Bushcraft & Blacksmithing: How To Make a Bushcraft Knife with ALEC STEELE
Description
Learning Bushcraft & Blacksmithing skills and how to make a Bushcraft Knife is a technique I have always been interested in. A Bushcraft Knife is a key tool when learning Bushcraft & Survival Skills. In this episode of TA Outdoors I learn how to make a Bushcraft Knife with YouTube Blacksmith Alec Steele.
Subscribe to ALEC STEELE: https://www.youtube.com/alecsteele
Learning how to make a knife using traditional Blacksmith tools was an incredible experience. We started out with a blank piece of 01 Steel, heated it up in the forge and then used the power hammer to get the material thickness to what we wanted. It was then a case of using the both the flat and round side of the hammer (and anvil) to shape out the point of the knife, paying particular attention to the classic drop-point that Bushcraft Knives tend to have. From here we used the horn of the anvil to create the knife Choil and palm swell.
It was then a case of grinding the knife profile down and removing the oxidised layer to get to the true steel. The hardest part for me was grinding the bevel of the knife. I didn't know how to grind a knife bevel but with Alec's tuition he guided me in the right direction. We then drilled holes for the pins and used Lignum Vitae as the wood handle scales. Lignum Vitae being an incredibly hard and dense wood. One of the hardest trade woods in the world. To finish off I oiled the knife with boiled linseed oil to stabilise the scales and we polished off the bevel on the grinder again.
It was then time for me to test the Bushcraft Knife. I showed how to make feather sticks, batoning with the knife, carving and making notches for pot hangers over the fire to hang various cooking implements. These are core Bushcraft skills and it was a great opportunity for me to see the limits of this survival knife.
Although not quite primitive technology, Blacksmithing is becoming a bit of a lost art. But thanks to Alec Steele's incredible work, he is brining it back! Learning how to forge and make a knife from scratch was one epic experience. Be sure to head over to Alec's channel to see his version of the knife build!
Follow me on Instagram: https://www.instagram.com/taoutdoorofficial/
My Facebook Page:
https://www.facebook.com/totallyawesomeoutdoors
If you wish to send me stuff:
Mike Pullen
PO Box 7466
HOOK
RG27 7NA
Subscribe to our other Fishing YouTube Channel "TAFishing" here: https://www.youtube.com/tafishing
Music:
http://www.epidemicsound.com/
Tags: bushcraft,blacksmithing,making a bushcraft knife,blacksmith,bushcraft knife,alec steele,survival,primitive,primitive technology,survival skills,how to make a knife,forge,anvil,bushcraft skills,shelter,natural shelter,primitive tools,damascus,knife making,engineering,steel,diy,forged in fire
Video Transcription
[Music]
in the previous one Alec help me Forge this steel striker and we managed to get some little bit of a spot so literally we made fire which was pretty exciting this is why I came here guys really you can't see it this is what we came in for a bushcraft knife this is kind of my sketch it's not amazing this is what we're gonna go for and it's gonna teach you some tips as well on what we need to do because really guys I don't know anything about blacksmithing at all other than what I've learnt yesterday should be good fun hope you enjoy it so we've already flattened out earlier Alex helped me maybe some oh one steel which is fairly common in brisk rough knives Alex doing a demo piece alongside my piece here just so he can teach me the basics really of getting that whisper of noise shape
into Margot's
you see what's happening is as we Forge it down it's thickening up turn it sideways hold your peace tell your pocket these level to the animal there we go and then flatten it with your flat side of the hammer [Music]
[Music]
[Music]
it involves
[Music]
[Music]
then we're gonna mark where our next groove is and it's a slightly large diameter now coming over here and we can use the hole like that what we're gonna start doing is we can start dipping in to that nice and swell we want so with that mark we then take the round side of hammer use the round side of the hammer to fall it walk up to that little toy he is just keep aiming right there and don't hit that mark it's got a little bit of a bend in here so you can do is you can lay that across the whole length the anvil and you can very gently collect your hammer across it and get yourself straight [Music]
[Music]
[Music]
well folks here is the bushcraft knife so far as you can see the profile we've got a little bit of a drop point here at the top which we're gonna Alec tells me we're now going to refine on the grinder we've normalized it time for the next stage
[Music]
[Music]
[Applause]
[Music]
we've measured it to the grip in my hand it's much much better originally I did have this kind of belly a little bit bigger but we've ran that down a bit more and it fits a lot more comfortable now so that my knuckle of my forefinger here goes right up to the choil which is what I wanted now you may notice there's some blue stuff on here I like what is it now that is blue duiker much is this blue stuff here it's a dye that you put on metal which that allows you to make a scratch mark you get this wonderful contrast between the scratch and the dark blue so it means that you have an accurate scratch line you can work to for this night especially because we're doing like a Scandinavian grind a Scandi grind
