Fire School Part 2 Bow Drill Lessons
Description
http://www.thepathfinderstore.com
Dave Canterbury, David Canterbury, The Pathfinder School,Bush Craft ,Survival skills, Historical Lore, Primitive Skills, Archery, Hunting, Trapping, Fishing, Navigation, Knives, Axes, Fire, Water, Shelter, Search and Rescue
Tags: Bushcraft,Survival,David Canterbury,Dave Canterbury,Pathfinder,The Pathfinder School,Archery,Hunting,Fishing,Camping,Primitive Skills,Fire,Water,Shelter,Navigation,First Aid,Search and Rescue,Signaling,Prepper,Preparedness,Self Reliance,Survivability,The 10 C's,Knives,Axes,Saws,Bow Drill,Ferrocerium Rod,Ferro Rod,Tarp,Hammock,Canteen,Cooking,Longhunter,Trapping
Video Transcription
[Music]
[Music]
okay so the next step is to make our heart board again we want this thing bigger around diameter than our spindle I've got my spindle in my pocket so it doesn't get wet so let's cut this off again a bahco laplander but make a lot shorter work of this then multi-tool saw for sure okay start off with a piece about that big I hope it's big enough in diameter remember that we can always make our spindle a little bit smaller if we need to as far as the diameter that spindle goes now I'm looking at sorry just saying I'm seeing it looks a little bit pithy right there it's been dead for a while you can see as I'm smacking with this one it's sheared off is that going to make a major difference maybe yes maybe no cutting - with my knife see what it feels like it's not too bad it's not too bad now let's cut this other side off
what I'm hoping to end up with here is a board that is close to a half an inch thick and I'm just going to see this basically into a rectangle about a half an inch thick and about this long and I'm going to flatten it out really good and about the finished thickness I want is about this right here and you can see that's about the thickness of my thumbnail and that's what I'd like to end up with for a finished thickness once I've carved this down [Music]
okay for our bow we just got another branch of that tulip poplar about the length of my armpit to my palm pretty straight branch this doesn't have to be above the difference is I'll have to run my spindle through the outside of the string instead of the inside of the string
I put the spend on the inside of the string without the curve I'm going to have friction along the linear side of this bow and I don't want that so I have to put the spindle to the outside of the string so destroying is in between here in the spindle if I had a curved piece of wood I could go ahead put it to the inside and it wouldn't matter but I'm trying to use what we collected and not worry too much about going out looking for a great bow and all that stuff so I just use one of these same tulip poplar branches pop the bark off of it I cut a notch in the back here notching the front to tie the bank line to real simple procedure of cutting a log-cabin notch and a quick stake notch or a seven notch here and that's where my string is going to run and hold and I should be ready to go with that okay so to attach our string to our bow pretty simple process I'm just going to take one into this number 36 Bank line this is tarred mariners line there's a couple place you can find this on the internet most of the places you buy this is not going to be tarred properly stuff they carry at Walmart does not have tar on any more tarred line has been a standard since the early days of mariners a tarred hemp rope all the time this is a nylon tarred line we sell this on our website and buy it
sometimes at Bass Pro Shops are generally out of stock on it but you can buy it there now I'm just going to come in here and I'm going to put a very simple bowline knot in here that's big enough to fit over the diameter of the front of my bow and the reason I'm doing that and because that's going to sit in this notch here then I'll pull it back here and I'll wrap it inside now I'm going to come back here I'm going to come around to that seven knots that I created and I'm just going to come in here and pull this down through here just like that to create a half hitch keep it on top just like this pull it back against itself so I've got this line straight across here it doesn't have to be real tight at this point because remember I've still got to be able to load my spindle in here I've got to give myself a little bit of slack then all I need to do is wrap it around here a couple of times and I can finish this back here on the handle with a clove hitch so I can come around here and wrap it and on the last wrap I want to make sure that I have an X to go through just like if I were lashing I want to go through that X with my tag so that I have that clove hitch style knot and it's not going to come undone on me [Music]
it does tags through there and I'll be alright there we go just like that so you've got that X right there you've got that line coming through it then you can dress that up down to the bottom like this and then just kind of tighten that down and it'll hold just fine like I said you want this thing here to be pretty straight down your bow from this back notch down to where your bowline knot is you've got to have a little bit of slack in there just going to stretch a little bit on you at first so if you got a little slack it's okay now let's talk about loading the spindle okay once we have our string on our bow now we can face the bow away from us just like this take our spindle and load it up through with the end that we went down going up right now so this is the end that's going to go down on the fire board this thing that's going to go up into the bearing block or handle so we load the fire board end up and we twist it down just like this so when we twist it pops into the string just like this and that's the way it's going to be running it's going to run on the outside like this of the bow so it's going to travel the length of that bow just like this on the outside that's not going to create any friction whatsoever between our bow and our spindle we don't want any friction anywhere except on the board that's going to alleviate that and it will give us the whole length of this bow all the way down to this knot and all the way down to the handle end that that spindle can spin freely just like this okay now let's talk about our hand holder bearing block okay the bearing block the bearing block is the most difficult thing to reproduce from natural material and make it effective that's why you see a lot of guys carrying things like bone or antler or glass or a piece of metal or they have a divot cut into our knife handle all of those things are materials that don't wear away very easily wood burns up and when that divot gets deep inside your hand hold it begins to rub on the shoulders of your spindle and that causes friction in your top block or your handled which reduces the friction in the bottom it also makes it harder to operate the bow which means it takes more energy to produce the same effect what I've got here is I've got a piece of green cherry that's about the size of my fist and about two inches in diameter and I'm just going to take and baton a section off of this piece of cherry just like this
