Bushcraft Axe Work: Leather Collar
Description
In this video we build a simple leather overstrike collar for the Gransfors Bruks Small Forest Axe.
Become a Patron:
https://www.patreon.com/MCQBushcraft
Bushcraft Basics Blog - http://www.mcqbushcraft.co.uk/bushcraft-basics/
Amazon Store:
UK Store - http://astore.amazon.co.uk/mcqbushcraft-21
US Store - http://astore.amazon.com/mcq-20
Merchandise:
T-Shirts - http://mcqbushcraft.spreadshirt.co.uk/
Connect On My Website - http://www.MCQBushcraft.co.uk
Connect On Facebook - https://www.facebook.com/MCQBushcraft
Connect On Instagram - http://www.instagram.com/mcqbushcraft1
Connect On Twitter - http://www.twitter.com/MCQBushcraft
Tags: woodland,forest,mountains,river,lake,tinder,Survival,Bushcraft,survivor,knife,knives,valley,axe,camping,tent,footwear,hunting,fishing,backpack,clothing,boots,primitive,nature,shelter,shooting,shotgun,rifle,rucksack,flashlight,torch,craft,plants,trees,education,wilderness,family,hobbies,fun,animals,game,Leather Crafting
Video Transcription
hi there guys is Mike from mcq bushcraft here an amazing the coppice again today mainly because I want a flat surface to work on and this stump here this populist stump and provide me with quite a nice flat surface as a workstation because in today's video we're going to be making something and what we're going to be making is a leather collar for a bushcraft acts a little bit like this one here this is my X here and it's a hold of his classic hunter and you can see that I've put a leather collar just around the shoulder of the axe then it's quite a short one because all it needs to do is protect this portion which is near the actual blade of the axe near the head so if we do strike something in a particularly old way or you might not be at the top of your game you'll be protecting that shoulder that with that leather collar but I've got another axe in front of me here and this is Grands Falls Brooks small forest axe and this one isn't mine it's a good friend it's this he's asked me to put a leather collar on for him not particularly big one just one that comes down to about there just enough to protect this shoulder and this axe has seen some action
my friends are professional woodsmen he works out here almost every day has a whole range of axes that he owns this is one of these axes that he carries around with him amongst many others and it's taken a real beating I think we'll put a leather collar on it and clean it up a bit
but it's going to need a few bits of equipment first before we can actually do that
so I've got a number of items in front of me they can help us build this leather collar I'll just run through them now so I've got a mug of water here and that's there to help us soak the leather so when we've cut out the piece we're looking for it's going to help us wet form it and actually mold it around the shoulder of the axe and also help it conform to this curve that we have on the head of the axe which you can see I've done to mine and when it's wet you can actually tuck it in even if you haven't got it particularly accurate and it'll shape very nicely and when it dries it'll set in place and shrink and be pretty stiff and it won't move at all so that's what the water is going to help us with I've got my maintenance kits or something in there that I need I've shown this in many videos and is a whole variety of items in there designed to maintain all the gear I bring out with me and there's beeswax and fats and needles and thread various things in there and something may come in handy so I've just got that at hand with me I've got a hole punch you can use an awl on a penknife or even a vintage all if you may have one in a toolbox even a nail to punch the holes but I've just got this dedicated punch that I had at home and it's going to obviously be pretty useful for punching holes in pieces of leather to thread the cord through and the cord itself is a 2 mil wide by 1 mil deep leather shoelace that I got from a cobblers it's always a very nice quality leather you can buy this stuff off eBay reams and reams of the stuff online but I generally like to see it before I buy it because often it can be of a poor quality when it turns up sometimes so this is a particularly good quality thin but strong leather lace and that's quite important
I've got a notepad of box cutter and the notepad is going to be particularly useful as you'll see later because it will actually help us trace the contours of the ax head just here and helps achieve this curve on the actual leather itself but these two items here on essential you could use an ordinary bushcraft knife and you could skip the notepad pad and make it another way but I've just brought them out with me because it does help you out the piece of leather I've got here is a premium piece of leather very good quality traditionally oak tanned in the UK and made from organic cattle and that wasn't my first choice usually for me it's old boot leather leather jackets and anything I can get my hands on but I met some people in this woodland just by the off-chance and they came to look at what I was doing and everything and they run a company called organic leather which specialized in getting organic cattle and making traditionally out tanned pieces of leather like this I didn't realize it but it takes one year to make one cow basically