Riaan form that edge is completely centered to it and so we'll take this this is a height gage has a carbide tip we can find the center give it a scribe and now when Mike and I go back into the grinding room and I showed him how to grind this bevel and he grinds his bevel he's gonna be able to grind it to the scribe line keep that edge straight down the hallway we're gonna keep it a little bit thick because after that we drill some holes it's gonna be time to go into the heat treat and when we heat treat it we won that edge to be thick so it's not warping all around and so that all that nice work we did to keep the edge straight isn't isn't wasted by being warped in the heat treat once you know you're in the right angle apply pressure sweet as you come to this this left hand comes out so that you keep that bevel on it and finish like this one smooth motion the whole way through [Music]
[Applause]
[Music]
[Applause]
[Music]
so we put these candy growing on now which alec actually help to refine towards the end there and I have to admit that's probably one of the hardest things that I've experienced from this whole project it's doing the grinding itself a lot harder than it looks we put well Alex put some blue dye come on there and we've marked out holes now where we gonna put the pins in for these scales
so what we're doing at the moment guys we've had a bit of problem with the drill bits I think we've gone through three is I think the matter about three drill bits or so yeah we've gone through three already
and it's actually gone to sharpen them on the grow yeah my sharpen the tiny little drill bit and still they won't cut the material we nailed it overnight and it's just too hard to get cut by the high speed steel drill bits yeah it's gonna be a good knife thing it is once we get some holes that have some pins and be nice to have the scales stay on you heard via would be the sort of machinists look away because we're now doing some good machining sacrilege for putting a carbide end mill and a Jacobs chuck
so you can see guys that alec is now countersunk the holes we've got six holes in there for the handle for the scales we're gonna normalize the knife to harden it and then temper it she's a fine blade chop the forging process all the grinding there are lots of stresses in here it has a very wide grain structure a big grain structure not good having a nice strong blade so the first thing we're gonna do before we harden it and get it hard enough to hold the edge is we're gonna make it strong enough to be able to take that hardening and hold the edge and be strong with normalizing it equalizing the stresses across the whole thing in the Forge here we've got a tube in there so we can get a nice even heat without any hot spots and so in we go the normalizing cycle number one we're gonna heat it up to a critical temperature
so there we go we're just simply going to let that cool down to room temperature
[Music]
now there we go this is the point in time where it's it's big very likely crack so we cross our fingers hope that it doesn't ears we need to select the wood
[Applause]
[Music]
[Applause]
[Laughter]
[Music]
[Laughter]
[Music]
so the knife has been tempered been cooking away in the oven and more gonna do now is go back into the grinding room to get that edge nice and sharp and clean it up a bit [Music]
that's a beauty it's a beauty straight off the belt already sharp it is arm shaving you shot little drop that little drop that Grover make sure we've got plenty of clearance let the glue dry all the way through you know once you're into here then pull up we got this here it's a little screw so that hopefully will stop that spinning but again we want to be careful that we don't bind it so you wanna make sure that when you lift up with this drill you're applying downward pressure so it doesn't come up in an angle if it comes up an angle we're gonna cam it and it'll go end up with a 2,000 rpm spinning blade [Music]
scribe around the edges so we know a little indication where everything is now break it off Joy's the superglue them or super glue her on to the other side
[Applause]
[Music]
[Music]
you see I've taken the small wheel left on the belt grinder and we ground in that I give the 60 grit and a little more surface area for the glutinous here see we're gonna be using at oxy if Hoxie likes Ashley to be a little bit thicker in its bottom and so that helps get it to have a little bit of a thicker bond if also means that we just get a little more surface area just because of the higher grit to recontact onto our epoxy we've also primed the surface of our scales themselves with it again a little 180 grit we think the epoxy is pretty much set why it's been close it needs a little more time but it'll do for now but now we're gonna work on the actual handle itself get it nice and a ganar McCall get it comfortable and then we should be pretty much there absolutely so we're gonna go make some dust [Music]
[Music]
there we go look at that lovely finish we've we've just put a layer of linseed linseed oil just to cover it used pretty much every bit of sandpaper that Alec has here to get that nice finish but that wood has come up so good [Music]
[Music]
guys I hope you enjoyed that build it has been the best project of my life for sure having never done blacksmithing before I had to say Alec it was awesome hey you did fantastically and I'm thrilled that you came it's been a lot of fun see incredible and look at that grind look at that growing we've got you did a lot of it got to take some credit yeah yeah and the grinding is difficult he didn't he did a fantastic job of that yeah definitely the hardest thing I'd say of this whole project towards the grinding so difficult keeping the angle it's not the physical labor part of it it's the actual tiny little movements that you need to do to get that grind but it's been awesome we've left that kind of finish on it you know that sort of raw antique antique yeah this is the scale and looks good and it helps remind me of what it previously looks like don't forget guys you've got a head over to Alex channel for literally