if I've got a choice if I have a choice when I do this I'm going to trim off the side that has the most growth rings because it will be the most dense on that side if it has stacked growth rings on that side tight growth rings I shouldn't say the most I should say the tightest growth rings are the least growth rings you can see if you look at this piece of wood the growth rings are out here and they're spread apart from the center that means this area of the tree was facing south toward the Sun so this is the more northern side of the tree and it's going to be dense and harder there because there's going to be less SAP wood and more heartwood kind of technical but it'll be a harder piece of wood in general the fact it's green is going to make it burn slower and that's important and I can debark this if I want to make it pretty or I can just leave it if I'm trying to make a quick set so now I have to cut a couple of divots or starters they need to cut one in my top block and then you cut one in my fire board or my hearth board this one needs to be pretty much centered on the wood here and here and I'm just going to take my knife and pretty much drill that in there keeping my knife blade away from me all the time so if I'm going to cut I'm going to cut with a knife blade away from me so that if it slips it slips down into here and not into my hand I'll turn this thing over and do the other side
if you've got a good hard piece of wood you're not going to have to cut that divot real real deep and it will wear in there okay when you first start to use it anyway this is a good dense piece of wood I can tell by that thick fuzz it's creating right there where the grain of the wood is this has got good green heavy green in it I want that for my bearing block I don't want that for my hearth board my spindle once I get that give it put in there I can just kind of rotate my spindle in here a little bit and clean it out and I want that to ride nice and smooth right there if this burns in too deep it's going to be on these shoulders and then I'm going to be getting friction in the top which is what I want to avoid that's why when he's a green hardwood for this top so it doesn't burn and if it does burn hopefully it will polish and it won't continue to Waller out the whole bigger and bigger but hopefully I'm only going to have to use this one time get my coal I've got a good fire lane I'm ready to rock and then I can prepare for the next fire in my progression of fire we'll talk about that in the next episode so we're going to marry those up a little bit and then we're going to go over here to our hearth boards and we're going to need to figure out where we want to put our spindle and hearth board to turn our coal remember that you're going to have to cut a v-notch in this hearth board so you have a place for the coal to go for the dust to collect to make that colt so you're going to back up a little bit and I'm going to back clear up this backside here figure right here in this area that I haven't carved off that's where that hole is going to go and I'm going to do the same thing here I'm going to dish that thing out just like this keeping the knife away from me and just cutting a divot in there just like that and all I need is a spot in there deep enough like that spindle will rest in there because the deeper I cut this now the less fireboard I'm going to have when the time comes to make my Ember and that's important to understand as well with a thin fire board you may only get one shot before you've got to change this and go somewhere else and again I'm going to do the same thing I'm going to take my spindle and put it on here and I'm going to turn it a little bit on a solid surface and kind of marry it up with my arm a little my arm strength a little bit here so that when I put it in there it marries up quickly it doesn't slip and jump around on so you can see I put that divot in there now now I'm ready to what's called burn it in which means I'm going to spin the spindle on the board to create a hot spot right there and burn it into the board and that will tell me if it turns the right color of black that this set is probably viable so we have our bow we have our top block or a bearing block we have our spindle and we have our hearth board this is tulip poplar soft wood doesn't matter what species soft wood willow will work Caesar will work white pine or pine will work if you use the SAP wood and not the heartwood spindle is made from the same material the bearing block is a hard piece of green hardwood we took another tulip poplar branch and we made our bow and again this is a straight bow so our spindle has to ride on the outside of the string not the inside all right so now we're going to get ready to burn this in I've got a piece of wood leaned up against my board so that I can put my foot on that board and not put moisture into the board right now I'm just trying to see that this thing is going to ride smoothly I've got to keep this bow level as I run just like that now what I'm looking at is I'm looking at two things I'm looking at my bearing block to make sure this not expanding too much I'm looking at the top to see how about it's starting to shoulder out and I'm looking for color here and color here before I decide I'm going to go after this for real I've got a couple things to consider I tightened up my bowstring just to make sure it was good and tight my spindle looks okay but I'm going to need to dress this front end I'm also going to need to cut my V notch and this looks like it's fine so I have to worry about that these two things need to be worked out then I'm going to need something to catch my coal and I can use anything like this flat piece of wood for that to catch my coal on top of this is my board to make sure that I don't put moisture into the rest of my board in case I have to use it later I put my foot on this we're going to need a V notch here ready to dress this top point and then we should be ready to rock and roll and try to get a coal first of all let's address this we're just going to come in here and knock that shoulder off at the top I don't want to knock that burnt area off because as it's burning it's hardening so I just want to come in below that and create a new angle there that goes up to that point but doesn't knock it off
just a little control right there we'll be fine just like that again remember preparation of the material is the key to the success here okay that should be alright now we can save all these little shavings for a fire light but we're not going to talk about that right now so we won't worry about it now we need to cut our v-notch our v-notch needs to come in at an angle across here and across here a lot of the notch size and width have to do with the material that you're using if you're using a lighter material a softer material you can generally get away with a smaller notch but you're going to need more width on that knotch