which is why it's so expensive and they kindly gifted me a large sheet about this big you think costs about 40 pounds but I've made great use of this piece of leather and made all manner of different things out of it and it's been wonderful to work with it really comes up well and it's very tough stuff I mean I've already hit this a few times on pieces of wood and it's just scratched it rather than actually cut in and bring up all of the grain of the leather but if you can't afford a premium quality bit of leather like that much like I can't most of the time then old boots are the way to go if you can get your hands on old boots then you know they'll be absolutely brilliant for making ax collars with because it's thick and strong but I will put the link in the description to organic leather they do some very nice bushcraft belts I've seen them firsthand and I'd like to get one at some point but they are very good quality but some yeah the links in the description I've also got a straight edge here so instead of bringing a ruler out with me I'm just going to use the Boesel and that's really the kit I'm using so all this stuff aside if your experience with leather work and you've got a lot of tools to do crafts with at home you can take this any which way you want we're just going to make a basic collar in this video and there are other things you can do afterwards I can pregnat the actual leather with beeswax to make it very resilient to water you can even blacken the edges as well like I've done on this one here and really kind of get some contrast in there and make it look very nice but at the end of the day it's designed to take a beating not really look too pretty because you'll be disappointed when you actually damage the leather if you make it look too nice because it will take a beating but all this aside let's crack on make this collar so when I start off making these sorts of things I never really measure things out too well because when we soak the leather later it can be stretched but you can see there I'm just wrapping this round pretty loosely and somewhere around there is where we're going to be having in terms of the DAP probably going to go somewhere around there so it doesn't need to be too deep I usually go about two and a half inches so what I'm going to do now is dip this in the water and let it soak for a little while I'll just leave that in there for a few minutes so our leathers been soaking in here for a couple of minutes now and it's much more pliable than it was before there's obviously some water in there that's looking a lot better much easier to work with so we'll put the water to one side just go sheet of paper from our notepad and I'm actually going to wrap it around the ax like that and just mark off the actual curves of the head just like that because the heads are hand forged there will be a difference but this just gives us a rough idea of where those two curves are and the paper is thinner than the leather but that's not a problem because we've even soaked the leather it will allow us to form it so there's a slight deviation in the actual curve itself between the leather and this head then we can actually wet form it and move it into shape so it's just to give us a rough outline what I'm going to do now is actually cut act roughly put this in the center our mark the center first was by putting this here I'll have to ignore all the tractors in the background I'm in the coppice a noisy place just run my finger down there very lightly just like that just to mark the center along there put that roughly in the center there I'm literally just going to cut around it with my knife so I'm doing it really lightly at first because this Stanley knife isn't particularly good but what it will do is it will just mark the leather for me enough for me to then remove the paper away and actually cut it properly and I can use my Jack claw bushcraft knife to do some really nice cutting later on and carve away pieces of the leather so that's mark did enough now we can actually cut the leather away don't worry if there is a slight difference as I say that can all be sorted out later just getting that basic shape sorted at the moment
that's what I'm doing now it's just cleaning up the edges I've got a very sharp knife so it means I can do some fine work with it and I actually do is taper in so we get away the actual inner edge and that allows me to flatten it against the head a bit more so when we wrap for this round you can see that there's still parts here that aren't quite right we've got the depth here okay and the other side and we've got some some sort of leather just hanging over there again it's not particularly good but the rough shapes there that's all I really care about at this point you can make it all look fancy and match it all up properly later and we can resect the leather again if you want to sort of make it a bit more pliable but you can see that there's just too much material at the back and the way that the handles shaped is it runs down like this so the material needs to be shaped in a fashion so it ends up looking a little bit like that so it means going to have to cut it at an angle all the way down to slightly wider there as in what we're removing is wider than what we're taking away there so take a triangle of material away and I'm just