everything blacksmithing he's uploading very regularly so make sure you go and hit the sub button and say hi to him from me great well thanks I look forward to see you guys there it's been it's been a pleasure being on your channel thank you but coming here it is so I'm out here in the woods and I've got the knife I've just made with Alex Steel okay give you guys a quick close-up of it and then we're gonna put it to the test and see what it can do so here's the knife itself with the lignum vitae scales one of the hardest woods in the world this one of the hardest trade woods in the world believe it's from the Caribbean really awesome awesome would have never had I never seen the wood like this never certainly on a knife anyway oh one tool steel as we said at the beginning of the video I don't if you saw there when I was grinding it I put in a bit of text because this is this is a very high bevel for a Scandi grind it's almost double what it normally would be that's because I being a first time at Groening I didn't exactly get it perfectly right Alec helped me say it's sort of turned more into what I would call a saber grinds now which is obviously a much higher up you can see that bevel is much higher than a typical Scandinavian growing would be down here about half way and again nice about four four and a half inch blade which I like really ergonomic handle well I did have this belly as I was saying a little bit bigger but actually I'm quite glad it's thinner cuz I can just wrap my fists around it a lot more now I like it when the scales go right up to the choil here the wood handle and I like a good curve from way forefinger just as he would cut one knuckle
grinder there but yeah I'd like to be able to come right up against that so that when I'm feather sticking I've got all the control that I can get you may notice here there's a little divot and that's how Alex actually done that with a file I've never seen it done on a knife before but he makes a good point basically when you're sharpening this against the a whetstone a lot of times especially if you're a beginner in your sharpen knife and a whetstone you can end up cutting in towards the toil and what this helps do is just prevent that because you can dress that edge of the blade right on the bevel there right on the whetstone and you should be fine then to just keep it straight and that way you don't cut in towards the bevel itself so it's one of Alec's tips really for sharpening which I quite like we've left that sort of oxidized type finish on it I quite like that you don't usually see that very often and pushed off nice and it's got six pins in it there to keep the handle in place a lot of knives have sort of two pins two big pins but we've gone for six because we like to be a bit different I would say a few things that I'm wary of if is with the grind or the bevel being so high it's much more likely to fold over where it's a bit more you know where it's the angles a bit tight like that the tip when it hits into it you imagine that's the tip of the knife it can bend and fold over a lot more so you can get a lot more folds or you know sort of not as strong as a typical Scandinavian grind but being a one steel is it should be strong enough to do fattening work and things like that and that's why I wanted the longer knife so that I can hold it like this well away from the blade and you know get bigger pieces of wood that sort of width and still have plenty of room to button down on the tip here so let's put it to the test first test I'm going to start fairly small is this is a bit of silver birch which is grows a lot in the current woodland that Island this is dead this is dead wood it's been dead a while so it should be fairly easy to chop and split nice straight grain on it which should make it easy for Bethany I'm gonna use another piece of birch as a battle to hit the back of the knife that's why I wanted a nice thick whipped at the top here of the steel stick steel because I needed that power when battling so here we go moment of truth when I'm battling I like to use this part of the blade because
not only did this give me a lot more control but it allows me a couple of inches over this side to be able to hit down and get that power typically when you're battening if you're gonna hit the tip of the knife here you can see the back of the handle is gonna kick up like that so you want to be able to lock your hand here and allow for that kick that's gonna happen by pushing down sometimes so sometimes your knife will end up doing this going down the wood which is fine but we'll give it a go and see if it breaks on me I'm gonna start with some light taps just to get the blade in there go check the blade after that we are looking good no folds no flex coming back at me awesome so let's split that piece that split it again a little bit harder now Wow it goes through bone like butter but it's awesome that splits really well turn it towards you guys a bit so you can see this falls open let's try a fatter piece this is this is a bit fatter let's try this piece I've split these with an axe previously check the blade no flex no folds wow that's shocked you know I didn't even stroke that after we took that off the grinder that's not even being strop tall or honed say that's lethal sharp I'm impressed I thought that would fold over if I'm honest being a sort of saber grind I thought that would definitely fold a bit more the sir split a couple more this one that's naughty a F uh-huh yes