especially with a poplar type material because it comes out in fibers your charcoal will be creating fibers that will be kind of long and stringy they have to have a lot of oxygen flow to get a good Ember so what I like to do with my fire boards when I'm using poplar is I'll come in here and I'll cut a v-notch just like this coming in from at an angle on both sides about a quarter of an inch wide the front tapering to and eight and I want that notch to pretty much end right at the edge of my burn in so when I pop all that stuff out of there and go to clean this up of my knife you can see that that notch is right at the edge of where I burned that in coming in there out of V I've got to make sure that I've got an area that doesn't dust can spill over so I'm going to clean that out just a little bit and give it a little bit of a ramp right there on the bottom side I want to make sure I'm getting plenty of oxygen flow so what I'll generally do is I'll come in here on the bottom side and I'll carve in just a little bit on an angle here and here to create a little bit of a V underneath there right here and here so that oxygen can flow in from the bottom and get to my ember and I think that's all important stuff and all of those little variables like that there's little subtle nuances are things that can get you messed up remember you only want to have to do this one time if you can help it so the better preparation you do to begin with the better off you're going to be that board is not very thick you may only have one bite at the Apple here now that we've got those things straightened out we're ready to try to get it done so we're going to set our board here and put our notch right here on top of our couch set our foot placement right here as close as we can get to our hole without rubbing our foot with the spindle on the bow we're going to get the bow loaded up just exactly like we talked about remembering that we tighten our string that's probably going to be a little harder to load the bow this time that was the last time I like to get mine in the middle if I can we're pretty close to the center we'll get ourself on here and get comfortable we've got to make sure that we get this buried into our shin then we can use our shin and lean our weight forward to get downward pressure putting our chest directly over the top of the spindle and this is the form that we want
I'm Dave Canterbury pathfinder school i thank you guys for joining me out here today for another video I thank you for all your support and comments I thank you for supporting our business our school all of my instructors affiliate sponsors and Friends and we're back another video as soon as we can thanks guys
[Music]
you
About the Author
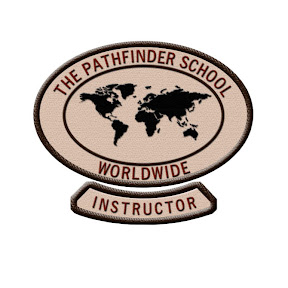
wildernessoutfitters
From the lore of bushcraft to all things related to self-sustainability, the Pathfinder vision is to pass on the knowledge of outdoor self-reliance. Providing basic to advanced self-reliance training and survival gear, our goal is to offer both practical knowledge and survival gear that will stand the test of time. From emergency preparedness to sustainability, the Pathfinder way is to share and educate.
Here you can explore the world of survival knives, survival kits and simple tips on outdoor self-reliance. We are always learning and enjoy passing on the knowledge we acquire.
There is no substitute for having a plan in the event of the unexpected.
More articles from this author
- Black Drawing Salve
- Pace Counting and Dead Reckoning
- Bullet Proof Bushcraft on a Budget Long Guns
- The Witchery of Archery Part 3 Arrows and Arrow Flight
- Sling Bow Final Modification How To
- Journal of the Yurt 29 Q&A
- African Bird Trap
- Journal of the Yurt 37 Stock and Trade
- A Common Man Sustainability Cross Bow
- Modular Packing Discussion
- Rendering Birch Oil, As taught at the PF Pioneer Class by Joe Kellam
- Modern Trapping Series Part 41 Raccoon caught in a False Drain Set.wmv
- Shooting the Recurve Bow (Beginners) with Iris Canterbury.wmv
- Journal of the Yurt 2
- Journal of the Yurt 7
- NINJA SHELTER
- Spring pole Bowdrill Ember
- Cooking Tips and Quick Treats (Garlic Rice and Smoked Sausage)
- 5 Navigation Techniques Every Woodsman Should Know
- Building a Discount Bushcraft Kit Part 5 (Wool Blankets)
- Journal of the Yurt 38 A day in the Life
- Trail Tarp Set up Options Part 1
- Cast Iron Cooking Part 2 Pork Mash Cassarole
- Creating a Fire with Aspen Punk wood and the Sun
- Modern Trapping Series Part 44 Skinning a Mink
- Shoes a Simple Improvised Pattern
- Pathfinder Advanced Class Florida Everglades
- Blacksmithing Part 14 Making Nails
- Bow Saws, a Common Man Bush Tool
- Bow Fishing Equipment Explained
- Kid Testing of the Lightning Strike Fire System
- The Osage Bow Part 6 (Draw Wt and Shooting)
- Modern Camp Set up
- Utilizing Resources Tallow Making Lye Soap
- Apache Foot Trap
- H&R 12 GA Buttstock Mods
- The Quickie Poachers Camp.wmv
- Blacksmithing Part 7 Making Cooking Irons
- Tablet Weaving
- 21st Century Longhunter Processing Tinder Fungus for Use
- Neolithic and Ancient Roman Fire Methods
- Eastern Woodland Trees and their Uses 1
- Using a Compass to take a Visual Bearing
- Journal of the Yurt 24
- Journal of the Yurt 36 12GA R&D
- Kit Mentality the Basics
- Blacksmithing Part 11 Forging a Knife Step 1.wmv
- Beginners Knife Safety Part 1
- Commercial: Dave Canterbury "Makes fire with his beard"
- Modern Trapping Series Part 23 Skinning the Catch
- Starting your net
- Wood Craft on a Budget Part 6 Cookware 2
- Jam Knots 3 that do it all
- Slingshot Forging
- Pathfinder Product Review 11 Flint Knapping Tools
- On the Waters Edge Part 4 Sling Spear
- Pathfinder Product Review #3 The Emergency Shelter Kit
- Pathfinder Product Review #5 The Nessmuk Hand Axe
- Throwing a Knife
- Packable Draw Knife and a Simple Vise for the Woodland Projects
- Bushcraft Kit Shot Show Intro
- Shooting Vanes from a Traditional Bow
- Journal of the Yurt 1
- Testing a Common Man's Survival Bow.wmv
- Diary of the Tipi 4 Primitive Archery Repair Kit.wmv
- ROKON Series Intro
- Cornish Hen Cassarole in an Aluminum Dutch Oven
- Super Shelter Modified for the Eastern Woodlands Part 1
- Improvised Zip Lock Compass.wmv
- 21st Century Longhunter The Versatile #110 Conibear
- Journal of the Yurt 31 Folders and MT's
- Condor Greenland Axe Pathfinder Product Review #12
- Packing for a Trip the 3 C's Concept
- How to get your pattern for a wool blanket shirt
- Brain Tanning Hair On Part 1
- SlingBow DVD
- Fleshing hides: The easy way
- Butcher Knives a Frontier Standard.wmv
- Reviewing a Survival Shotgun Set up.wmv
- Long Guns, Canoe Guns&Testing the Wax Slug 12 GA Load
- Stronghold Haywire Klamper Projects
- Asian Monitor Trap
- NO FAK First Aid Kit
- Journal of the Yurt 6
- Walnut Blueing an H&R 12GA
- Modern Trapping Part 4 Foot Hold Traps
- Mora Camping Axe "Dont save it for the wimpy wood!"