going to do this bit by bit with no real measurement again because it's wet leather it can be stretched and I can manipulate it later with the cord that I Tyron to actually stretch it into place and then shape it so I'm just going to take away a little bits at a time but just to give me a rough idea what I'm looking to get rid of I'm going to run my finger down like that so it looks like we're going to need to get rid of that much off of that side that's about right so you can see that there's quite a gap there as it runs round and that can be stretched now and pulled very tight and then when the leather actually dries it'll be even tighter so I think we'll work with that from the time being that's looking okay so we're going to want to punch some holes now and start stitching it in place if we look at the thickness of the calls we've got here the leather cord two mil wide one mil deep so we're going to go with a small hole and that way we can actually force the cord through in the hole as it as the leather dries we'll tighten around the actual piece of cord this is a bit better than punching a great big hole which will just look pretty ugly and stretch open and it won't really look particularly good or seal very well you'll get lots of dirt in there
so I'm punching the holes about two mil from the edge and they're probably spaced apart about four mil there we go so we'll start threading the cord through and then we'll start manipulating the leather so it flushes around the edges and looks a little bit a little bit better so I've got a piece of antler there and I'm just using it to slightly stretch the whole knot because I want the hole to be too much bigger but just because what that will do is will stretch it temporarily so the cord is able to go through and then it will form around the cord and be a bit tighter I'm just going to sharpen off a bit of cord so it's easier to thread through I'll do the same the other side and we're going to do a cross-stitch so we're going to go through and then through again and you can see I'm putting the flat bit of leather so it's not going to be like that with the 1 mil piece sitting like that it needs to be flat and then this will cross like that and this will cross like that and it will continue down I'll show you so you can see there we've got two crosses and then the spare holes at the bottoms have five holes in total with two two holes per cross obviously are on one side that is so four holes four holes and then two at the bottom and those will cross over and tie together and that I'll finish it off and we won't use these together permanently you'll leave it so that you can tighten it in the future if things need adjusting over time so what we can do now is try and thread that on and start manipulating it because this piece of cords twisted here I'm just working out how I can untwist it yes you should rotate the cord because you want to keep it as flat as possible those bits there that are bursting at the moment you can manipulate those with a piece of antler but I actually flattening the leather while it's still wet and you can persuade the gap to actually close up PC by pushing the leather and pushing again that side you can see it's starting to close and this is what I mean by manipulating the leather you won't worry about this bit at the bottom but you can see we've kind of got what we're looking for apart from this part here which is a bit of a shambles I would be happy with that I'm not happy with that but that's just unfortunately due to me cutting it badly it's okay isn't my axe there we are so I've decided to cut that piece off just there because I'd cut it a little bit thin on one side and it just wasn't quite right I didn't like it you don't necessarily need it to tuck up that's more here that that needs to protection literally just this portion of the wood there it needs the actual guard on but I usually make things quite flush just to make them look a bit better but it wasn't so steep on the halter for Zack's you see so you don't need so much leather suddenly coming up Brown here that isn't being held in too tightly by anything so it can start to get a bit iffy I've just cut it away like they're some of the ones you buy commercially will just be a strap like that a square strap but it's quite nice to put this contouring in to offer extra protection and to act as a dust guard sometimes I'm just leaving that bit open and I've settled with the four holes and the two crosses on the cross stitch so I think that would be okay but we're just going to tighten all this up and start manipulating all this leather around here so it's much more flush with the head so when it's set that's nice and hard and stays that way you can round any sharp edges as well just by rubbing the leather with the with the antler or your finger and you can even splack in it it's a later state which we may have a go at later I think what we'll do now I mean this is set in place you can see it there looks quite good it's not going anywhere it just needs to dry but we're just going to blacken the edges of the leather a little bit in all those little gaps and I usually just use black ink for that although there are special products you can buy to do it so I don't worry too much about going all over the leather I usually just rub it with my finger and with this ink I usually darken areas that I want to darken up a bit more on other projects that are supposed to look a bit more athletic than this but it just allows you to darken the edges of the leather a bit and stop it looking so sort of rugged really in a in a respect or unfinished