I'll show you in a minute above all they stood there's no flex on it at all that's a Nazi piece of wood you can see their knots in it here so the next test is the tip which is something I do use a lot of with there with a bushcraft knife and splitting it if I come in on that again where the groin and the bevel has gone so high it's meant that the tip here it's really quite thin it usually the angle will be a lot a lot sort of shallower angle it's quite a steep angle there which means it could break it could snap at the tip say so for this test I'm just gonna split the wood by holding the knife like this and basically stabbing down on it I like to hold it with the blevells away from me because if I cut and slip like that you've got arteries and everything in your arm here that could run across to the blade which I've ridden or not I was gonna cut myself I'd rather it be my fingers then my heart reso I always turn the blade away from me and she splits how's the tip tip is still intact yeah seems to be splitting fine it's enough to get it into sort of small small pieces for firewood and the tip seems to be yeah wish that we're still intact here let's try this piece she be splitting all right that spits fine tip is still intact the tip of it is still intact as well and if I clean it off there's no flex yet running back for me you know the bet the bevels not rolled over which is good Jen went further sticking everything's away from me because I don't want to be cutting in the triangle of death in here near my leg my femoral artery arteries say cutting away and given that this has such a high bevel I won't need to dig in much I won't need to change the angle in in much of the further stick it should just be fairly shallow because it's being that sort of saber groaning so we'll see Wow
that was you barely got to move it bit of a ben stretch bit here but tiny thing hose that is unreal the sharpness of that unbelievable it makes feather sticking so you easy it's one beast of a knife try really fine cows
being it's got a really high bevel I can get some really thin feather sticks going which great for rainy conditions when lighting with a fire steel you need to sort of thinnest wood possible designed by yourself as well when you designed your own knife and made your own knife I don't think anything could be more satisfying I absolutely love it okay one of the other things that's important with the bushcraft knife is having that 90 degree spine
that's just pure 90-degree right angle to work on a on a fire steel like this and you know it just gives you the best opportunity to be able to straight scrape sparks from it which this fuzzy back seems to be doing pretty well it's just my normal fire still that I use plenty of sparks coming off this there you go
we have fire it works people good old alex steel and his oh one steel i think that last one blew out say we will try again just made a baby feather stick yes small one can't expose the feathers a bit more cuz there's not loads you know there's one well it works fire Oh
well
you know if I were to have a proper father just tentatively build this up over all the curls really tough for this knife really chuffed with it so much better than I thought
but not not to be a feds to you Alec but it's awesome I didn't think I could design something that would actually work like this which is really cool so super pleased she's a beaut [Music]
[Applause]
[Music]
[Applause]
[Music]
[Applause]
[Music]
well what can I say other than thank you Alex for give me the opportunity to be able to create my own knife from scratch from a piece of o1 steel and turn it into something really practical so massive thanks to Alec and thanks to you guys for watching the video I'll be using this a lot more in future videos as well I think I'm gonna name it I've been thinking about this I think I'm gonna name this the lignum stealer lignum vitae handles Alec still helps me make it lignum stealer what do you think guys only knife it's cool to know it's the only knife like this in the world because I made it it's nice to have that exclusivity of it which is cool to know it's the only knife in the world that's sort of like this obviously there's loads similar but the fact that I made it is just awesome thanks Alec help me make the lignum stealer you guys go and check out his channel and I'll see you soon in the next video [Music]
[Applause]
[Music]
[Applause]
About the Author
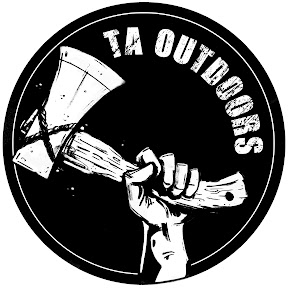
TA Outdoors
Bushcraft, Wild Camping, Wilderness Hiking Trips, Solo Overnight Camps, Shooting, Hunting and Backpacking. My dog joins me on some of the trips. His name is Jaxx.
My name is Mike. And I'm addicted to adventure...
Check out our other YouTube Channel TAFishing: https://www.youtube.com/user/TAFishing
More articles from this author
- Dorset Steam Fair 2016 | TAOutdoors
- Make a Pallet Wood Trash Can screen CHEAP & EASY | TA Outdoors
- Bushcraft & Fishing - Catch and Cook Deep Fried Fish on the Fire at The Bushcraft Camp
- Bushcraft Camp Update 11 - Hunting Tower, Dog House, Gate and Raised Camp Bed
- DIY TIPS - How to repair cracks in walls | TAOutdoors
- Making Bushcraft Chairs at the Shelter - Axe, Fire and Cooking too!
- Swedish Firetorch Cooking at the Bushcraft Camp
- Solo Overnight at the Bushcraft Camp - Fire, Cooking, Axe Work
- Bushcraft & Fishing - Catch N' Cook on the Camp Fire!
- NEW BUSHCRAFT CAMP!! + Tinder Fungus Fire
- Stoat Kills Rabbit on Camera! | TAOutdoors
- Cooking Pheasant at the Bushcraft Camp- Axe, Hunting Knife, Fire and Preparing Game in the Field
- How to Pluck and Gut a Pheasant | TA Outdoors
- How to make a Boot Rack from reclaimed Wood - TA Outdoors
- 4 DAY MOUNTAIN ADVENTURE! [TRAILER]
- Bushcraft Camp with my Dog - Wall Weaving, Campfire and Cooking Bacon on the Grill
- Bushcraft Cookset - Crusader MK2 Review & Test | TA Outdoors
- How to TRAP & KILL RODENTS | TA Outdoors
- Beachcraft - Survival on the Beach | TAOutdoors
- 3 Days Alone in the Wilderness - Fishing, Bushcraft & Foraging for Wild Food
- How to Track and Stalk wild Deer | TA Outdoors
- BUSHCRAFT & SURVIVAL CHALLENGE!! - Lighting a Fire with ONE HAND ONLY!