- Quick Run Down of the Final 5 C's of the 10 PC Kit
- 1751 Belt Ax Kit Project Part 2
- Fire Tube
- Journal of the Yurt 28 Spices
- Journal of the Yurt 26 My Shooting Bag
- Utilizing Resources, Glass Arrow Heads
- Iris Intro1.wmv
- PF Cook System for 2017
- Primal Gear Unlimited Compact Folding Survival Bow
- Corn Meal Mush
- Journal of the Yurt 9
- Emergency Fire-Foul Weather
- Boot Care and Boot discussion
- Pathfinder Pocket Hunting System Promo
- Auger Adapter DIY
- Making a Scrap Yard Folding Knife Part 1
- Bug Dope
- Tools and Honing Discussion
- Pine Sap Accelerant
- Journal of the Yurt 5
- On The Waters Edge Part 8 Fileting a Fish
- American Mod to the Asian Bird Trap Snare
- Modern Trapping Series Part 26 Prepping the hide for Tanning
- Modifying Brass Shotgun Shells to accept the 209 Primer.wmv
- Survival Bows (Shaping and Floor Tillering the Stave)
- Woodcrafters Bench Part 4 Spoon Mule Attachment
- Pathfinder School Self Reliance Projects Update 2
- Char Cloth and Ignition Sources
- Wool Blankets Winter Camping Part 2
- Making Woodland Furniture The Dove Tail Joint Lash
- Fire School Part 9 Bowdrill Ember from Horsehoof Fungus
- American Yurt at the Pathfinder School Intro
- Journal of the Yurt 3 Making Hard Tack
- Cast Iron Cooking Part 1 Spicey Rice Dish
- Pathfinder Nessmuk Trail Tarp by Duluth Pack Co
- Take Down Bucksaw Project Wood Craft on a Budget Part 19
- 5 Min Shelter Option Double Wedge
- Swing Arm Cook System from Natural Materials
- Stump Anvil Improvements The Clave
- Throwing the Tomahawk
- Making Corn Flour Cereal.wmv
- Diary of the Tipi 8 Making Gourd Containers Part 1
- Starting Fire with Steel Wool and Ferro Rod
- NEW Gen 2 Small Bushpot
- Exploring the Whelen Lean Part 2
- Converting Your Percussion Cap to 209 SG Primer Ignition (Mag Spark)
- Over Night Scout
- Pathfinder Cribs The Pathfinder Yurt
- Survivability vs Sustainability.wmv
- Self Feeding Fire Part 1 Basic Bushcraft
- Simple Machines 3 Rope Spinner
- Bullet Proof Bushcraft on a Budget Cover
- Wood Craft on a Budget Part 10 Refurbishing Old Tools1
- Survival Basic Series DVD Part 5
- Pathfinder Product Review #14 New Mora Knives
- Addressing Snake Bites
- Top 5 Medicinal and Useful Plants of the Eastern Woodlands Part 1.wmv
- Poplar Dough Bowl Part 1
- Simple Camping Plow Points Part 1
- Clothing for the Cold
- Frontier Fire Methods 2.wmv
- Fishing Kit-Improvments Testing
- Modern Trapping Part 5 Intro to Snares and Snaring
- Equipment List Discussion for Pathfinder Basics
- Processing Small Game Pheasant
- Evolution of Survival
- Black Smithing Part 1 Making a quick Fire Striker from a File
- Modern Trapping Series Part 33 Using PVC in Sets
- Journal of the Yurt 8
- Journal of the Yurt 4
- Introducing the Pathfinder Scout Hawk
- Mini Inferno NEW PRODUCT
- The Common Man's Last Shot- Pocket Pistol
- Scout about and Bacon out
- Simple Bucket Pack Modification
- Navigation by Terrain Feature Association Part 1
- A Quick Bait holder for Catfishing
- Building Traps without Tools
- Journal of the Yurt 27 Securing More Meat
- The Witchery of Archery Remake Part 1 The Two Tracks Long Walker
- Pocket Hunter A Comprehensive Look at Design and Use
- Practicing Fire Methods 1
- Cabin Fever Part 20 Preserving Game meat in Winter
- Cast iron Cooking Part 3 Deep Fried Bass Filets
- Journal of the Yurt 50 Forging a Cookset.wmv
- Journal of the Yurt 23
- Tarp Setups and Research for System Development
- 5x5 Bushfit Kit
- A Review of 3 Pocket Tools
- Bushcraft Tools Fire Piston Test
- Sunfish Lunch'en
- Knapping a Quick Stone Point from a Flake.wmv
- PVC Bait stick Trap
- Bullet Proof Bushcraft on a Budget Containers
- Cooking Squirrel and Rice
- The Spider Shelter Part 3 Finishing up and heating it up!