this part here is best done beforehand because you know you can end up coloring in your axe handle if you're not careful and it just allows you to be a bit more thorough when you do it before hands but I'm just kind of doing it afterwards because I'm seeing a pretty breezy job of this so there are a number of ways of finishing off this cord here and all I generally do is cut it just like that and then sometimes I put just a dab of glue on the leather and seal it there that can be broken away and then tightened and unstitched at any time and you can always keep some of this cord Andry stitch it if you have to repair it and take it off but that will hold there and when this dries and tightens up this won't loosen up and it'll be absolutely fine it's looking quite nice so it's been a short space of time we've made quite an effective leather collar for our Graham force Brooks small Forrest axe here and I think I'll do a little bit more to this I'll sharpen it put some oil on the handle and seal around the head with beeswax which is what I've done with this here just to protect it from moisture but there is something I need to mention before you put on the collar what you want to do first of all is rub beeswax or some kind of wax or oil just in the wood underneath the collar and what that will do is it will do two things if you use beeswax it'll add quite a lot of friction under the leather and it'll stop the leather slipping even years down the line it will act as a vise and keep it there especially as the leather dries and tightens around the beeswax and it'll also stop moisture you can seal wax into the actual leather itself which is a technique that you might need to do at home but again another method you can use for stopping the elements getting in but to be honest with you I've run with a setup similar to this for years never had any problems of moisture or moisture gathering in the handle and rotting the actual wood so no problems there
but I use this same technique that I've made this collar today with all the leather work that I've got here in front of me obviously I didn't make the sheath and some of the items here but you can see the stitching on the Farah rod and the cover on the actual Lum hook knife there
I'm also the hobo fishing kit and this pot of Wax so similar techniques can be used across the board and you can darken the edges with ink so a lot can be done even when you don't have the right equipment there are specific bits of gear out there for leather work I don't really own anything particularly special but I just get by on scrap and whatever I can find and you can make an awful lot with that and get creative with it so I hope this videos helped out just a very basic video on making a collar for an axe like this a bushcraft axe and this should protect it just fine so thanks for watching guys and if your interesting any other gear that I use in this video please do have a look at the Amazon links in the descriptions below and the other links that I've put in there and they're also relevant social media links t so thanks again and I'll see you again in another video
take care
About the Author
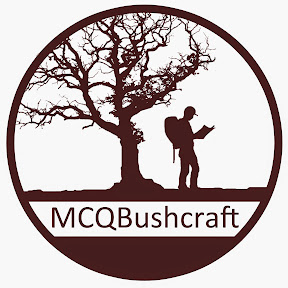
MCQBushcraft
I'm a UK based outdoorsman who started hunting and fishing with my friends when I was young.
Educating yourself about your surroundings and having the core skills to sustain yourself using your environment is a lost curriculum in the United Kingdom. We are well provided for, so well that "why do anything if somebody else will do it for you". This lifestyle has drastically disconnected people from having the knowledge and skills required to spend even one night in the woods and not get hungry.
I love being outdoors and have never lost the desire to learn and practice skills that I get a sense of natural connection from. Hunting hangs controversy in the minds of many, but in my eyes there is nothing more natural if you choose to eat meat. I appreciate that not everybody hunts in moderation though.
Thanks for reading
Michael McQuilton
Private Sponsorships: http://fbit.co/u/MCQBushcraft
More articles from this author
- Bushcraft Containers: Pine Pitch & Spruce Cord
- Bushcraft Basics Ep06: Choosing a Backpack
- Hunting: Pigeon Shooting with a Shotgun
- Bushcraft Basics Ep12: Knife Safety
- Bushcraft Basics Ep15: Personal Med Kit
- Bushcraft Shelters: Hammock & Tarp Setup
- MCQBushcraft 2015 Channel Update
- MCQBushcraft Q&A: Ep01 - About Me
- Bushcraft Fire Lighting: Leather Tinder Pouch
- Wild Camping & Bushcraft with ZedOutdoors
- Bushcraft Basics Ep10: UK Knife Law
- Field Dressing a Brown Hare
- Bushcraft Basics Ep20: Making Fire Feather Sticks
- Bushcraft Fire Lighting: Cramp Ball Fungi
- Bushcraft Equipment: The Hidden Woodsmen
- Bushcraft Fire Lighting: Woodburning Stoves
- Bushcraft Shelters: Quick Deployment Tarp System
- Bushcraft Equipment: Maxpedition Condor II Pack
- Bushcraft Basics Ep13 - Knife Maintenance
- Hunting: Shotgun on Pigeon & Rabbit (Two Day)
- Field Dressing Game: Duck Whole Bird
- 200,000 Subscriber Giveaway Prize Draw Winners!
