin Season 2 Part 1
- Trappers Cabin Season 2 Part 6 Single Shot Maintenance
- Trappers Cabin Season 2 Part 8 Pocket Sets
- Making a Holiday Wreath
- Trappers Cabin Season 2 Part 9 Making Kvass
- Trappers Cabin Season 2 Part 3 Trash Panda
- 110 For Mink
- Trappers Cabin Season 2 Part 13 Wood Stoves
- Morakniv Carbon Steel Garberg
- Trappers Cabin Season 2 Part 14 Releasing a Domestic Animal
- Z Drag with wooden Pulleys
- Trappers Cabin Season 2 Part 12 Log Crossing Set
- Trappers Cabin Season 2 Part 11 Chasing Mink
- Exotac Products and Titan Lighter tips
- Trappers Cabin Season 2 Part 10 Mapping the Creek Bed
- Trappers Cabin Season 2 Part 15
- Trappers Cabin Season 2 Part 16 Last day for a few
- Trappers Cabin Season 2 Part 18 Buck Mink
- Trappers Cabin Season 2 Part 17 Hidden Woodsman Pack
- Bushcrafting a Tarp Clip
- DD Tents
- Neck Knife to Carry or Not to Carry
- Blanket Pin Tripod
- Comprehensive Bow Drill
- Hibiscus Cordage
- The Versatile Marline Spike Hitch
- Hammock Chair Terrapin Outfitters
- Sticky Rice
- Udemy Intro Video
- Conserving the Bic in an emergency
- LL Bean Continental Ruck Sack
- Navigation The X Box Exercise
- Cave Man Conibear Updated
- Limb line Hook Set Device from natural materials
- Solar Embers without Char or Fungus
- Packing up the raised Bed Camp
- Raised Bed Emergency Shelter
- Basket Trap for Crayfish
- Making a Sun Compass
- Ottomani Sun Compass
- Dutchwaregear Chameleon Hammock and Xeon Tarp
- Tulip Poplar Knife Sheath
- Shadow Board Direction Finding
- Dirty by design
- Orienting a Map without a Compass
- Mushroom Foraging Part 2
- 5 Minutes to Better Bushcraft Pot Crane
- Paracord Hammock
- 5 Minutes to Better Bushcraft Quickly Deployable Ridgeline
- 5 Minutes to Better Bushcraft Hanging Camp Gear
- Tighten a Shear Lash Easily
- 5 Minutes to Better Bushcraft Tripod
- 5 Minutes to Better Bushcraft 90 Degree Spine
- Mushroom Foraging
- Broiling Fish with Grill Racks and the SRO Monthly Special
- Exerpt on Basket Weaving at the Bushcraft 101 Class
- 5 Minutes to Better Bushcraft Double Prusik Tensioning System
- Week Long Training Loadout
- Lunch and the Base Camp Cookset
- 5 Minutes to Better Bushcraft 5 Navigational Aids
- 5 Minutes to Better Bushcraft The Angular Advantage
- Last Shadow First Shadow Method
- 5 Minutes to Better Bushcraft Improved Fire Starting
- 5 Minutes to Better Bushcraft Pot Hanger
- Tulip Poplar The Best Eastern Woodland Bushcraft Resource
- 5 Minutes to Better Bushcraft Bark Candle Lantern
- Woodsman's Gear of the 20th Century Part 6
- 5 Minutes to Better Bushcraft The JB Figure 4 Variant
- Mushroom Foraging Part 3
- Woodsman's Gear of the 20th Century Part 3
- 5 Minutes to better Bushcraft other uses for Puffball Mushroom
- Woodsman's Gear of the 20th Century Part 7
- Woodsman's Gear of the 20th Century Part 5
- Fried Puff Ball Mushrooms
- Woodsman's Gear of the 20th Century Part 4
- Using a Strop to Clean, Sharpen, and Hone your Blades
- Woodsman's Gear of the 20th Century Part 1
- Best Survival Deadfall Trigger PDF4
- Woodsman's Gear of the 20th Century Part 2
- Woodsman's Gear of the 20th Century Part 9
- Woodsman's Gear of the 20th Century Part 8
- Woodsmans Gear of the 20th Century Part 10
- Woodsmans Gear of the 20th Century Part 11
- Blood Trailing a Deer
- M6 Takedown Rifle Comparison to the Springfield Scout
- Safe Release of Non Target Species
- French Press Testing and Protyping
- Simple Camp and a Test of the Wildward Lavu
- Pocket Stove Comparison