- Fire School Part 14 Rub Cloth
- Journal of the Yurt 20
- Journal of the Yurt 18
- Journal of the Yurt 41 Pack Goat
- Materia Medica Yarrow 3
- Building a Discount Bushcraft Kit Part 4 (Take Down BuckSaw for Ten Dollars)
- 5 Tools and Functions to manipulate Wood
- Brain Tanning Hair On Part 3
- Grand Opening Invite
- Common Man Self Reliance Bow #2
- Cabin Fever Part 29 ATV Scouting and my Kit 1
- 21st Century Longhunter Mentality and the 5C's
- NEW Council Tool Woodcraft Pack Axe
- 2 Dollar Knife and Sheath Project Part 1
- Reproducing an Antique Draw Shave Part 1
- Basic Multi Use Knots
- New Sling Bow
- Quick Fishing Kit from Common Materials
- Asian Trail Spring Trap
- Natural Cordage Part 2 The Process of Reverse Wrap 2 Ply Cordage
- Ignition Sources, My Belt Kit
- Bushcraft Kitchen Part 1
- Dressing for Cold Weather.wmv
- 5 Minutes to Better Bushcraft Building a Friction Fire Ember
- Torture Test of a Savotta Pack
- Wisdom of the Wall Tent Part 4 Junk on the Bunk
- Full Circle
- Carving a Noggen
- Canvas Ship Hammocks and Weaving a Clew
- Traditional Japanese Water Stone Sharpening
- 5 Minutes to Better Bushcraft Dakota Fire Hole
- Blacksmithing Part 39 Making a Portable Pit Forge
- Dream Hammock System
- Starting Fire with a Compass K&R Alpine
- 5 Wooden Tools
- New Jon Pack Woodsman’s Bed Sleeve
- 5 Minutes to Better Bushcraft proofing and Reproofing
- Mushroom and Plant walk in Sweden
- Mora Adventure 2018 Short clip
- 5 Min Fire and Shelter Conversion.wmv
- Trap Comparison and Thought Process, Modern Trapping Series Part 43
- Simple Fencing
- Rendering and using Raccoon Fat
- Viking research
- Hickory Resources
- Bushpot Chicken and Dumplings
- Woodcrafters Bench Part 2
- 21st Century Longhunter The Oil Cloth Watch Coat
- Game Hooks
- Bill Hawk
- Pathfinder Product Review The JW Trekker
- Basic Camp Overnighter Part 3
- Next Fire Mentality
- 50 Dollar Tool Kit for Green Woodworking
- Pathfinder Product Review #6 The Duluth Pack PF Haversack.wmv
- Steam Bending Wood
- Water Filter Comparison
- Sling Bow (Bow Fishing Mod How To)
- Survival Bow Making(Making a Bow String)
- Making the Packable Draw Knife
- Making A Common Man's Broadhead
- Building a Discount Bushcraft Kit Part 7 (The Blanket Pack)
- Exploring the Whelen Lean
- Blacksmithing on a Budget
- Building a Discount Bushcraft Kit Part 6 (Cheap Small Game Snares)
- Materia Medica INFUSIONS The Woodsman's Expectorant 22
- Fire School Part 8 No Container Char
- Norlund Axes
- Using Flex Seal on a Canvas Pack
- Pathfinder Product review #4 The Pathfinder Trade Knife.wmv
- Knives and Processing Wood
- Axes and Hatchets Wood Craft on a budget Part 15
- Opinel Safety Mod and Penny Knives
- The M44 Mosin Nagant, A Common Man Rifle
- Simple Box Traps Live Rabbit Box
- Grass Thatching
- Frontier Fire Seminar from the Camping and Woodcraft Class
- Rocky Woodland Forge's Woodcraft Tool Kit
- Stack Pack by Short Lane Arms
- Restoring A Scrap Yard Wood Stove
- Diary of the Tipi 10 I love Fire! my EDC.wmv
- PFODJ Ep4 18th Century Woodsman Hunters Camp
- Camp Cookery Baked Rabbit
- Survival Pro Tips 1 Making Fire with an Empty Bic
- Simple Box Traps Mink Box
- Meat Processing Tools
- Fire School Part 7 Strikers, Scapers, and Smooth Strokers
- Tools and Wood Processing
- Medicinal Trees of the Eastern Woodlands 1.wmv
- Hush Puppies on the trail
- Blacksmithing Part 17 Scrap Yard Pick'en
- Hammock Chat
- Knife Making , Material Reduction Knife Start to Finish Part 1
- Belt Pouch EDC
- Useful and Medicinal Trees of the Eastern Woodlands 3
- Using the H&R 12GA for a Muzzeloader
- Ultimate Survival Bows
- Journal of the Yurt 11 Hygiene
- Journal of the Yurt 10 Visit with Jeremy Janey PF School Intructor
- On the Waters Edge 13 Day 2 Mohawk Canoe
- Hygiene from Fire
- Wisdom from the Wall Tent Part 1
- Making a Common Man Limb Quiver for Hunting
- Coyote Consuming the Harvest
- Knife Care in the Field
- Hobo Stew and Corn Bread
- Bushpot Jambalaya and Hushpuppies
- Useful and Medicinal Trees of the Eastern Woodlands 4
- Basic Camp Overnighter Part 1
- Axe Care Made Simple
- Bulletproof Bushcraft on a Budget Part 1
- Snares The Ugly Truth Modern Trapping Part 57
- Kit mentality Useage vs Investment
- Blacksmithing Part 36 The Wind Tunnel Forge