- Bushcraft Camp - Roof Pulley System for the Shelter + Fire Pit Cooking
- Making a Wine Rack from Free Pallet Wood, Cheap and Easy! | TA Outdoors
- Alcohol Stove Review | TA Outdoors
- Amazing fish recipe! Rainbow Trout Curry | TA Outdoors
- Sami-Style Oilskin Pouches for Bushcraft | TAOutdoors
- Bushcraft & Survival - Catch, Kill and Cooking Fish at Camp
- Bushcraft - New Knife, Flint & Steel Fire + Cooking at the Camp
- Emergency Survival Fire Starter - Char Cloth | TA Outdoors
- How to lace up a Hiking boot - Simple and Easy! | TA Outdoors
- Tree Root Survival Shelter - Fast Build, Minimal Tools
- Bushcraft, Hiking & Camping Backpacks - Which one is best for your needs?
- Bird Hunting - Shooting Pheasants | TA Outdoors
- Hunting with Ferrets | TAOutdoors
- How to make Natural Cordage from Tree Roots | TAOutdoors
- Bushcraft - Camp Fire with Pot Hanger, Coffee and Day Pack Gear Overview
- Solo Camping under a Tree Root - Stone Fire, Raised Bed, Cooking Tripod
- How to make a Bookshelf from Pallet Wood for FREE! | TA Outdoors
- Bushcraft Gear Hanger | TAOutdoors
- Bushcraft Fireside Camp Chat - Episode 1 | TAOutdoors
- Preparing My FORT for Winter - WINTER IS COMING!
- Foraging for Wild Food with my Dog | TAOutdoors
- Bushcraft, Camping & Hiking Tips | SHED SUNDAY EP. 4
- The Ultimate SURVIVAL TOOL - This thing is a BEAST!
- How to fix a bilge pump for boats | TA Outdoors
- Walking in the English Countryside | TA Outdoors
- Bushcraft Camp Update 5 - Secondary Shelter! | TAOutdoors
- Solo Overnight Camping - Tipi Tarp Shelter, Campfire, Grill Cooking, Knife work
- Bushcraft Camp Update 1 - Bushcraft Breakfast | TA Outdoors
- Introduction to Air Rifle Shooting | TAOutdoors
- Bushcraft - Winter Camp Fire Cooking in the Shelter
- How to skin a Rabbit | TA Outdoors
- Hunting Tower, Campfire & Stalking Deer with HD Cameras at The Bushcraft Camp
- How to cook fish - Awesome Curry Cod | TA Outdoors
- Beach Fishing and BACON!
- 12 Wild Camping Tips - How To Do Your First Solo Wild Camp | SHED SUNDAY EP. 1
- Making a Christmas Wreath from Natural Materials found in the Woods
- Bushcraft - Making a Fire Reflector the easy way | TA Outdoors
- Awesome water bottle tip! | TA Outdoors
- Camp Cooking at the Bushcraft Shelter on the Fire Pit and Grill
- 5 Tarp Shelter Setups for Bushcraft and Camping in the Woods
- Coastal Safety by The Coastal Survival School | TAOutdoors
- Beach Fishing and Cooking Fish over a Fire | TA Outdoors
- Solo Overnight at The Bushcraft Camp - Minimal Gear, Lightweight Campout
- Shotgun Shooting for Beginners | TA Outdoors
- Bushcraft Camp Update 2 - Log Seat Build | TA Outdoors
- Bushcraft Camp Update 3 - Improving Shelter | TA Outdoors
- How to Light a Campfire with Natural Materials and a Ferro Rod
- Bushcraft Camp Update 7 - Cooking Set-up | TAOutdoors
- Hiking in the Rain with my Dog - Warm Fire, Knife Work and Coffee at The Bushcraft Camp
- How to attract wild birds to your garden | TA Outdoors
- Bushcraft Camp Update 6 - THE FIRE PIT!! | TA Outdoors
- Easy to make Boot Remover | TAOutdoors
- Making a Leather Tinder Pouch by Hand
- How to make a Recycled Pallet Wood Coat Hanger & Mirror | TA Outdoors
- I Need To Get This Off My Chest...
- One Stick Fire CHALLENGE - Boiling Water with ONE STICK ONLY!