- Solo Three Day Hunting & Bushcraft
- Solo Five Day Hunting & Bushcraft
- Bushcraft Containers: Frying Pan
- Bushcraft Foraging: Dehydrating Mushrooms
- Field Dressing Game: Pheasant Breast Only
- Wood Carving & Crafts: Bushcraft Tinder, Skulls, Knives, Carvings & Furs
- Bushcraft Foraging: Piptoporus Betulinus
- Wood Carving & Crafts: Tinder Pouches & Leatherwork
- Bushcraft Fire Lighting: Using a Firesteel
- Bushcraft Camping: The Lake District
- Hunting: Slingshot Aiming Techniques (Aimed)
- Hunting: Grey Squirrels with a Shotgun
- Bushcraft Equipment: 'Old Kit' September 2013
- Bushcraft Foraging: Pignuts
- Camp Cooking: Crayfish
- Wood Carving & Crafts: Alder Spoon & Kuksa
- Coastal Bushcraft: Two Days Fishing & Camping
- Bushcraft Foraging: Alexanders
- MCQBushcraft Hunting & Shooting Compilation
- Shooting Gear: My Game Bag & Goose Gun
- Bushcraft Knives: ESEE Izula II Firesteel
- Bushcraft Camping & Cooking on Embers
- Hunting: Slingshot Aiming Techniques (Intuitive)
- Bushcraft Fire Lighting: Fire Kit & Bowdrill
- Camp Cooking: Roasting Pheasant over a Fire
- Wood Carving & Crafts: English Yew ladle
- Bushcraft Foraging: Saffron Milk Cap
- Bushcraft Fire Lighting: Introduction
- Shotguns & Hunting Gear
- Hunting: Grey Squirrel & Woodpigeon
- Bushcraft Basics Ep05: Land Access Northern Ireland
- Bushcraft Sweden: Ep05 - Four Days Canoeing In The Wilderness
- Bushcraft Foraging: St George's Mushroom
- Bushcraft Basics Ep16: Field Journal
- Bushcraft Basics Ep08: Water Contaminants & Pathogens
- Bushcraft Foraging: Wild Edibles of Spring
- Bushcraft Fire Lighting: Finding Fatwood Heart Root Tinder
- Bushcraft Knives: ESEE 90 Degree Spine
- Bushcraft Knives: Using Animal Fats
- Bushcraft Shelters: Weaving a Grass Bed
- Bushcraft Basics Ep03: Open Access Land England & Wales
- Bushcraft Knives: ESEE Paracord Sheath
- Bushcraft Sweden: Ep02 - Cliff Top Camp
- Bushcraft Foraging in the Woodland
- Bushcraft Fishing: Using a Hobo Reel
- Bushcraft Knives: Camp Knife & Neck Knife
- Bushcraft Basics Ep19: Finding Fatwood Tinder
- Bushcraft Equipment: My Gear & How To Use It.
- Bushcraft Basics Ep07: Water Containers
- Jeep XJ Off Road Crayfish Recovery
- Bushcraft Foraging: Tapping Birch Water
- Bushcraft Foraging: Dryads Saddle Mushroom
- Bushcraft Basics Ep02: Private Land England & Wales
- Hunting: Pheasant & Wood Pigeon
- Bushcraft Basics Ep18: Ferrocerium Rod Technique
- MCQBushcraft Q&A: Channel Update 2016
- Bushcraft Equipment: Maxpedition Xantha
- Bushcraft Sweden: Ep01 - Gear Overview
- Bushcraft Foraging: Navelwort
- Bushcraft Sweden: Ep04 - Hunting Capercaillie & Black Grouse
- Bushcraft Knives: Jacklore Knives
- Bushcraft Sweden: Ep03 - Canoeing & Fishing In The Wilderness
- Bushcraft Basics Ep14: Knife Sharpening
- Bushcraft Camping: Woodland Wild Camp
- Bushcraft Basics Ep04: Land Access Scotland
- Bushcraft Containers: Pot Hangers
- Bushcraft Fire Lighting: Finding Fatwood Pine Shoulder Tinder
- Bushcraft Basics Ep09: Water Filtration & Disinfection
- Bushcraft Clothing: Outdoor Clothing & Layering
- Bushcraft Clothing: Deerhunter Waterproofs
- Bushcraft Foraging: Hawthorn Fruit Leather
- Bushcraft Fire Lighting: Fly Repellent