- New Primitive Technologies Discussion
- Blacksmithing Part 13 Forging a Knife Step 3 Heat Treat and Testing
- Fire Lay The Proper Construction and Ignition after a Night of Rain
- Fire Arms Combination for Long Term Sustainability
- Modern Trapping Part 29 Foothold Pocket Set
- Basic Knife Handling and Bush Craft Notches Part 1
- Blacksmithing Part 18 Making a Brake Drum Forge
- Bucking with a HB Cruiser Ax Wood Craft on a Budget Part 16
- Journal of the Yurt 12
- Reloading 12GA with (Pyrodex) Black Powder in the Field
- Skinning a Raccoon with Rope,Modern Trapping Part 32
- The Witchery of Archery Part 2 The Basics
- Honeysuckle resources and a quick update
- Survival Bows (Collecting the Stave, Improvised Draw Knife)
- Skinning a squirrel for a usable hide
- Blacksmithing Part 12 Forging a Knife Step 2 Material Reduction
- Evolution of the 10 C's Part 1
- Shelter Basic Tarp Setups 1
- Fire The Basic Class Presentation
- Mora Garberg Full Tang Discussion and Review
- NEW 2 1 Ltr Bushpot and 64 Oz Bottle
- Shelter Basic Tarp Setups and an E Fire 2
- Mora Dangler made simple
- Simple Machine Woodland Hoist
- Coyote It's whats for Lunch
- Shelter Basic Tarp Setups 3
- A Woodsmans Apothocary
- Wooden Pulleys and Lifting
- Deer Heart and Pepper Gravy Camp Cooking
- Simple Woodcraft Aids
- Overnight Pack Out
- Fire School Part 1 Bow Drill Lessons
- Collapsible Cast Iron Skillet DIY
- Quick Upload Extracting Pine Tar from Fat Wood
- Blacksmithing Part 15 Making tools for Spoons and Ladles
- Forging and making a Primitive Adze
- Trapping Season Prep and Primer Discussion
- Top 10 Non Firearm Meat Gathering Tools
- Haversack Kit
- Pathfinder Advanced Class 1_7_2010 MA, USA.wmv
- Squirrel Hunt with a Flintlock
- Best Medium Game Snare Modified figure 4 Trigger
- Council Tool Hudson Bay Camp Axe
- Gig Discussion and Hunt with Weapon Vision Spear Cam
- 2 Dollar Knife and Sheath Project Part 2
- Go Ruck Rucker Review and Kit layout
- Bushcraft Breakfast Bannock
- On the Waters Edge Part 1 Compact Fishing Rods and Systems
- Toggle Trigger Fishing Variation
- Swiss Army Knife easy Ember , Fire Tips and Tricks
- Roycroft Pack Frame Part 3 Using Shelter Components
- Blacksmithing Part 4 Rounding and Drawing steel to make a Trap Stake
- Fire School Part 13 Ferro Rod Tips
- Tension Bending Pack Boards
- 12GA Shell Bag Contents and Discussion
- Bushpot Convection Oven
- Stretcher Bed Setup
- Pathfinder Folding Skillet
- Making Sweet Corn Bread Drop Biscuits
- Diary of the Tipi 2 Making Hide Glue.wmv
- Otzi s Knife Sheath
- Pathfinder Basic Survival Class Video Diary
- A Common Man's Grease Lamp
- Canterbury Camp Kitchen
- Rokon Winter Packout
- Blacksmith a Squirrel Cooker explained Part 47
- Leather Knife Scales
- M6 Scout Update Review
- The Osage Bow Part 1
- Basic Carving Kit
- Snow Shoes JMHO
- Simplicity
- Final Product Modified Kephart Bedroll by Duluth Pack
- Swedish Lap Vise
- Forging a Custom Carving Axe with Liam Hoffman Part 1
- Toggles The Woodsmans Friend
- Tarp Setups the Foresters Tent and the 4 W's
- Making a Blade Bowl Adze
- The osage Bow Part 4
- Taking a Bearing from your Map made easy
- Journal of the Yurt 43 Stock and Trade Part 2
- Survival JMHO
- Simple Camping Improved Pot Crane System
- Batoning Wood with your Knife
- Improving the Wax Slug Load for 12 GA and Black Powder Equivelant
- Modern Trapping Part 7 Bedding Foot Hold Traps
- Wisdom of the Wall Tent Part 3 Camp Tool Box
- Useful and Medicinal Trees of the Eastern Woodlands 5
- Pine Crate Tool Chest
- Pathfinder School Basic Class Equipment List Rundown
- Diary of the Tipi 11 Care for a Smoothbore Flintlock.wmv
- Baking with a Plank and a Bushpot
- Wood Craft on a Budget Part 3 Sheath Knives Continued
- Building a Discount Bushcraft Kit Part 3 (Food)
- Triple Barrel Shotgun PF Edition Intro
- Maul a good Learning Project
- Meat Preservation Concerns and Setting Snares
- PFODJ Ep 11 Wet Weather Fire Segment
- The Small Common Man Trapping Kit
- Useful and Medicinal Trees of the Eastern Woodlands 2
- Simple Camping Connection Knots 3
- Pathfinder Outdoor Journal Ep1 FULL HD Episode
- Quick Review of the ILBE USMC Assault Pack and Sealine Insert Bag
- Simple Blade Grinding Jig