- Bushcraft Camp Update 4 - Perimeter Walls Finished! | TA Outdoors
- Bushcraft Shelters - Tree Root Shelter with no tools | TA Outdoors
- Make a Boat Bookshelf from Pallet Wood | TA Outdoors
- BUSHCRAFT: Den Building Diaries Part 1 - Natural Shelter | TA Outdoors
- Bushcraft Portable Sawing Horse, Table and Log Collecting Tips | TA Outdoors
- Bushcraft - Using an Ancient Saw on Logs + Cooking on the Fire at Camp
- How to cut wood | TA Outdoors
- How to make a Picket Gate from Pallet Wood | TAOutdoors
- 4 Day Solo Wild Camping Adventure in the Mountains
- Awesome Lamb Race!! | TAOutdoors
- Shooting - The Shooter's Stew | TA Outdoors
- Bushcraft Camp 2 - Wood Cooking Tripod, Latrine, Axe, Knife & Cooking on the Campfire
- Bushcraft & Fishing - Catch and Cook Fresh Fish on the Grill at The Bushcraft Camp
- Coastal Foraging For Beginners - LATE SUMMER | TAOutdoors
- Survival Tips - How to Kill, Fillet and Cook Fish | TAFishing
- Primitive Shark-Tooth Knife! Gutting and Preparing Fish at the Bushcraft Camp
- Fishing & Bushcraft - Catch, Cook, Fillet and Solo Overnight Wild Camping in the Forest
- One Man Tent Review - Yellowstone Matterhorn | TA Outdoors
- Taking my Dog and my Girlfriend to The Bushcraft Camp + Subscriber Gifts!
- Fishing: Catch n Cook in a CAVE & CAVE EXPLORING!
- Making a Mood Lamp from reclaimed Pallet Wood | TA Outdoors
- New Bushcraft Campsite Permission!
- Fishing & Bushcraft - Catch, Kill & Cook on a Campfire
- Making a Bushcraft Chopping Log | TA Outdoors
- DIY Survival Container from Recycled Bottle Caps! | TA Outdoors
- Solo Camping in the Forest - Fire Reflector, Tarp, Camp Fire, Axe and Knife Work
- Bushcraft Camp Update 10 - Natural Shelter expansion, Camp Construction, Axe, Knife & Saw work
- My Top 3 Fishing Knots - Strong, Reliable and ones that YOU NEED TO KNOW | SHED SUNDAY EP. 2
- New Bushcraft Camp Construction - Site Clearing, Firepit & Bacon Breakfast
- How to clean a Shotgun | TA Outdoors
- NO WAY! My Dad has taken over my Bushcraft Camp!!
- Overnight Hammock Camping in the Woods - Camp Fire, Tarp, Knife and Camp Tips
- Bushcraft Burden Strap | TA Outdoors
- Solo Bushcraft Camp in a Bug Infested Forest - Giant Ants, Spiders and Mosquito
- Axe Madness! Using 7 different Axes & Hatchets in the Woods + Camp Fire Cooking
- How to use a Woodburning Stove | TA Outdoors
- Wilderness Gathering 2016 | TAOutdoors
- Shooting Targets from The Hunting Tower at The Bushcraft Camp
- How to service an oil lamp | TA Outdoors
- Bushcraft Backpack Review - Snugpak Stamina | TAOutdoors
- Epic Camping & Survival Gear Giveaway!
- Shooting - Scoping a Deer Rifle | TAOutdoors
- Bushcraft Fire Lighting: Birch Bark Fire | TA Outdoors
- The Dangers of Shotgun Shooting at Close Range | TA Outdoors
- How to cook fish - Pan fried and baked Whiting | TA Outdoors
- Bushcraft Camp Update 9 - FIRE, SHELTER, COOKING & LOG STORE!!
- Epic Airgun Range!! | TAOutdoors
- Pike on a Bike! - Pike fishing tips | TAOutdoors Show
- 3 Day Camping Trip with my new Puppy! | TAOutdoors
- Day Camp - Hammock, Tarp and Chill in the Woods!
- How to Upholster a Chair -Simple and Easy! | TAOutdoors
- Hunting Dogs - Working The Woodland | TA Outdoors
- Bushcraft Camp Update 8 - Raised Camp Bed | TAOutdoors
- How to make Survival Fire with natural oil | TA Outdoors
- How to make a Plant Pot Stand from Pallet Wood | TAOutdoors
- How to build a FREE Garden Table from recycled pallet wood | TA Outdoors
- Bushcraft Knife Review - TBS Boar | TA Outdoors
- Clay Shooting at Bisley - Behind the Scenes of the Traps!
- 10 Knots for Bushcraft & Camping - How To Tie Knots | SHED SUNDAY EP. 3
- Bahco Laplander Folding Saw Review and Test | TA Outdoors
- Shotgun Silencer | TA Outdoors
- Bushcraft Shelters - The A Frame Shelter | TA Outdoors
- How to build a LOG STORE with PALLET WOOD! Cheap, Simple & Easy! | TA Outdoors
- Bushcraft Camp Shelter - Campfire, Long Hike with my Dog, Folding Wood Stove
- Catch n Cook - Spit Roast TIGER TROUT at The Bushcraft Camp
- Cooking Steak on the Grill at The Bushcraft Camp - Log Cabin Fire, Wood Splitting.