- Field Dressing Game: Pheasant Whole Bird
- Essential Knots: Bushcraft & Tarp Setups
- Bushcraft Basics Ep17: Fire Lighting Tools
- 200,000 Subscriber Giveaway Entry Video (CLOSED)
- Field Dressing Game: Rabbit for Meat & Fur
- Wood Carving & Crafts: Bushcraft Fire Lighting Set
- Bushcraft Foraging: Tapping Birch Water (tree friendly)
- Bushcraft Foraging: Hairy Bittercress
- MCQBushcraft Q&A: Channel Update 2017
- Bushcraft Basics Ep11: Bushcraft Knives
- Bushcraft Fire Lighting: Essential Technique of Bow Drill Friction Fire
- Bushcraft Foraging: Ramsons
- Clay Pigeons Shooting With The Knife Makers
- Bushcraft Foraging: Seasonal Edibles Ramsons
- Foraging & Cooking Dryad's Saddle
- Bushcraft Foraging: Wild Edibles of Summer
- Coastal Bushcraft: Trotline Fishing
- Field Dressing Game: Grey Squirrel
- Bushcraft Axe Work: Sharpening
- Bushcraft Fire Lighting: Tinder Fungus
- Hunting: Wood Pigeon & Grey Squirrel
- Coastal Bushcraft: Foraging & Cooking Shellfish
- Bushcraft Axe Work: Safety & Technique
- Bushcraft Knives: Field Sharpening & Stropping Kit
- Bushcraft Equipment: Swedish LK35 Backpack
- A Windy Day Hunting Wood Pigeons
- Bushcraft Basics Ep01: Introduction
- Bushcraft Knives: The Field Master
- Hunting: Slingshot on Grey Squirrel
- Bushcraft Equipment: Catapult Target Practice
- 200,000 Subscriber Giveaway Announcement
- Hunting: Wood Pigeons Early December
- Bushcraft Containers: Basket Weaving, Clematis
- Bushcraft Equipment: Full Kit July 2014
- Bushcraft Shelters: Camp Construction
- Bushcraft Containers: Washing & Sterilising
- Field Dressing Game: Wood Pigeon
- Bushcraft Foraging: Lesser Celandine
- Bushcraft Fire Lighting: Make Fire With Fatwood Tinder
- Bushcraft Basics Ep21: Choosing a Bushcraft Saw
- Wood Pigeon Decoying Over Maize Stubble
- Part 1: Fitting a Wood Burning Stove to a Canvas Bell Tent
- My Experiences on YouTube & Plans for 2018
- Part 2: Fitting a Wood Burning Stove to a Canvas Bell Tent
- Jeep XJ Overland Build Ep01: Vehicle Overview
- Jeep XJ Overland Build Ep02: Workshop & Tools
- Jeep XJ Overland Build Ep03: Rear Bumper Upgrade, Sliders & Tie Ins
- Winter Bivi Camping & Cooking Wood Pigeon Curry
- Jeep XJ Overland Build Ep05: Ruffstuff Frame Stiffeners Install
- Traveling Northern Europe 4x4 Ep02: Our Journey & Living in a Jeep
- Jeep XJ Overland Build Ep04: Tyre Carrier, Bumper Supports & Rear Stiffeners
- Traveling Northern Europe 4x4 Ep08: Rooftop Tent Camping Norway - Part 4
- Jeep XJ Overland Build Ep06: Box Rockers, Slider Sill Replacement
- Traveling Northern Europe 4x4 Ep04: Rooftop Tent Camping Denmark
- Traveling Northern Europe 4x4 Ep07: Rooftop Tent Camping Norway - Part 3
- Traveling Northern Europe 4x4 Ep05: Rooftop Tent Camping Norway - Part 1
- Traveling Northern Europe 4x4 Ep06: Rooftop Tent Camping Norway - Part 2
- Traveling Northern Europe 4x4 Ep03: Rooftop Tent Camping North West Germany
- Offroad Truck Camper Build Ep07: Ruffstuff Front Stiffeners & Front Axle Overhaul
- The end of MCQBushcraft as we know it.......
- Traveling Northern Europe 4x4 Ep01: Rooftop Tent Camping The Netherlands
- MCQBushcraft Traveling Europe 4x4 Ep09: Finding our New Home in Sweden
- Campfire Cooking 'Show us your Steak' Men's Mental Health