- Diary of the Tipi 12 Working with Natural Dyes Part 1.wmv
- PF SS Kettle
- Jeff White Bush Knife and a Wet wood Fire
- My Back Yard
- Knives JMHO
- Iris Intro Video Part 2.wmv
- Thanks for Play'en, Bobcat in an MB 450 Released
- Kit Mentality Updates
- Bullet Proof Bushcraft on a Budget PVC Pack Frame
- The Osage Bow Part 5
- The Mocotaugan
- Pathfinder Knife Shop Introduction
- Deadliest Small Game Primitive Trap
- Saami Repair Kit
- Building a Discount Bushcraft Kit
- Stone and Bone (Utilizing Resources) Part 1
- No Map No Problem Part 2
- Arrow Making for the Common Man
- The Wish Bone Trigger Snare New
- Making a quick Spring Lathe
- Using the Slingshot to Hunt Bigger Game
- Bark Basket Part 1
- Scout Camp Common Man Black Powder Setup
- Collecting Back Sinew and Some Meat from a Roadkilled Deer
- Dakota Fire Hole Proper Construction and Use
- Artifact Quality Leather Work
- Bucket Making White Coopering
- PFODJ Ep 5 Axe Tomahawk Segment
- Reverse Figure 4 Dead fall Trigger
- Fire and Bushpots
- Shooting Shot from a 50 Cal BP Rifle
- Tarp Setups Modifed Plow Point
- 50 Cal Blue Ridge Mountain Flint Lock
- Remington Shotgun Model 1889 Double Barrel
- Shrink Pot 1
- Reflector Oven Bread
- Preping the Sling Bow for a Big Game Hunt
- Modern Trapping Coon in Beaver set
- Brimstone Matches and Next Fire Mentality
- No Map No Problem Part 3 Height and Distance
- Saw Maintenance 2 Wood Craft on a Budget Part 14
- SS Canteen Available NOW!~
- Identifiying Flint Chert and other Sparking Rocks
- Trap Sets The Step Down Set Modern Trapping Series Part 48
- Axe Selection and Use
- The Osage Bow Part 2
- Tomahawk from a Rasp Blacksmithing Part 46
- Making Pemmican
- Moonshine Why Carry
- Trailblazer Deliverables Basic Compass Use
- Making the Flemish Bow String in the Bush Part 2
- Simple Camping Hammock use with Wool Blankets
- Forging a Hook Knife
- Finishing a New Old Stock Mora 311
- Survival Basic Series DVD Part 1
- Sharpening an Axe with a Hardware Store Grind
- Putting a Handle on a Mora Blade Blank
- Simple Machine DIY Spring Hammer
- Forging a Tomahawk from a Rasp
- Feathersticks or Shavings
- 21st Century Longhunter Series Combustion
- Fire School Part 15 Pump Drill Fire,Learning the process
- Seneca Pack Frame
- Ever thought about this? Fire Tricks
- Sustainability Long Term,Modern Trapping Series Part 42
- Blacksmithing Part 2 The Folding Small Game Gambrel
- Double Bit Axes Wood Craft on a Budget Part 17
- Sleeping Gear JMHO
- Knapping Arrowheads From Glass Part 1
- Mora Bushcraft Pathfinder
- Making a Cook Tripod with a Chain
- One Match Fire for BSA Bushcraft
- Rope Bed Construction
- The Spider Shelter Part 4, Simple Improvments
- Quick and Easy Tensioner Knot for your Tarp Lines.wmv
- 10 Simple Knife Projects Part 1
- Lighting a Candle with Flint and Steel
- Winter Pack Out
- Utilizing Resources (Making Venison Jerky) Part 2
- Natural Cordage Part 1 Harvesting and Processing Materials
- Asian Bird Trap Laos
- Vines and Withies
- Woodman's Pal
- Five Tool Rule
- Prefered Clothing and Layering for the Woods
- Simple Shadow Navigation Part 1
- Brain Tanning Hair On Part 2
- R&D of the Kephart Bedroll by Dave Canterbury and Duluth Pack
- Light Weight Scouting Pack Set up
- Trapline Diary Part 1 Coon Cuffs
- Survival Basic Series DVD Part 2
- Pathfinder Basics Estimating Distance and Pace Count Lecture
- Super Shelter Modified for the Eastern Woodlands Part 2
- FULL TANG MORA Bushcraft Knife
- Beginners Knife Safety Part 2
- Survival Bows (The Tillering Process)
- Blacksmithing Part 6 Common Man Tools and lighting the Forge
- Building a Discount Bushcraft Kit Part 2
- Sloyd Project 1 Fid
- On the Waters Edge, Trekken and Fishen
- Traditional Cold weather Hammocking
- Knife Making, Material Reduction Knife Start to Finish Part 3
- Trapline Journal Coyote in MB450
- Winterizing the Hammock for the Common Man
- Samick Sage Recurve 8pt Buck Kill
- Large Bushpot Intro
- Bucksaw Modifications
- Fatwood Collecting Processing Igniting
- Aussie Wool Blanket
- Assembling a Custom Classic in the Mora Factory
- Traditional Camp Pack weight
- PFODJ Ep 2
- Hook Knife Part 1
- Making a Bushcraft Knife Part 4
- 1908 A&F Cook Grate
- Nordic Pocket Saw
- Making a Bushcraft Knife Part 1