- Overnight Solo Camp in a Canvas Tent - Bushcraft, Axe Work & Campfire
- Bushcraft & Fishing - Catch and Cook Smoked Fish at the Log Fort Camp
- Bushcraft Camp Update 12 - Wood Roof Kitchen, Overnight Camp & Perimeter Wall Expansion
- Bushcraft & Fishing - Catch and Cook Pan Fried Fish on the Fire at The Bushcraft Camp
- Cooking on a Campfire in the Forest with my Dog.
- My First Aid Kit for Bushcraft, Fishing & Wild Camping
- Winter Camping in a Hobbit Tent and a Woodstove
- Building a Bushcraft Camp in the Forest - Wood Saw Horse, Tarp Chair, Log Cabin Notches
- Shooting with Shotguns and Air Rifles - Forest & Field
- Building an Off Grid Cabin in the Forest using Free Pallet Wood - A Wilderness Project
- Winter Hot Tenting Alone in the Forest with a Canvas Tent and a Woodstove
- Off Grid Pallet Wood Cabin Build in the Forest for Free - Wood Floor, Wall & Frame Structure
- Log Cabin Life: First Night in the Off Grid Pallet Wood Cabin
- One-Man Off Grid Cabin using Free Recycled Pallet Wood - Roof & Front Porch Build
- Log Cabin Life: Alone with my Dog in the Off Grid Pallet Wood Cabin
- Building an Imperfect Cabin in the Wilderness for Free - Recycled Pallet Wood Project
- Bushcraft ft. ALEC STEELE - Fire Lighting, Steak, Axe work - Epic Day at The Camp!
- Off Grid Cabin in the Forest using Recycled Pallet Wood - Woodstove Cooking & Log Store
- Cabin Life: Snow at the Off Grid Pallet Wood Cabin - Unboxing Mail
- Bushcraft Camp Update 13 - Primitive Shelter, Fire Pit Cooking, Overnight Camp
- Primitive Survival Shelter Build with Bare Hands - No Tools Needed
- Recycled Pallet Wood Cabin Build: An Off Grid Wilderness Project
- Off Grid Tiny Cabin: Pallet Wood Projects & Cast Iron Grill Cooking
- Building an Off Grid Cabin for Free to Save Money - Woodstove & Pallet Wood Bed
- Coastal Trip - Wild Plants, Bushcraft, Scouting for Fishing Marks & Channel Update
- Off Grid Log Cabin: Recycled Pallet Wood Project - Roof Extension & Sink
- Bushcraft Camp in the Snow - Fire, Shelter, Axe, Cooking Fish
- Bushcraft Camp: Full Super Shelter Build from Start to Finish.
- 3 Day Solo Winter Snow Camp - Bushcraft, Canvas Tent, Woodstove, Bowdrill
- Off Grid Pallet Wood Cabin: Opening Subscriber Gifts & Coffee Vibes
- Primitive Fishing with Horse Hair and a Bamboo Rod - Catching Fish with a Stick
- Off Grid Pallet Wood Cabin: Picket Fence Build & Woodstove Cooking
- My Dog's First Time in The Snow + Truck Update - New Mods
- Forging with ALEC STEELE: Hammer Technique, How To Forge for the First Time
- Cabin Life: Unboxing Fan Mail in the Cabin with my Dog (Incredible Gifts!)
- CATCH and COOK: FRESH TROUT on the Woodstove at The Off Grid Pallet Cabin
- Cooking at The Bushcraft Camp - Axe, Fire, Shelter, Wilderness Survival Tips & Grilled Kebabs
- Solo Overnight Camp - Stealth Tarp, Winter Camping in Cold Rain, 100 Year Old Tools.
- Making a Hatchet with ALEC STEELE - Forging with a Sledge Hammer!
- 2 Days Camping Alone in a Tent on a Clifftop - Fishing, Hiking & Filming
- Build a Bushcraft Dog House in the Forest Camp - Part 2
- Building an Off Grid Cabin using Free Pallet Wood: A Wilderness Project
- First Night Camping on the Roof of my Truck
- Pallet Wood Cabin in the Woods: Raised Vegetable Bed for Spring Garden at The Off Grid Cabin
- Solo Overnight Camp in the Mountains (Truck Camping) - Lake District Adventure | Ep.2
- Bushcraft Camp Update 14 - Tunnel, Fire Pit Upgrade, Blacksmithing, Wood Mallet Carving
- Camping in a River Valley - The Rain is HERE! | Ep 3
- Bushcraft Camp - Solo Overnight in the Super Shelter, Axe, Campfire, Lean to Shelter
- Taking my Wife and Dog to The Bushcraft Camp - Merch Release
- Solo Overnight Hammock Camping - Bushcraft, Foraging for Wild Food to Eat
- How to Prepare a Deer for Food | Survival Skills | Bushcraft | Wild Meat | Wilderness Living
- Primitive Log Cabin in the Woods - Moss Roof | Overnight Camp
- Pallet Wood Cabin in the Woods - The Last Unboxing Video
- Overnight Bushcraft Trip - Camping in a Debris Shelter - Cooking Wild Meat on Open Fire
- Bushcraft Camp with My Dog - Slingshot, Axe, Knife, Bowdrill Fire, Hunting Tower
- Bushcraft Skills - Axe & Knife Skills, Camp Setup, Fire (Overnight Camping)
- Fishing for GIANT CATFISH - New UK PB!
- BUSHCRAFT CAMP in the FOREST - Making PRIMITIVE GLUE, Repairing the SHELTER
- 3 Days Learning Bushcraft & Survival Skills
- Building a Dog House Shelter at the Bushcraft Camp (Part 1)
- 4 Day Camping Trip in the Mountains - Lake District Wild Camping Adventure | Ep 1
- Bushcraft Camp Update 15 - Wood Frame Roof Build (Super Shelter)
- Catch n Cook with FREE HOMEMADE CHARCOAL| Pan Fried Fish - FRESH CATCH!
- Catch and Cook BIG TROUT {GRAPHIC} GUT, CLEAN & FILLET | Cook on a STICK
- Gorilla Tape Shelter Build With My Dog | Survival Challenge | Bushcraft Camp
- Bushcraft & Fishing - Catch and Cook, Fillet, Clean Fish at The Bushcraft Shelter
- Bushcraft Day Camp in the Woods with a Canvas Poncho Tent
- Build a Tiki Bar from Recycled Pallet Wood - Off Grid Project
- Solo Camping 24hrs Alone Overnight on the Coast - A Solo Adventure
- Off Grid Cabin - Building a Free Pallet Wood Outhouse in the Woods
- Leatherwork for Beginners - Basic Skills (Tutorial)
- Bushcraft Camp - Destroying Structures ready for Wood Roof Shelter Build
- Off Grid Cabin in the Forest - Roast Chestnuts, Woodstove (Camp in the Woods)
- Camping in the Woods like ROBIN HOOD - Military Poncho Tent
- Cave Camping: Cooking Snails, Fish, Wild Plants, Fire (Survival)
- Bushcraft & Fishing - How To GUT & CLEAN FISH | BUSHCRAFT BOWDRILL FIRE | BAKED FISH
- Her First Time at the Cabin: Woodstove Cooking (Off Grid Pallet Wood Cabin)
- Off Grid Pallet Wood Homestead Build - Pallet Wood Projects at The Cabin
- Make a Leather Tinder Pouch | Bushcraft Kit (Tutorial)
- Bushcraft Camp Update 16 - Thermal Shelter Upgrade (Survival)
- 2 Day Bushcraft Camp with a Dog - Deer Hide Beds, Camp Fire Cooking (Forest Camping)
- 3 Day Camp in the Woods - Bushcraft Shelter, Dog, Wool Blanket (STORM FORCE WINDS)
- Make a Survival Zip Pull from Paracord (Tutorial)
- Saving Our Off Grid Cabin in the Woods (TOTAL RE-BUILD)
- Solo Bushcraft Overnight - Swedish Axe, Canvas Lavvu, Wool Blanket
- Bushcraft Camp with my Dog - T-Bone Steak on the Camp Fire (SHOW US YOUR STEAK CHALLENGE)
- Camping in a Debris Shelter (Bushcraft) - Lanterns, Log Bench, Deer Hide Beds
- Cooking at the Off Grid Cabin in the Woods - Woodstove, Firepit (WINTER PREPARATION)
- Bushcraft Camp Update 17 - Stone Fire Pit, Cooking, Knife Sharpening (SPIDERS)
- Camping Overnight at The Bushcraft Camp & Off Grid Cabin in the Woods
- Bushcraft - Duck, Flint and Steel, Traditional Gear (Field Sports)
- 20 Minute Bushcraft Shelter (REAL TIME)
- Bushcraft Camp with a Subscriber - Deer Meat, Axe, Knife, Camp Food
- Bushcraft Camp: Full Super Shelter Tour (Tower, Ladder, Shelter, Roof, Log Store, Raised Bed)
- Off Grid Log Cabin with Moss Roof - Cruck Frame Shelter (Overnight Camp)
- Goodbye Bushcraft Camp. WE ARE DONE.
- 2 Day Bushcraft Camp in a Tipi Shelter - Woodstove, Deer Hides, Axe (Camp Craft)