- PFODJ Ep 5 Moved from the Pay Channel
- PFODJ Progression of Meat Source Gathering
- Experiments in Viking Navigation Viking Sun Stone
- Turkey Tail Materia Medica
- Hook Knife Part 2
- Making a Bushcraft Knife Part 3
- Making a Bushcraft Knife Part 2
- Double on Coons
- The Woodsmans Pantry Plus and the Woodland Chef Cook Kit
- Cooking Bannock in the Bush Pot with a Pack Grill Rack
- Fence Line Snares for Coyote
- Forged Scissors Part 2
- Forged Scissors Part 1
- Pathfinder Scout Hammock
- Trappers Cabin Season 2 Part 5 Raccoon Meatloaf
- Trappers Cabin Season 2 Part 2 Firearms
- Trappers Cabin Season 2 Part 7 Fleshing Hides
- WInter Clothing Discussion
- Trappers Cabin Season 2 Part 4 Tail Stripping
- Hammock Chair Hunting Seat
- Trappers Cabin Season 2 Part 1
- Trappers Cabin Season 2 Part 6 Single Shot Maintenance
- Trappers Cabin Season 2 Part 8 Pocket Sets
- Making a Holiday Wreath
- Trappers Cabin Season 2 Part 9 Making Kvass
- Trappers Cabin Season 2 Part 3 Trash Panda
- 110 For Mink
- Trappers Cabin Season 2 Part 13 Wood Stoves
- Morakniv Carbon Steel Garberg
- Trappers Cabin Season 2 Part 14 Releasing a Domestic Animal
- Z Drag with wooden Pulleys
- Trappers Cabin Season 2 Part 12 Log Crossing Set
- Trappers Cabin Season 2 Part 11 Chasing Mink
- Exotac Products and Titan Lighter tips
- Trappers Cabin Season 2 Part 10 Mapping the Creek Bed
- Trappers Cabin Season 2 Part 15
- Trappers Cabin Season 2 Part 16 Last day for a few
- Trappers Cabin Season 2 Part 18 Buck Mink
- Trappers Cabin Season 2 Part 17 Hidden Woodsman Pack
- Bushcrafting a Tarp Clip
- DD Tents
- Neck Knife to Carry or Not to Carry
- Blanket Pin Tripod
- Comprehensive Bow Drill
- Hibiscus Cordage
- The Versatile Marline Spike Hitch
- Hammock Chair Terrapin Outfitters
- Sticky Rice
- Udemy Intro Video
- Conserving the Bic in an emergency
- LL Bean Continental Ruck Sack
- Navigation The X Box Exercise
- Cave Man Conibear Updated
- Limb line Hook Set Device from natural materials
- Solar Embers without Char or Fungus
- Packing up the raised Bed Camp
- Raised Bed Emergency Shelter
- Basket Trap for Crayfish
- Making a Sun Compass
- Ottomani Sun Compass
- Dutchwaregear Chameleon Hammock and Xeon Tarp
- Tulip Poplar Knife Sheath
- Shadow Board Direction Finding
- Dirty by design
- Orienting a Map without a Compass
- Mushroom Foraging Part 2
- 5 Minutes to Better Bushcraft Pot Crane
- Paracord Hammock
- 5 Minutes to Better Bushcraft Quickly Deployable Ridgeline
- 5 Minutes to Better Bushcraft Hanging Camp Gear
- Tighten a Shear Lash Easily
- 5 Minutes to Better Bushcraft Tripod
- 5 Minutes to Better Bushcraft 90 Degree Spine
- Mushroom Foraging
- Broiling Fish with Grill Racks and the SRO Monthly Special
- Exerpt on Basket Weaving at the Bushcraft 101 Class
- 5 Minutes to Better Bushcraft Double Prusik Tensioning System
- Week Long Training Loadout
- Lunch and the Base Camp Cookset
- 5 Minutes to Better Bushcraft 5 Navigational Aids
- 5 Minutes to Better Bushcraft The Angular Advantage
- Last Shadow First Shadow Method
- 5 Minutes to Better Bushcraft Improved Fire Starting
- 5 Minutes to Better Bushcraft Pot Hanger
- Tulip Poplar The Best Eastern Woodland Bushcraft Resource
- 5 Minutes to Better Bushcraft Bark Candle Lantern
- Woodsman's Gear of the 20th Century Part 6
- 5 Minutes to Better Bushcraft The JB Figure 4 Variant
- Mushroom Foraging Part 3
- Woodsman's Gear of the 20th Century Part 3
- 5 Minutes to better Bushcraft other uses for Puffball Mushroom
- Woodsman's Gear of the 20th Century Part 7
- Woodsman's Gear of the 20th Century Part 5
- Fried Puff Ball Mushrooms
- Woodsman's Gear of the 20th Century Part 4
- Using a Strop to Clean, Sharpen, and Hone your Blades
- Woodsman's Gear of the 20th Century Part 1
- Best Survival Deadfall Trigger PDF4
- Woodsman's Gear of the 20th Century Part 2
- Woodsman's Gear of the 20th Century Part 9
- Woodsman's Gear of the 20th Century Part 8
- Woodsmans Gear of the 20th Century Part 10
- Woodsmans Gear of the 20th Century Part 11
- Blood Trailing a Deer
- M6 Takedown Rifle Comparison to the Springfield Scout
- Safe Release of Non Target Species
- French Press Testing and Protyping
- Simple Camp and a Test of the Wildward Lavu
- Pocket Stove Comparison